Быстросохнущий цемент: свойства быстротвердеющего цемента
Востребованность бетонного состава для строительных работ обуславливается набором отличных физико-технических характеристик. Ранее усложнял использование обычных смесей на цементной основе долгий срок их застывания (отвердевания). Производители успешно справились с этим, разработав быстротвердеющие цементы с малым временем гидратации. Заменив обычный строительный портландцемент на БТЦ, можно осуществлять строительство гораздо быстрее.
Составные компоненты
Компании выпускают данную разновидность материалов по индивидуальным производственным рецептам, скрывая подробности состава. Однако в базовую консистенцию входят стандартные компоненты. Набор свойств, присущих разновидностям быстротвердеющего порошка, дают следующие добавки:
- негашеная известь;
- углекислый калий;
- соляная кислота;
- различные соли.
Исходя из их процентного соотношения, скорость застывания и набора высшей прочности может варьироваться, но процесс всё равно протекает максимально быстро. Также производство не исключает применение различных минеральных добавок и прочих компонентов (не минерального происхождения) для повышения пластичности, обеспечения гидроизоляционной способности, химической устойчивости и других качественных показателей.
Способы изготовления
На сегодняшний день быстросхватывающиеся цементные порошки продаются в двух видах. Для первых производственная технология предусматривает добавление компонентов, способных ускорять схватывание и твердение, до продажи. Другие же цементные растворы замешиваются непосредственно во время строительно-ремонтных процедур. Предусматривается добавление специальных жидкостей в комплект поставки этой разновидности порошка.
Сферы эксплуатации
Зачастую оперативно сохнущий порошок используется при необходимости восстановления какой-либо конструкции. В зданиях и сооружениях такой стройматериал необходим для гидроизоляции, шпаклевки, герметизации различных дефектных участков поверхности, ремонта на фундаментах и цоколях.
Современные (новые) подходы к архитектуре предполагают, что такой бетон может заливаться под анкерные крепления, металлоконструкции и прочие детали, а также применяться в печной кладке, лепнине и установке колонн.
Марочная принадлежность
На отечественном рынке выпускается две основные марочные разновидности порошка — М400 и М500. Каждая марка из указанных позволяет осуществлять вышеописанные процедуры. Различаются они лишь выдерживаемым уровнем нагрузки (самым высоким в сравнении с порошками меньшей марочной принадлежности). При специализированных видах строительной деятельности большое внимание уделяется именно 500-му номеру.
Ключевые особенности
Как уже было сказано, ключевым достоинством таких порошков является их мгновенное застывание. Если в базовых разновидностях требуется не менее часа для первичного схватывания, то в быстро затвердевающих на это уходит от 1 до 5 минут. Причем в таких условиях бетонные консистенции самоуплотняются, заполняя щели и отверстия. Соответственно, в кратчайший срок можно восстановить целостность любого перекрытия. Также это порошки, применяемые при повышенной влажности и низких температурах.
Нюансы эксплуатации
Фактически приготовление рабочей консистенции ничем не отличается от стандартного. Всё также клинкерный помол смешивается с водой, песком и твердыми наполнителями (при необходимости). Но в этом случае необходимо помнить про активные компоненты, вызывающие схватывание в течение 1-5 минут. Соответственно, израсходовать заготовленную массу следует за указанное время. Своевременно распределив её по обрабатываемой площади, получают качественное покрытие.
Разводить схватывающийся стройматериал нельзя: он потеряет свои качества. Внимательно следите за содержанием компонентов в заготавливаемой бетонной массе, пользуясь инструкциями от производителя. Заведомо подготовьте обрабатываемую поверхность, очистив её. Жидкость добавляйте в замес равномерно и медленно, используя при этом строительный миксер на малых оборотах, чтобы заготовить оптимальную консистенцию.
Закупка качественного стройматериала
Обратившись к услугам группы компаний «АльфаЦем», вы гарантированно сможете купить высококачественные строительные порошки для выполнения вышеописанных процедур. Мы обслуживаем весь Центральный федеральный округ РФ, а также г. Москва, оперативно доставляя заказы, соблюдая права клиентов и исполняя собственные обязанности. Продукцию от ведущих отечественных и зарубежных заводов вы сможете получить на выгодных условиях.
Внимательно изучите разделы нашего сайта и прочитайте тематические статьи, чтобы подробнее узнать обо всех нюансах эксплуатации данной категории стройматериалов. Оставляйте свои заявки или звоните нам напрямую для обсуждения деталей заказа. Компетентные менеджеры оперативно реагируют на каждое обращение. Ждём вас!
Быстросохнущий цемент – классификация и применение
Во многих ситуациях использование обычного цемента неэффективно и неудобно, потому что приходится долго ждать отвердевания, а это не всегда представляется возможным, к примеру, работы на улице в слякотную или дождливую погоду. Именно поэтому используют специальные быстросохнущие цементы. Быстрое отвердевание придают ему специальные минеральные добавки, способные при контакте с водой очень быстро кристаллизоваться, создавая собой монолит. Такие растворы способны (в зависимости от толщи укладки) отвердевать за 3 суток, максимум за 28, но это уж очень мощный слой цемента при очень сложных погодных условиях. Ведь его можно применять, когда на улице ниже -27 градусов по Цельсию!!! Быстросохнущий цемент применяют при изготовлении железобетонных изделий, морозоустойчивого бетона, а также при аварийных восстановительных работах.
Важно знать, что такой цемент нельзя долго хранить, не применяя его, так как через 1-2 месяца пропадает свойство быстрого отвердения. Также не стоит его использовать в агрессивной, химической среде, потому что минеральные добавки неустойчивы к воздействию кислот и щелочей. Бетонные конструкции на основе таких цементов нельзя применять для массивных сооружений из-за перепадов температур внутри и снаружи изделия.
В последнее время добавки, способствующие быстрому отвердению, усовершенствовались, за счет чего их количество в растворе стало всего от 2 до 5%, причем они вдобавок увеличивают прочность изделий на целую ступень. Благодаря этому, сократились траты на электроэнергию и топливо, так как теперь заводам не нужно дополнительно пропаривать изготовленные конструкции.
Быстросохнущие цементы бывают белые и цветные. А серый цвет стандартного цемента объясняется содержанием в его составе окислов марганца и железа. Для получения белого цвета используют такое сырье, как каолиновая глина или мел, в которых марганцевых и железных соединений очень мало. Белые цементы бывают двух марок — «400» и «500». У цветных марки те же, но добавлена еще «300». Разноцветные цементы получают путем добавления в их состав красителей, гамма их абсолютно разнообразна. Но за такой симпатичный внешний вид приходится платить не такой хорошей устойчивостью к низким температурам, как у белых, низкой сопротивляемостью к коррозиям, а также больше подвергаются усадке.
Также различают цементные порошки, которые впитывают или же, наоборот, отталкивают воду. Это легко проверить, достаточно капнуть водой на горстку порошка. Если вода впитается в первые секунды, значит цемент впитывающий, или гидрофильный, а если в течение 4-5 минут не впиталась, значит, порошок отталкивает воду, то есть гидрофобный. Из такого «антиводяного» цемента бетон будет служить дольше, поэтому он применяется в более ответственных конструкциях. К тому же он не боится долгого хранения.
Есть еще и монолитный цемент, который даже за использование на военных объектах, такое название и получил — «военный» цемент, марка его «600».
В последнее время поставщики не довольны качеством цементных смесей, свойства их снизились, что привело в свою очередь к некачественным конструкциям, не способным выдерживать такие холода и воздействие влаги, какие они с легкостью выдерживали раньше. Это говорит о том, что отечественные заводы-изготовители не соблюдают ГОСТов, установленных на производство цемента, представители же Европы, наоборот, остались в этом отношении на том же уровне, а в чем-то даже улучшили качество! При этом цена его ненамного выше, чем цена на российский цемент. Примерами применения европейского цемента можно назвать туннели метро, всевозможные водопроводные и канализационные стоки, все те объекты, которые постоянно подвержены воздействию большой влажности и скачков температуры.
Немного отойдя от темы (но это знать тоже не помешает) хочется упомянуть еще и кислотоустойчивые цементы, которые, также как и быстротвердеющие, имеют очень высокую твердость, а также весьма устойчивы к воздействию агрессии кислотных сред. Отличие указанных разновидностей цемента следующее: этот вид твердеет гораздо дольше и при воздействии воды начинается процесс разрушения.
Как же работать с быстросохнущими растворами? Очень просто!!! Замешивается раствор из цемента, гранулированного песка и воды. Полученный состав нужно израсходовать в течение часа, поэтому раствор следует замешивать порциями. Наносится он только на подготовленную поверхность (то есть не замороженную, чистую и сухую, не должно быть жирных пятен, красок и старой штукатурки), слоями, каждый из которых выравнивается. Температура, при которой следует производить такие работы, рекомендована специалистами и составляет +10…+25 градусов. Также, нужно не допустить воздействия сквозняков и солнечного света, до отвердения через 3 суток.
Компания «ХимСервис» предлагает цемент марки ПЦ 500Д20 со склада в Пскове.
Быстротвердеющий бетон: состав, как производят
Используется быстротвердеющий бетон в строительстве многоэтажных зданий и монолитных бетонных сооружений для сокращения время ожидания между различными этапами строительства и увеличения качества постройки. Чтобы ускорить затвердевание, в раствор добавляют отвердители и специальные химические добавки. Такой метод имеет низкую себестоимость и широко доступен. Более редким и эффективным способом является измельчение цементного порошка и увеличение площади его контакта с водой.
Добавление строительного гипса ускоряет процесс затвердения в несколько раз, однако такая методика является устаревшей.
Что собой представляет?
Быстротвердеющий бетон отличается от обычного тем, что значительно быстрее набирает прочность и отвердевает согласно марке. Такой вид раствора обозначается буквой «Б». Он используется при строительстве монолитных сооружений, а также при кладке кирпича в многоэтажных зданиях. Особенность его заключается в предотвращении деформации нижних слоев под давлением верхних и отсутствии необходимости во временном прекращении работ. Быстросхватывающиеся бетонные растворы нашли свое применения в различных сферах строительства, особенно это касается возведения многоэтажных домов и других объектов со значительными объемами цементных работ.
Состав
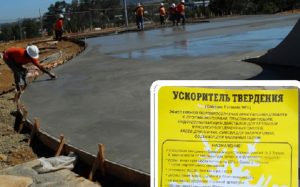
Бетон с быстрым твердением получают с помощью более тонкого измельчения цементного песка без изменения химического состава раствора. Для его изготовления понадобиться высококачественный цемент, щебень с высокой прочностью и промытый песок. Улучшить качество раствора поможет добавление суперпластификаторов, а также увеличение процентного соотношения цемента к основным компонентам бетона. Чтобы ускорить процесс затвердевания, применяют добавки-ускорители, такие как хлористый водород и кальций или глинозем. Иногда для получения необходимого эффекта используют 3% гипса, который добавляют в жидком или сыпучем виде. Алюминатный цемент подходит для изготовления быстротвердеющего раствора, который способен сжиматься в первые сутки 500 кг на сантиметр квадратный.
Плюсы и минусы
Существуют такие положительные моменты в использовании быстротвердеющего бетона:
- устраняются ограничения во времени при возведении кирпичных строений;
- при монолитном строении уменьшает вероятность трещин и расколов;
- отсутствуют перерывы между этапами строительных работ.
Быстротвердеющий бетон имеет такие недостатки:
- отсутствие широкодоступной информации о материале;
- большие материальные затраты на строительство;
- использование вредных добавок в виде отвердителей.
Маркировка
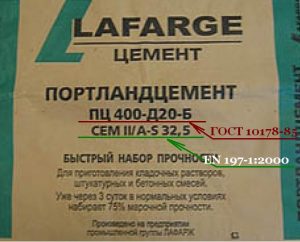
Цемент с быстротвердеющим эффектом имеет обозначение с индексом «Б», что указывает на эту особенность материала. Следующая цифра 500 или 400 показывает содержание в порошке добавок в виде отвердителей и загустителей. После этого ставиться процентное соотношение дополнительных веществ в нем. Международная маркировка имеет вид М400 и М500 без соответствующего индекса.
Быстросхватывающийся цемент целесообразно использовать при строительстве многоэтажных зданий.
Как производят?
Изготовление быстротвердеющего бетона без использования добавок происходит с помощью тонкого измельчения цемента. Это обусловлено тем, что меньшие гранулы соприкасаться со значительной площадью реагента. Такой процесс увеличивает прохождение дегидратации. Увеличение площади взаимодействия раствора приводит к застыванию в естественных условиях за короткий промежуток времени и снятия опалубки уже через 4 часа после заливки. Способ дорогостоящий, поэтому чаще применяется метод использования минеральных добавок и отвердителей. Полученый раствор затвердевает медленно, но применяется намного чаще, так как затраты на материалы меньшие.
Цемент водостойкий, водонепроницаемый, влагостойкий
Цемент водостойкий используется для строительства объектов, которые постоянно либо периодически находятся под воздействием воды и повышенного уровня влажности. Несмотря на то, что на рынке сегодня представлено множество строительных материалов с разнообразными свойствами, цемент по-прежнему остается одним из наиболее востребованных и актуальных. И необходимость сделать его водостойким может появиться в самых разных ситуациях.
Водонепроницаемый цемент в ряде случаев позволяет сэкономить деньги, время и силы на обеспечении сложных влагозащитных систем, сокращая объем гидроизоляционных мероприятий.
Объясняются такие свойства структурой материала: если при затвердении в обычном растворе остаются воздушные микроскопические полости, куда может попасть вода и разрушить материал, то в водостойком цементе их практически нет, поэтому монолит не боится воздействия влаги и воды.
В водонепроницаемом цементе нет воздушных включений благодаря расширению материала либо заполнению их специальными веществами. Обычно из влагостойкого цемента строят фундаменты на влажных почвах, разные конструкции при условии низкого пролегания грунтовых вод, погреба, подвалы, стяжки пола, смотровые ямы, стенки колодцев, бассейнов, резервуаров и т.д.
Виды водостойких цементов
Цемент влагостойкий бывает нескольких видов, которые отличаются по принципу взаимодействия веществ с составе, структуре, эксплуатационным характеристиками.
Всего существует три вида цемента, стойкого ко влаге: быстротвердеющий, безусадочный, расширяющийся. Все виды обладают нужным уровнем гидрофобности, но предполагают определенные особенности в работе и сфере использования.
Водонепроницаемый цемент демонстрирует меньшую пористость, не позволяя влаге попадать в структуру материала.
Не боится снега и влажного воздуха, не пропускает воду вовнутрь верхних слоев бетона, выдерживает воду под большим напором. Водостойкий цемент отталкивает воду – не пропускает вовнутрь, но напор воды не выдерживает.
Производство цемента с водостойкими качествами и его состав
В составе бетонной смеси с высокими показателями влагостойкости основным вяжущим веществом является цемент (производится из гипса, высококачественного глиноземистого цемента, гидроилюмината кальция. В частном строительстве редко делят цемент данного типа на водонепроницаемый и влагостойкий, но при возведении серьезных масштабных проектов состав и особенности материала нужно изучать тщательно.
В производстве водонепроницаемой бетонной смеси используют цемент тонкого помола (обычно портландцемент М500) со специальными добавками, вид и объем которых может быть разным. Мелким наполнителем выступает песок, крупным – щебень или гравий.
Связующее и наполнитель используют в пропорциях от 1:3.6 (М450) до 1:11.6 (М100). Песок с щебнем берут в объемах 1:1.5 (не очень прочные составы) и 1:2.2 (высокопрочные бетоны).
При покупке нужно обращать внимание на маркировку: М500 – это марка прочности цемента, а Д20 – это процент добавок (то есть, в общем объеме 20% добавок). Есть смеси, в которых добавок нет, маркировка может выглядеть вот так «Цемент Русеан М500 Д0».
Область применения
Водонепроницаемый цемент используется обычно в условиях повышенной влажности, риска разрушения бетона водой, там, где мероприятия по гидроизоляции не могут быть проведены или обойдутся слишком дорого.
Сфера применения водостойкого цемента:
- Условия повышенной влажности от 75% и выше – в сухих условиях после использования раствора с такими свойствами он даст сильную усадку
- Строительство фундаментов, цоколей, несущих конструкций
- Сооружение колодцев, различных конструкций на большой глубине
- Цемент водонепроницаемый расширяющийся активно используют при восстановлении разрушенных железобетонных и бетонных объектов
- Гидроизоляция стволов шахт, тоннелей
- Подземное и подводное строительство, обустройство водонепроницаемых швов
- Устройство изоляционных оболочек в разнообразных конструкциях железобетонных сооружений
- Цемент для бассейнов водонепроницаемый применяют при укладке плитки на дне чаши
- Устройство стяжки пола в подвале, погребе, гараже
- Заливка дна и стен септиков
- Сооружение водоводов, декоративных прудов
- Создание водонепроницаемой стяжки на крыше подземных гаражей
Применение материала актуально везде, где есть необходимость повысить стойкость бетонной конструкции ко влаге и защитить от разрушений.
Безусадочный
Безусадочный водонепроницаемый цемент создают с использованием алюмината в небольшом объеме. Создается кристаллический цементный камень, упрочняющий и уплотняющий структуру. Состав смеси: глиноземистые портландцементы (около 85% объема), асбест (до 5%), полуводный гипс и алюминат кальция (до 10%).
Уже через час после твердения железобетонных конструкций бетон набирает 75% прочности, полный цикл проходит за обычные 28 суток. Масса должна застывать во влажной среде (минимум 70% влажности), в противном случае процесса усадки не избежать.
Материал используется для возведения сооружений, которые постоянно находятся под воздействием воды. Поэтому в раствор часто добавляют смесь азотнокислого кальция, алюминиевой пудры и ферросилиция для антикоррозийного эффекта и защиты армирования от влаги.
Расширяющийся
ВРЦ расширяющегося типа изготавливают посредством добавления в состав гидроалюмината. Чаще всего состав такой: 70% глиноземистого цемента, 20% полуводного гипса, 10% гидроалюмината кальция. Смесь готовят так: смешивают сухие компоненты, измельчают. Благодаря активной реакции между компонентами масса расширяется в процессе быстрого твердения, схватывается уже через несколько минут после укладки, завершается процесс через 10 минут.
Влагостойкий расширяющийся цемент расширяется тем больше, чем выше влажность. Процесс внутреннего расширения проходит долго. Через 3 дня цемент соответствует прочности марки М300, через 28 – марки М500. Раствор обладает высокими гидроизоляционными свойствами, улучшающимися в воде. Данная характеристика позволяет использовать бетон в строительстве бассейнов, плотин, дамб.
Быстротвердеющий
Цемент водонепроницаемый быстротвердеющий застывает быстрее всех остальных. Его состав способствует повышению прочности уже на третьи сутки после заливки. В состав вводят трехкальциевый силикат в объеме, равном минимум 50% общей массы раствора.
Быстротвердеющий водостойкий цемент используется в создании сверхпрочных бетонов, для ускорения времени кладки, в производстве не боящихся влаги железобетонных конструкций, для создания тротуарной плитки и бордюров.
Цемент быстротвердеющий более дорогой, чем обычный, работать с ним можно лишь при наличии определенного опыта, так как смесь быстро твердеет и потом становится непригодной для использования. По внешнему виду цемент ничем не отличается от обыкновенного, хранить нужно вдали от воды (хоть влаги смесь и не боится).
Как сделать цемент водонепроницаемым своими руками
До того, как сделать раствор водонепроницаемым своими руками, нужно тщательно изучить все пропорции. Так, в обычный цемент можно добавить жидкий гидроизолирующий гиперконцентрат Дегидрол 10-2 в объеме 4 литра на кубический метр раствора. Рецепт гидроизоляционной бетонной смеси: 125 кг цемента, 30 кг песка, 55 кг щебня, 200 миллилитров Дегидрола, 10 литров воды.
Сначала разводят водой добавку, потом смешивают сухие компоненты, в них доливают жидкость. В процессе приготовления нужно исключить возможность попадания в раствор песка с содержанием глины или самой глины. Если используется бетономешалка, то сначала в нее вливают воду, потом Дегидрол, далее постепенно всыпают сухие субстанции. Смесь готова через 5 минут после замеса.
Важно не только соблюдать пропорцию сухих материалов и правильно выбирать добавки: изготовление бетона предполагает еще некоторые нюансы. Так, нужно удостовериться, чтобы объем воды не превышал 40% общего объема раствора. То есть, для мешка цемента в 50 килограммов берут воды не больше 20 литров. Нужно следить за тем, чтобы в составе песка не было глины. На один кубический метр смеси берут минимум 350 килограммов цемента.
Виды добавок
Можно произвести водостойкий цементный раствор своими руками, зная, какие добавки нужны и в каких объемах их нужно добавлять. В составе бетонной смеси, стойкой к воде, могут быть такие добавки: Дегидрол, Працтин, Церезин Нормал, Бетфикс, Трицосал Н. Эти добавки призваны повышать прочность материала, плотность, уменьшать число пор в структуре, в которые может попадать вода.
Пластификаторы могут добавляться в объеме 0.1-3% общей массы. Это преимущественно ПАВы, которые могут быть высокоэффективными, сильнопластифицирующими и слабопластифицирующими.
Для придания водонепроницаемости уже затвердевшему материалу в состав вводят неорганические соли металлов (нитрат кальция, силикат калия и натрия, хлорное железо и т.д.). Щелочные соли и силиконовые жидкости применяются в качестве гидрофобных добавок.
Вибрирование
Вибрирование позволяет удалить воздух, который мог появиться в структуре материала и значительно уплотнить бетон. Лучше всего данный этап работ выполнять с использованием специального оборудования – обычно для этих целей берут наружные глубинные вибраторы планетарного, маятникового, электромеханического типов.
Уход за бетонными конструкциями
На протяжении трех суток после заливки бетона его поверхность регулярно сбрызгивают водой – с интервалом несколько часов. Также обязательно укутывают полиэтиленовой пленкой, которая защищает бетон от быстрого испарения влаги. Такой специальный уход позволит уменьшить усадку и защитить будущую конструкцию от появления трещин, деформаций, разрушений.
Водостойкий цемент – материал, использование которого актуально в самых разных сферах, на тех или иных этапах ремонтно-строительных работ. Создать водонепроницаемую бетонную смесь можно своими руками, при условии соблюдения пропорции и выбора правильных добавок.
Твердение (время схватывания) бетона в зависимости от температуры
Заливка бетона в холодное и жаркое время года требует особых навыков и знаний, т.к. работы с цементной смесью осложняются, а период ее высыхания резко уменьшается или возрастает. Изменение скорости твердения бетона в зависимости от температуры обусловлено замедлением процессов гидратации и удержанием большого количества жидкости в толще материала.
Для ускорения застывания и предупреждения дефектов используются специальные строительные приемы, полимерные и противоморозные добавки.


Стадии набора прочности бетонной конструкцией
Схватывание и твердение растворов на основе цемента обусловлено его химическим взаимодействием с водой. Силикаты, алюминаты и алюмоферриты, которые входят в состав портландцемента, обеспечивают повышение прочности на различных стадиях отверждения.
Скорость химических реакций зависит от наличия катализаторов (специальных добавок) и температуры.
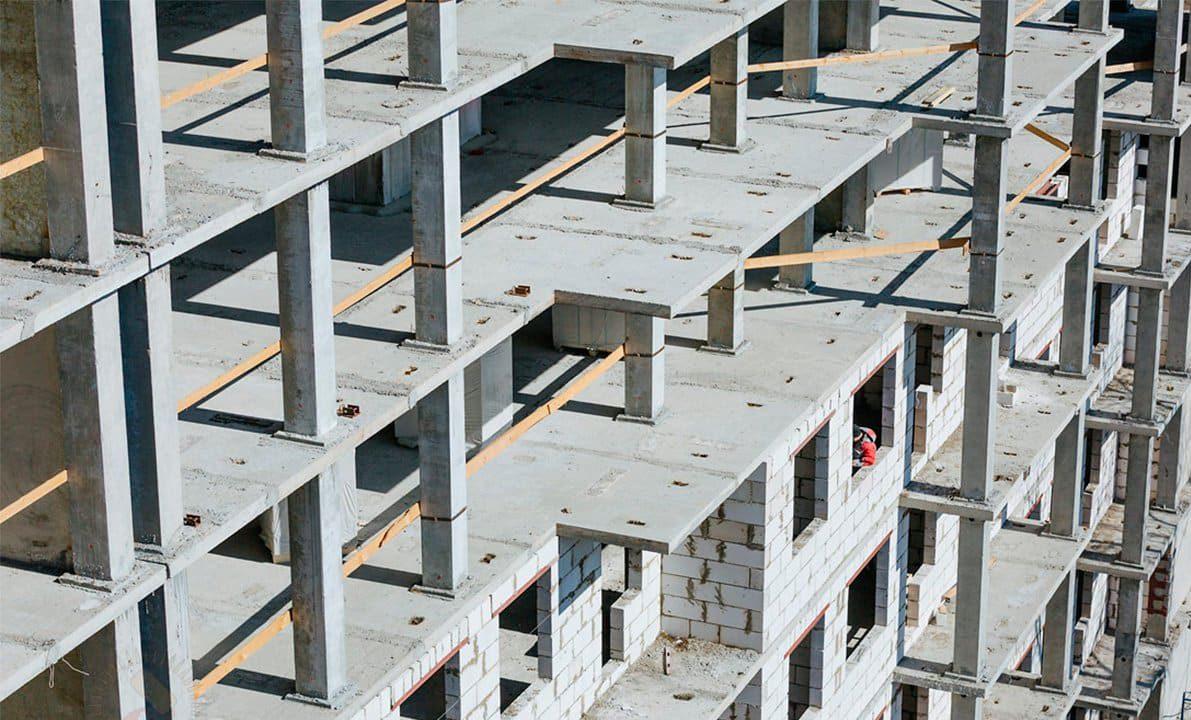
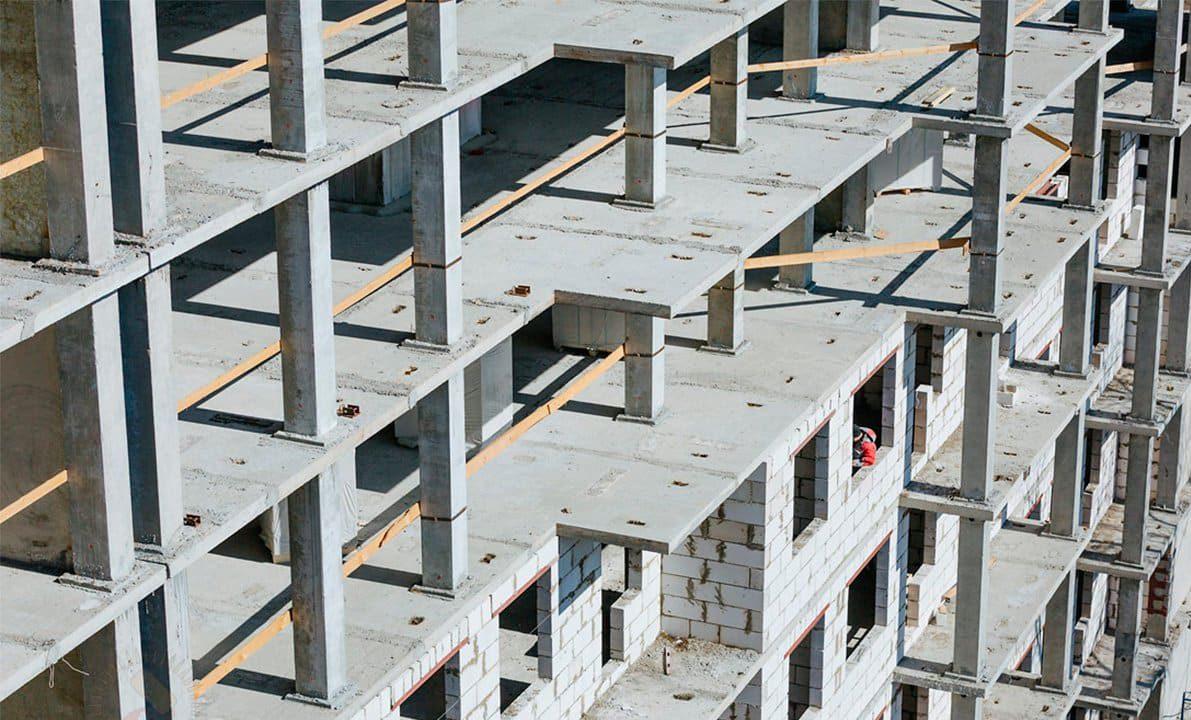
Бетонные конструкции бывают разные, исходя из этого следует рассчитывать соотношение компонентов раствора и предполагать сроки схватывания и твердения.
Стадия схватывания
В состав цементного порошка входит трехкальциевый алюминат (3СаО*Al2O3), трехкальциевый силикат (алит, 3СаО*SiO2), двухкальциевый силикат (белит, 2CaO*SiO2) и алюмоферрит. Алит, который занимает большую часть массы портландцемента, участвует в обеих стадиях отверждения. При затворении водой и в начале стадии схватывания он выделяет тепло, которое увеличивает скорость реакции.
Однако более активным компонентом цемента на этапе схватывания является трехкальциевый алюминат. В течение 24 часов после смешивания он интенсивно реагирует с водой, формируя первичные связи в бетоне. После окончания схватывания алюминат полностью утрачивает влияние на прочность цемента.


Итоговая прочность бетона в зависимости от марки, времени затвердевания и температуры воздуха.
Стадия схватывания проходит в первые часы после заливки опалубки. Скорость начала реакции и длительность процесса зависят от состава смеси и температуры воздуха. При нормальных температурах (+18…+22°С) бетон схватывается через 2,5-3 часа. Из них 1,5-2 часа проходит до начала реакции, а 1 час уходит непосредственно на схватывание.
При снижении температуры начало реакции может отодвинуться на 4-8 часов, а ее продолжительность — увеличиться до 15-20 часов.
В горячей среде схватывание происходит активнее и начинается более быстро. Весь процесс может занять менее 1-2 часов, из которых реакция — 15-20 минут.
Стадия твердения
Стадия формирования бетонного камня начинается по завершении схватывания. Твердение материала происходит за счет удаления свободной воды. Часть жидкости испаряется во внешнюю среду, а другая — связывается с молекулами силикатов и алюминатов, образуя стойкие комплексы. Чтобы не нарушить баланса между связываемой и испаряющейся водой, нужно обеспечить оптимальную влажность и температуру среды.
Основным реагентом на стадии твердения является алит. Белит обеспечивает постепенное упрочнение материала в процессе эксплуатации: за счет его свойств прочность материала через 2-3 года может составлять до 250% прочности после твердения.
Стандартный срок затвердевания бетона
Стандартное время застывания бетона составляет 28-30 дней. Нормальные условия для отверждения — температура +15…+22°С и влажность 60-100%. Длительность отверждения зависит от условий процесса, марки бетона и наличия дополнительных добавок в растворе.


Корреляция прочности бетона с временем выдерживания и температурой среды.
Зависимость времени набора прочности от марки бетонной смеси
Повышение прочности бетона на сжатие коррелирует с увеличением вязкости смеси. Это означает, что с увеличением марки материала время схватывания и твердения сокращается.
Продолжительность реакций для бетона разных марок
Марка материала | Время схватывания, часов | Время твердения, суток |
М100 | 3-3,5 | До 30 |
М200 | 2-2,5 | 14-25 |
М300 | 1,5-2 | 7-14 |
М400 | 1-2 | 4-7 |
М500 | <1 | 2-4 |
Продолжительность набора прочности зависит от состава смеси, влажности, температуры внешней среды и материала.
Марка и назначение раствора определяют и критическую прочность бетонного камня. Это значение, по достижении которого конструкция продолжит твердеть после замерзания без потери эксплуатационных свойств. Данный показатель зависит от марки следующим образом:
- для бетона М100 и М150 он соответствует 50%;
- для М200, М250, М300 и М350 — 40%;
- для М400, М450 и М500 — 30%;
- для нагруженных конструкций (вне зависимости от марки) — 70%.
Если в момент замерзания образец имеет соответствующий уровень прочности на сжатие, то температурные перепады незначительно повлияют на его прочность. При замерзании на ранних стадиях твердения без применения противоморозных добавок прочность готовой конструкции падает не менее чем на 50%. Например, для марки М200 критической точкой прочности является 80 кгс/см² или 8 МПа.
Наиболее часто для фундаментов и нагруженных конструкций используются марки бетона от М300. Снятие опалубки со стандартных конструкций допускается через 4-5 дней при наличии щелей между щитами формы и бетоном. Для перекрытий и лестниц длиной не более 6 м время выдержки продлевается до 14 дней, для длинных лестниц — до 28 дней. Мосты, дамбы и другие ответственные и тяжело нагруженные конструкции выдерживаются в форме до 90 дней.
Специальные добавки
Стремительное или слишком медленное схватывание и твердение смеси снижает прочность бетона. Медленное застывание дополнительно увеличивает расходы на уход за конструкцией. Для коррекции скорости отверждения применяются добавки, которые регулируют кинетику процесса.Существует два типа добавок, регулирующих процесс твердения раствора:
- Ускоряющие. Реагенты этого типа сокращают время до начала схватывания на 30-40%, ускоряют затвердевание и улучшают прочностные свойства материала. Они добавляются в смесь при промышленной штамповке бетонных изделий, заливке фундаментов, перекрытий и иных строительных конструкций при пониженных температурах. Наиболее дешевые ускоряющие добавки — это хлористый кальций и поташ (углекислый калий). В перечень востребованных строительных составов для ускорения отверждения входят: Релаксор, Аддимент В3, Форт-УП2, Поззолит-100, Конкрит-Ф и др.
- Замедляющие. Пластификаторы и замедлители схватывания положительно влияют на удобоукладываемость и подвижность раствора. Они применяются при доставке бетона в передвижных смесителях, задержках в строительстве и заливке конструкций при температуре выше +25…+30°С. Пластифицирующие свойства замедлителей позволяют отказаться от виброуплотнения при укладке бетона с малой подвижностью. Наиболее распространенными замедляющими добавками являются НТФ-кислота, цитрат и глюконат натрия, Линамикс, SikaPlast 520 N, Frem Linas 200 и др.
При заливке в условиях низких температур используются противоморозные реагенты. Они понижают температуру замерзания воды, препятствуя ее фазовым переходам при 0…+4°С.
В зависимости от вида и концентрации добавок они позволяют работать с бетонным раствором при температуре до -15…-25°С. К морозоустойчивым реагентам относятся нитрит натрия, нитрат-нитрит кальция, карбамид и др.
Набор прочности бетона в зависимости от температуры
Температура окружающей среды определяет скорость реакций, которые формируют бетонный камень. Повышенная температура воздуха смещает баланс в сторону испарения жидкости, а пониженная — тормозит процессы гидратации в растворе.
При высоких температурах
В сухом и горячем воздухе испарение воды происходит быстрее, а оставшейся жидкости может не хватить для полноценной гидратации. В результате снижается надежность конструкции, а ее прочность на сжатие в верхних и центральных слоях существенно различается.
Для профилактики неравномерности и быстрого высыхания в бетон добавляются замедляющие добавки, а готовая конструкция смачивается в процессе застывания.
Высокая температура и влажность применяются при производстве стандартных бетонных изделий в автоклавах. Такие условия обеспечивают быстрое схватывание и максимальное твердение конструкций.
В прохладное время
При низких температурах раствор долго схватывается, а затем в течение длительного времени остается хрупким по сравнению с марочной прочностью. Химические реакции происходят до температуры фазовых превращений воды.
При отрицательной температуре
Когда температура среды опускается ниже 0°С, вода замерзает, а гидратация в растворе — прекращается. При прогреве воздуха процесс отверждения возобновляется, но прочность конструкции после перерыва может снизиться.
Набор прочности бетона при различных температурах
Срок застывания, суток | Доля от 28-суточной прочности, достигнутой при оптимальных условиях твердения | |||||
При -3°С | При 0°С | При +5°С | При +10°С | При +20°С | При +30°С | |
1 | 3 | 5 | 9 | 12 | 23 | 35 |
2 | 6 | 12 | 19 | 25 | 40 | 55 |
3 | 8 | 18 | 27 | 37 | 50 | 65 |
5 | 12 | 28 | 38 | 50 | 65 | 80 |
7 | 15 | 35 | 48 | 58 | 75 | 90 |
14 | 20 | 50 | 62 | 72 | 90 | 100 |
28 | 25 | 65 | 77 | 85 | 100 |
В таблице рассмотрен набор прочности материала марок М200 и М300.
Снижение вязкости раствора
Во время схватывания бетонный раствор сохраняет свою пластичность. При движении в стационарной или подвижной бетономешалке смесь проявляет свойство тиксотропии — уменьшения вязкости состава при постоянной динамической нагрузке.


Характеристики действия пластификаторов на примере одного из наиболее популярных.
Слишком длительное перемешивание приводит к «перевариванию» бетона и снижению конструктивной прочности готовой конструкции. Чтобы сохранить подвижность раствора и избежать негативных эффектов, в смесь добавляются пластификаторы. Они удлиняют периоды схватывания и застывания.
Снизить вязкость смеси на стадии затвердевания нельзя. Механическое воздействие на застывающий бетонный камень приводит к формированию дефектов и растрескиванию конструкции. До достижения минимально допустимого уровня прочности застывающий бетон следует предохранять от ударов, вибрации и др.
Зависимость уровня набора прочности от показателей температуры материала
Низкая температура ингредиентов отрицательно влияет на эксплуатационные характеристики бетонного камня. Если для смешивания используется холодная вода и наполнитель, то последующий уход за конструкцией не сможет обеспечить марочную прочность.


Учитывайте, как может измениться температура окружающей среды пока бетон будет затвердевать.
При температуре менее 10°С рекомендуется подогревать воду, которая применяется для изготовления. Если показатель термометра соответствует -5…0°С или ниже, то необходимо подогревать и мелкий наполнитель (речной песок).
Для сокращения времени схватывания и расходов на подогрев бетона в опалубке компоненты разогреваются до предельно допустимого уровня. Максимальное значение определяется составом и маркой портландцемента. При нагреве выше этой температуры готовая смесь будет реагировать менее интенсивно, что скажется на прочности конструкции.
Предельная температура компонентов бетонного раствора
Вид цемента | Максимальная температура воды для затворения, °С | Предельная температура наполнителя, °С | Максимальная температура бетонного раствора после вымешивания, °С |
Глиноземистый | 40 | 20 | 25 |
Портландцемент марки М400 и выше Пуццолановый цемент марки М300 и выше | 60 | 40 | 35 |
Портландцемент марок М300 и М350 Цемент с пуццоланой М200 | 80 | 50 | 40 |
Шлакопортландцемент М200 и М300 | 90 | 60 | 45 |
Рекомендации по ускорению процесса
Соблюсти необходимые условия для заливки не всегда возможно: в жаркую и холодную погоду температура отклоняется от оптимальной не менее чем на 15-20°С, а влажность может составлять ниже 60%.
Чтобы избежать пагубного влияния низкой влажности, высоких и низких температур, бетонщики прибегают к специальным методам ухода. К ним относится обработка горячим влажным паром, применение теплых опалубок, закладка электродов и греющих проводов в тело бетонного изделия и др.
При заливке фундамента строители прибегают к мерам защиты бетона на этапе смешивания, но редко дополнительно подогревают готовую конструкцию. Это обусловлено тем, что основа здания должна пройти этапы усадки и стабилизации грунта. В этом случае возникшие дефекты не скажутся на прочности дома, а будут устранены с помощью дополнительного слоя бетона.
Бетон м500: характеристики
Бетон М500 – прочный и надежный материал, который не боится воздействия различных негативных факторов, агрессивных сред, выдерживает максимальные нагрузки и служит долго. В частном строительстве бетон используется редко ввиду того, что его характеристики часто превосходят нормативные и мастера просто не видят смысла в больших расходах.
Стоимость кубометра и точные показатели бетона зависят от того, какие материалы используются в приготовлении раствора, есть ли присадки для увеличения стойкости к воздействию влаги, мороза и каков их объем в смеси. Любой тяжелый бетон 500 демонстрирует великолепные характеристики прочности на сжатие, что актуально во многих сферах строительства.
Технические характеристики
Марка бетона 500 предполагает определенные свойства и показатели, которым должен соответствовать материал. Многие параметры существенно превосходят более популярные в ремонтно-строительных работах марки цемента М200 (бетон не самый прочный), М300 (бетон со средними характеристиками), М400.


Основные свойства бетона М500:
- Прочность – класс В40, 51.73 МПа (раствор выдерживает нагрузку в 523.7 килограмма на см2)
- Стойкость к перепадам температуры – F200-F500
- Подвижность (бетона на граните) – П2-П5
- Водонепроницаемость – W10-W16 (допускается строительство эксплуатируемых в воде конструкций)
- Нормативная плотность бетона М500 – 2298 кг/м3
- Вес кубического метра – 2298 килограммов
- Срок застывания – 1-2 часа
Преимущества и недостатки
В отличие от марок М200, М300 и других, бетон М500 демонстрирует очень высокие показатели прочности, долговечности, стойкости к разным средам и воздействиям. Но и стоимость материала высока, поэтому до применения его в строительстве необходимо тщательно изучить все свойства и определить целесообразность приготовления раствора.
Основные достоинства бетона М500:
- Высокая прочность на сжатие, разнотипное механическое воздействие – повредить материал можно лишь специальным инструментом с алмазным напылением
- Высокая скорость затвердевания – это не быстросохнущий цемент, конечно же, но все равно схватывается смесь оперативно, даже в условиях повышенного уровня влажности
- Прекрасные показатели стойкости ко влаге – из-за того, что в составе применяется мелкий песок, не дающий шанса воде поступать в поры монолита: благодаря этому конструкции можно эксплуатировать даже под водой
- Состав бетона М500 гарантирует ему неподверженность воздействию сильных ветров, ультрафиолета, атмосферных осадков и т.д.
- Длительный период службы – конструкции и объекты, созданные из материала, вообще не подвержены самостоятельным деформациям
Из недостатков стоит отметить, в первую очередь, то, что бетон марки М500 очень дорого стоит и его повышенные характеристики не актуальны в быту, так как остаются невостребованными. Да и приготовление раствора потребует немалых затрат, усилий. В Москве и области, других регионах можно приобрести сухую смесь (щебня в ней только нет), но для замеса потребуется специальное оборудование.
Где применяют бетон этой марки
Как указывалось, бетон М 500 практически не применяется в индивидуальном строительстве, так как там нет необходимости обеспечивать столь высокие параметры материалом, существенно повышающим расходы на строительство.
Сфера применения бетона М500:
- Сооружение фундамента для многоэтажных домов (небоскребов) с большой массой на минимальной площади
- Монтаж опор мостов, разнообразных гидротехнических сооружений и сложных конструкций
- Проектирование и монтаж подземных сооружений, которые испытывают воздействие грунтовых вод, нагрузки почвы – стены и опоры метро, к примеру
- Оборонительные сооружение – благодаря тому, что бетон М500 характеристики теплопроводности, прочности, плотности предполагает наилучшие, конструкции из него защищают от температуры, осколков, мощной взрывной волны, даже от радиоактивного излучения и т.д.
- Гидротехнические сооружения – пристани, молы, волнорезы, гидроэлектростанции
- Создание автострад, опор для мостов
- Монтаж объектов специального (особого) назначения – бункеры и иные, для возведения которых применяют даже бетон 500 марки со свинцовой стружкой в составе
Состав бетона
Чтобы определить оптимальные пропорции бетона М500, сначала нужно рассмотреть его состав. В раствор входят определенные ингредиенты, от качества и правильности выбора которых зависит качество смеси. Параметры готового раствора регулирует ГОСТ 7473-2010.
Что входит в смесь:
- Качественный гранитный щебень фракции 3-5 сантиметров – камни должны быть одинаковыми, чтобы нагрузку материал принимал равномерно
- Мелкий песок – тщательно очищенный и промытый, за счет него понижается число пустотных участков, повышается плотность
- Цемент марки М500 – на данном ингредиенте экономить точно нельзя, так как именно он отвечает за прочность, которую обеспечит бетон марки 500 (пропорции тоже должны соблюдаться максимально точно)
- Вода чистая – после специальной фильтрации для исключения риска попадания в раствор примесей органики и солей, которые могут препятствовать нормативному схватыванию
Как приготовить бетон 500-й марки самому
Чтобы приготовить качественный раствор, необходимо точно знать соотношения. Пропорции бетона М500 могут зависеть от типа и качества материала и меняться соответственно. Но все равно лучше придерживаться стандартов, чтобы вместо нужной смеси не получить смесь марки М350 (бетон со средними показателями) или М450. Ведь при сооружении конструкций, которые будут выдерживать огромные нагрузки и сложные условия эксплуатации, даже небольшое отклонение от нормативных показателей может быть губительным.
Пропорции бетона М500 (1:1.1:2.2:0.5):
- Цемент – 10 килограммов
- Речной песок – 11 килограммов
- Щебень – 22 килограмма
- Вода – 5 литров
Такое соотношение считается наиболее оптимальным для приготовления бетона М500. Сделать такой бетон дома практически невозможно – так, если М400 (бетон тоже с достаточно высокими характеристиками) еще можно приготовить в быту, то М500 лучше заказывать на заводе. При заказе сухой смеси также нужно тщательно выбирать поставщика, убедившись в наличии у него необходимого для производства материала оборудования и всех сертификатов качества.
В противном случае можно купить смесь, которая по нормативным параметрам будет соответствовать гораздо более низким маркам и в определенных условиях приведет к деформации конструкции, продемонстрирует класс В22-25 прочности вместо В40, спровоцирует другие проблемы, что просто недопустимо.
Бетон М500 – прочный и долговечный материал, который стоит довольно дорого. Поэтому используют его обычно там, где есть необходимость в повышенных параметрах и улучшенных свойствах, что полностью оправдывает высокую цену.
Ускорители твердения (схватывания) бетона: что это, какой лучше
Для того чтобы разобраться с процессом твердения бетона, надо вспомнить, почему и как происходит этот процесс.
Современная бетонная смесь состоит из следующих компонентов:
- цемент;
- песок;
- щебень;
- добавки;
- вода.
Процесс твердения обеспечивает цемент с водой. А чтобы понять, что такое цемент, подробно остановимся на этом компоненте.
Цемент получается после помола клинкерных смесей, которые производят в огромных печах обжига при температуре порядка 1450 ℃. Основным сырьём для клинкера являются известняковые горные породы и глина. После такой высокой температурной обработки происходят структурные изменения и полученный спёкшийся клинкер смешивают с гипсом и другими веществами. Эту смесь загружают в шаровые мельницы и измельчают до мелкодисперсной сыпучей массы серого цвета, которая и называется цементом. Он состоит из 4 основных минералов:
- 2Cа∙SiO2 – двухкальциевый силикат;
- 3Ca∙SiO2 –трёхкальциевый силикат;
- 3CaO∙Al2O3 – трёхкальциевый алюминат;
- 4CaO∙Al2O3∙Fe2O3 – четырёхкальциевый алюмоферрит.
Все эти составляющие цемента играют важнейшее значение в его дальнейшем поведении. Всё самое главное начинается тогда, когда он вступает во взаимодействие с водой. Начинается твердение цемента или ещё этот процесс называют гидратацией, когда молекулы воды связываются через физико-химический процесс со всем многообразием минералов цемента.
В этой фазе все четыре компонента ведут себя по-разному. Одни минералы вступают в реакцию сразу, другие через время, третьи запускают своё действие лишь в финале процесса затвердения, завершая долгодневный процесс.
Полный цикл твердения цемента длится годами, но основным считается отрезок в 28 суток.
Важнейшим фактором гидратации цемента считается водоцементное соотношение (В/Ц).
Оно определяет все прочностные характеристики полученного цементного камня. На этой картинке удачно обозначена схема взаимодействия молекул воды и цементных зёрен.
Из неё видно, что оптимальным В/Ц будет 0.4. Но при приготовлении уже бетонной смеси там добавляются инертные заполнители, такие как песок и щебень. Если готовится раствор, то тогда добавляется только песок. Цемент является единственным вяжущим, который скрепляет в одно целое все компоненты бетонной смеси. Частицы цемента уже кристаллизовались и заполнили пространство между частицами инертных материалов, начался процесс схватывания.
Этот процесс начинается в зависимости от температуры и других факторов через 20 минут и продолжается до 20 часов. Но после схватывания наступает непосредственно процесс твердения, который и даёт основную прочность бетону. Он длится до 28 суток, когда набрана основная прочность в 95 %.
Так подробно надо было остановиться на этих процессах для того, чтоб было понятно, как можно влиять на них.
Необходимость ускорения процессов схватывания и твердения
Строительные процессы каждый раз ставят различные сложные задачи перед исполнителями. Например, низкая температура, которая отрицательно сказывается на сроках твердения – они удлиняются.
Бывают ситуации, когда необходимо разобрать опалубку раньше, чем бетон затвердеет и наберёт необходимую прочность, позволяющую передвигаться по поверхности строителям. Но возможны и ситуации, когда необходимо оттянуть сроки начала схватывания цемента, потому что бетонный узел находится далеко от объекта.
Во всех этих случаях необходимо применение регуляторов сроков схватывания цемента. Это требуется для того, чтобы сроки начала схватывания не опережали сроки укладки бетонной смеси. Эти процессы надо разводить по сторонам. Механизм такой – сначала укладка, потом начало сроков схватывания.
Химия процесса
Необходимо различать несколько способов ускорения твердения бетонных и растворных смесей:
Тепловая обработка
Голландский химик Вант – Гофф вывел правило, которое гласит, что при увеличении температуры на 10℃ происходит ускорение химической реакции в 2 – 4 раза. Такое происходит в температурном диапазоне от 0 до 100℃. Если бетон набирает свою марочную прочность при температуре 20 ℃ за 28 суток, то исходя из формулы голландца необходимая прочность у бетона наступит при температуре 60 ℃ через 8 часов. Поэтому на заводах весь процесс укладываю в 12 часов (3 часа подъём температуры, 6 часов изотермическая выдержка и 3 часа – остывание). За это время изделие набирает прочность от 90 до 105%.
Добавки в бетоны и растворы
Это всевозможные соли неорганических кислот — хлориды, сульфаты ( CaCl2, NaNO3, KNO3, KCl и т.д.). Механизм состоит в том, что это соли электролиты и они повышают растворимость цементных минералов и реакция гидратации протекает быстрее. Требования к добавкам ускорения по ГОСТ 24211 – 2008 состоят в том, что они должны обеспечивать в первые сутки твердения бетона прирост прочности не менее 30 %. Надо также отметить, что эти добавки в большинстве своём известны как противоморозные.
Снижение водоцементного соотношения (В/Ц)
Чем меньше воды, тем быстрее вода с цементом переходят в насыщенное состояние и активизируется рост кристаллизации цементного камня. Ну а если воды больше, то насыщение раствора и рост кристаллизации будет проходить в удлинённые сроки. То есть можно сказать так – бетон с низким В/Ц быстрее приобретёт распалубочную прочность, нежели с высоким.
А это очень важно в условиях ускорения строительных сроков.
Для регуляции В/Ц применяются пластификаторы, которые и позволяют снижать содержание воды в бетонной смеси.
Использование микрокремнезёма SiO2
Это побочный продукт некоторых металлургических производств, которые работают с кремнесодержащими металлами, сплавами и в виде золы уноса собираются и добавляют в бетонные смеси. Химия этого процесса ускорения заключается в следующем: вода вступает во взаимодействие с цементом и образуется портландит (Ca(OH)2) плюс ещё много чего. Но при добавлении микрокремнезёма он вступает в реакцию с портландитом и связывает его, и реакция образования портландита ускоряется по законам химии. При добавлении кремнезёма прирост прочности бетона в первые двое суток составляет от 50 до 80%.
Использование быстротвердеющих цементов
Это такой е портландцемент, но с большей удельной поверхностью. Поэтому некоторые железобетонные заводы докупают к своим технологическим процессам шаровые мельницы и подвергают обычные, низкомарочные цементы дополнительному помолу. На выходе получается цемент, который быстро твердеет и решает задачу ускорения производства ж/б изделий. Есть цементы, которые за счёт быстропротекающей реакции набирают прочность стремительно. Например, глинозёмистый, который может набирать 100 % прочность за 3 суток.
Но у них есть недостаток – они дороги.
Обзор российских и иностранных регуляторов сроков схватывания и твердения цемента
Универсал П-2
Является пластифицирующей добавкой, которая позволяет снизить расход воды на 12 %. Набор роста прочности в первые сутки не менее 50%. Увеличивает морозостойкость на 1-2 марки. Повышает водонепроницаемость на 2 позиции. Не содержит веществ, провоцирующих коррозию арматуры. Применяется для всех видов бетонов, включая преднапряжённые и особо ответственные конструкции.
Форт УП-2
Комплексная добавка для бетонных смесей и цементно-песчаных растворов. Добавляет составам рост сроков схватывания и твердения. Прирост прочности в течение первых суток твердения более 30 %. Позволяет полностью отказаться от тепло-влажностной обработки при температуре ≥15℃. Повышает конечную прочность бетона на 10 %, что позволяет экономить до 12 % цемента. Улучшает удобоукладываемость и сохранность бетонной смеси.
Асилин 12
Жидкий ускоритель для работы с бетонами и растворами при пониженных и повышенных температурах. Применяется при производстве пенобетона, снижает усадку при протекании реакции вспучивания. Прирост прочности по отношению к регламентной – 30 %. Безвреден при работе с ним, не горит. Содержание по отношению к массе цемента – 0.4-1% для пенобетонов, 0.5-2 % для тяжёлых.
Хлористый кальций
Добавка, позволяющая в дополнение к ускорению твердения ещё повысить износостойкость и устойчивость к атмосферным осадкам. Применение хлористого кальция даёт прирост прочности во время твердения в 2-3 раза. Эта добавка набирает влагу из воздуха и пускает её на гидратацию цемента. Такой эффект важен при высоких атмосферных температурах.
Но требуется осторожность при изготовлении армированных бетонов, в больших количествах может отрицательно сказаться на коррозии арматуры.
Релаксол
Выполняет две функции – как ускоритель и противоморозная добавка. Ускоряет твердение на 40 % в первые трое суток. Дозировка – 0.5-2 % от массы цемента.
Реламикс
Целая линейка суперпластификаторов ускорителей твердения. Снижает расходы на пропарку изделий, а в отдельных случаях и вовсе позволяет отказаться от неё. Дозировка – 0.6-1 %.
CemStone
В строительстве бывают ситуации, когда требуется продлить сроки начала схватывания и твердения вяжущего. Это позволяет сохранить смесь в рабочем состоянии на несколько часов. Таковой является эта пластифицирующая добавка. Её действие основано на замедлении начала химического процесса гидратации цемента, т. е. с запаздыванием кристаллизации. Такая добавка наоборот снижает набор прочности в первые 7 суток на 30 %. Но к 28 суткам набирает необходимые 100 %.
Видео
Для рукастых домохозяев вот видео:
Коротко о главном
- Для быстрого затвердения свежеуложенной поверхности применяют так называемые упрочнители (топпинги), которые содержат особые виды цемента и устойчивые к механическим воздействиям наполнители. Такой состав наносят на поверхность и образуется прочная корка.
- Газообразователи. Применяют при производстве газобетона. Основной воздухообразователь алюминиевая пудра. Снижается удельный вес бетона, но и прочностные характеристики.
- Есть вещества, которые служат ускорению схватывания, такие свойства необходимы растворным смесям при проведении ремонтных работ, когда требуется быстро заделать отверстие в бетонных плоскостях.
- При применении добавок, замедляющих процессы затвердевания, необходимо строго соблюдать дозировку, иначе при излишнем количестве возможна потеря прочности.
Осушение и сушка бетона: торопясь с ожиданием
В напольных покрытиях, будь то готовый бетон или нанесенный пол, всегда присутствует элемент «поторопитесь и подождите» — желание двигаться вперед, но зная, что торопливость может закончиться слишком быстро. в случае поломки или поломки пола. Выполнение требований к бетону и напольным покрытиям может показаться роскошью, которая не всегда доступна подрядчику в сжатые сроки.
Осушение — это один из процессов, который часто используется для ускорения высыхания бетонной плиты до места установки.Основная концепция проста: уменьшить точку росы воздуха, окружающего плиту, чтобы большая часть скрытой влаги внутри плиты могла испаряться через поверхность плиты. В строительной индустрии существует несколько распространенных подходов к осушению: осушение конденсацией, осушение с помощью нагрева (или сушки) и осушение адсорбентом.
Осушители воздуха на основе адсорбентов используют химическое притяжение для удаления влаги из воздуха. Влажный воздух проходит через осушающий материал, который связывает и удерживает влагу.Затем используется поток горячего воздуха, чтобы высвободить влагу из осушителя и отвести ее от окружающей среды плиты. Затем высушенный адсорбент впитывает больше влаги и снова высвобождает ее при нагревании в непрерывном процессе. Этот процесс не зависит от внешних погодных условий, поэтому его можно использовать круглый год, если бетонная плита может быть изолирована от погодных условий.
В процессе конденсации используются осушители на основе охлаждения, которые охлаждают воздух, эффективно снижая точку росы, чтобы влага могла собираться и отводиться.В отличие от этого, при осушении используется нагретый воздух для повышения точки росы окружающего воздуха, позволяя ему поглощать больше влаги с поверхности плиты. Затем насыщенный воздух циркулирует либо через систему сбора, либо в наружный воздух, где он выделяет излишнюю влагу при охлаждении. Здесь следует отметить, что большинство установленных систем HVAC не способны удалить количество влаги, выделяемой в процессе высыхания бетонной плиты. Хотя можно повысить или понизить температуру окружающей среды с помощью системы HVAC, осушение должно активно удалять излишки влаги из конструкции.Если влага просто перемещается внутри стен, избыток влаги может со временем вызвать рост плесени или износ оборудования.
Настоящий ключ к успешному осушению — это полностью закрытая бетонная плита, чтобы влага, удаленная во время процесса, не возвращалась в окружающую среду плиты. Либо плита должна быть ограждена в готовых к эксплуатации внутренних условиях, либо вокруг нее необходимо возвести пароизоляцию для наружных условий. Точное тестирование относительной влажности (RH) позволяет точно отслеживать движение влаги из плиты.После того, как плита достигнет желаемого уровня относительной влажности и будет нанесена отделка или пол, бетон будет оптимально поддерживать качественную отделку, которая прослужит долгие годы. Система измерения влажности Rapid RH®
Wagner Meters может помочь вам легко и точно измерить относительную влажность, чтобы вы могли отслеживать влажность плиты во время процесса осушения. С 2002 года испытания на относительную влажность ASTM-F2170 на месте заменили хлорид кальция в качестве предпочтительного метода определения влажности бетона.
Позвоните Вагнеру сегодня по телефону (541) 291-5123 или закажите систему измерения влажности Rapid RH ® онлайн.
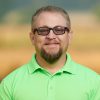
Джейсон имеет более чем 20-летний опыт продаж и управления продажами в различных отраслях промышленности и успешно выпустил на рынок ряд продуктов, в том числе оригинальные испытания на влажность бетона Rapid RH®. В настоящее время он работает с Wagner Meters нашим менеджером по продажам продуктов Rapid RH®.
Быстросохнущая акриловая краска для бетонных полов
Быстросохнущая акриловая краска для пола для бетона
Проект | Компонент A | Компонент B | ||
Часы использования | 2 часа (10 ℃) | 1 час (25 ℃) | 45 мин (30 ℃) | |
Время отверждения | Сухая поверхность | 12 часов (10 ℃) | 8 часов (25 ℃) | 3 часа (30 ℃) |
Жесткая сушка | 48 часов ( 10 ℃) | 36 часов (25 ℃) | 24 часа (30 ℃) | |
Избыточный вес | 7 дней (10 ℃) | 4 дня (25 ℃) | 2 дня (30 ℃) | |
Дозировка | 1.55 ± 0,55 | 0,95 ± 0,02 | ||
Цвет | Дополнительно | Мягко-желтый | ||
Пропорция | Компонент A: Компонент B = 5: 1 | |||
VOC | ≤2% (после смешивания) |
1 .0004Каков ваш MOQ (минимальное количество заказа)?
Наше минимальное количество заказа составляет 1000 кг, и мы принимаем смешанные заказы.
2. Образец бесплатный?
Предлагаем бесплатный образец в пределах 1 кг, достаточно оплатить фрахт.
3. Можете ли вы сделать OEM?
Да, мы можем сделать бренд, логотип и другой размер упаковки в соответствии с вашими требованиями.
4. Можем ли мы посетить ваш завод?
Приглашаем Вас посетить наш завод, мы будем очень рады!
Почему сухое шлифование не работает как метод подготовки поверхности для герметиков для бетонных столешниц
Меня часто спрашивают, можно ли использовать сухое шлифование бетона для подготовки бетонной поверхности для нанесения Omega Concrete Countertop Sealer TM или любого другого герметика для покрытия. Ответ — нет.
Сухое шлифование — это не то же самое, что мокрое шлифование, даже с такой же зернистостью. Сухая шлифовка / полировка приводит к полировке бетонной поверхности, что делает ее слишком гладкой для хорошей адгезии герметика. Это касается любого герметика для покрытий, а не только Omega.
Практика сухой шлифовки бетона с использованием сухой наждачной бумаги часто рассматривается как простая, быстрая, легкая и «бережная» по отношению к бетону. К сожалению, у этой практики есть и обратная сторона, которая не очевидна, пока не придет время заделывать бетон.
Сухое шлифование приводит к полировке поверхности. Это означает, что вместо того, чтобы равномерно шлифовать поверхность, чтобы получить первозданную, свежую и незагрязненную поверхность, сухое шлифование часто делает поверхность более гладкой и блестящей, чем это было вначале.
Кроме того, загрязняющие вещества, такие как воск и смазки для форм, которые были захвачены из формы во время литья, имеют тенденцию проникать в бетонную поверхность вместо того, чтобы их стирать.
В результате бетон, как правило, слишком гладкий и, возможно, загрязненный. Оба условия могут привести к нарушению адгезии герметика.


Полировка с использованием сухих алмазных дисков (зерно 200, слева) и обычной наждачной бумаги (зерно 220, среднее и 80, справа). Нешлифованный бетон — это более светлая область на дальней левой стороне бетона.


Полированный блеск наждачной бумаги зернистостью 220 и 80.
Причина, по которой сухое шлифование приводит как к полировке бетона, так и к рабочим загрязнениям на поверхности, связана с процессом шлифования. Большая часть используемой наждачной бумаги предназначена для дерева, хотя некоторые также продаются для металла. Абразивные зерна, как правило, немного тверже, чем бетон (или намного тверже, в зависимости от возраста бетона), поэтому при шлифовке образуется пыль и песок. Эта пыль и песчинки имеют тенденцию задерживаться под шлифовальной подушкой, и как абразивные частицы, так и частицы бетона действуют на бетонную поверхность.При недостаточном удалении пыли под шлифовальной тарелкой абразивные частицы и абразивные частицы вскоре начнут полировать поверхность, а не врезаться в нее, поскольку бетонная пыль и песок имеют такую же твердость, как и поверхность. Загрязняющие вещества обычно находятся на поверхности бетона, и если только верхняя поверхность отшлифована и отполирована, при недостаточной очистке от пыли, загрязненная пыль возвращается обратно на поверхность, создавая проблемы со связкой для вашего герметика.
Сухая полировка алмазными подушечками на электрическом или пневматическом полировальном станке позволяет получить обрезки бетона, которые не смываются, как при влажной полировке.Поскольку порошкообразные стружки, как правило, дольше остаются под полировальной головкой, они разрушаются и действуют как более мелкие полировальные средства. Вот почему сухая полировка более эффективна, чем влажная, при попытке отполировать бетон до зеркального блеска, потому что сами по себе обрезки бетона действуют как более тонкий полировальный состав, чем алмазный диск, который их создал.
Кроме того, сверхмелкие стружки проникают в открытые поры бетонной поверхности, загрязняя поверхность, что может вызвать нарушение адгезии.
Вот подробное видео, показывающее, как сухое шлифование полирует поверхность:
Что делать, если вы отшлифовали бетон сухим способом и теперь хотите герметизировать с помощью Omega?
Еще не все потеряно, и перед вами тоже не стоит грандиозная задача.
Omega (и все покрытия с высокими эксплуатационными характеристиками) опираются на слегка шероховатую микротекстуру поверхности для создания прочной и долговечной связи с бетоном. Таким образом, сухая шлифовка (и даже сухая полировка алмазами) предотвращает то, что необходимо для адгезии герметика.
Если вы отшлифовали бетон сухим способом и у вас все еще есть цементно-кремовая отделка, то проще всего отшлифовать вручную, используя наждачную бумагу для влажного / сухого нанесения из карбида кремния с зернистостью от 320 до 400. Карбид кремния намного тверже, чем бетон, поэтому он легко стирает поверхность, но не удалит кремовую отделку. А поскольку это мелкая зернистость, 320 не оставит глубоких царапин, которые будут видны сквозь герметик. Влажное шлифование помогает смыть обрезки и предотвращает нагревание трением, которое может привести к смазыванию и полировке.Будьте внимательны и убедитесь, что вся поверхность равномерно отшлифована.
Если вы шлифовали бетон в сухом виде и на нем были обнаженные зерна песка или декоративный заполнитель (например, стекло или камень), вам нужно отшлифовать более твердый заполнитель чем-то более агрессивным, чем наждачная бумага. Самый простой и быстрый способ сделать это — использовать влажный алмазный полировальный диск (зернистость 100 или 200), прикрепленный к обычной шлифовальной машине с произвольным вращением. Просто распылите немного воды на бетон, чтобы он намок, и «отшлифуйте» поверхность с помощью алмазного диска, чтобы стереть полированную поверхность.Будьте очень внимательны, так как орбитальные шлифовальные машины далеко не так агрессивны, как мокрые полировщики. Если все сделано правильно, это даст вам поверхность, которая позволит Omega прочно сцепиться с бетоном.
Вот видео о процессе (в контексте удаления существующего покрытия и повторной герметизации с помощью Omega):
.
Насос быстрого высыхания Применяет цементную основу для выравнивания бетонных полов
Быстросохнущая подстилка на цементной основе, применяемая насосом для выравнивания бетонных полов
Введение:
Самовыравнивающийся цемент для стяжки пола, другое название: Самовыравнивающаяся смесь для пола, она изготовлена из сложного заполнителя специального цемента и иностранного полимера распыления сухой смолы и специальную добавку, она принимает иностранную технику и формулу, это нетоксичный и окружающей среды.Это высокая прочность и супер текучесть наливные смеси. Он облегчает работу с высокой текучестью и обладает отличной стойкостью к истиранию с высокой прочностью.
Характеристика:
a. Высокая ликвидность, точное автоматическое выравнивание.
б.Быстрая установка и ранняя прочность, повышение эффективности строительства.
c. Низкая согласованность и простота конструкции.
г.Применяется для обогрева пола.
E: улучшить интенсивность нижних слоев, избегая растрескивания.
Применение:
a. Самонивелирующаяся цементная обработка поверхности раздела: используется для обработки базового курса перед наземным строительством самовыравнивающегося цемента, улучшает прочность сцепления между самовыравнивающимся и базовым курсом. 1
b. Связь между старым и новым бетоном: используется для армирования швов и колонны балки, реконструкция старого фундамента, способного улучшить прочность на сдвиг в 3 раза.
c. Гладкое основание штукатур курс: заменить ровную бетонную поверхность процесса натриево-промывной удаления масла и ручной черновой обработки, способной улучшить связывающую силу в течение 6 раз.
д. Кирпич плита мощение: Интерфейс покрытие или тротуарной блок борт, непосредственно после того, как обработано в высокую силу склеивания строительного раствор, и с ним можно вставить новый кирпич на старом кирпиче.
эл. Бетон ремонт и защита поверхностей: используется для защиты поверхности бетона и стальной прут, чтобы предотвратить износ и коррозию.
ф. Загрязнение нефти, Обсахаривание лечения Базового курса: покрытие и делать штукатурку обработки непосредственно для удаления пыли и загрязнений немного базового масла конечно.
г.Водонепроницаемый и влагостойкие, антикоррозионные: имеется в наличии построить на влажной базовой конечно, могут быть использованы в качестве изолирующего слоя влажного маслянистого покрытия, склеивания плотно с полиуретановым покрытием.
Технические данные:
Технические данные:
(Температура: 20-25, относительная влажность: 48% -55%)
Соотношение смешивания: мощность: вода = 25 кг: 5,5 л
| Сопротивление сжатию: Около 4 МПа через 1 день; О 17Mpa через 7 дней; Около 21Mpa после 28 дней. |
Плотность сухого порошка: около 1,3 кг / л
| |
Плотность свежеприготовленного клея: около 2,0 кг / л
| Прочность при складывании: Примерно 1 МПа через 1 день; О 4Mpa через 7 дней; О 5Mpa после 28 дней. |
Время работы: (20) около 30 мин.
| |
Время верхней отделки: около 24-48 часов | Жесткость падающего шара: Около 25 МПа через 1 день; Около 60Mpa через 7 дней. |
Хранение:
A: Хранить в прохладном сухом помещении. Этот продукт на цементной основе, обратите внимание на уплотнение, чтобы предотвратить
сырости.
B: нераспечатанный продукт имеет срок годности 12 месяцев.
1: Промывка интерфейсным агентом
Для самовыравнивающегося цемента ключевым этапом является даже один или два раза.
2: Добавить воду для смешивания
Добавить воду в соответствии с требованиями производителя, лучше использовать градуированный цилиндр, перемешивание 3-5 минут
3: Заливка, Соскоб общий 2-4Мм.
4: Пеногаситель
После засыпки грунта с помощью противопенного инструмента для удаления пузырьков воздуха.
5: Protect
После самовыравнивающегося цементного раствора до Мастера требуется 24 часа.
Изображение:
Транспортное изображение:
,