Штукатурка стен из газосиликатных блоков
Блоки на газосиликатной основе широко используются в качестве стройматериала для возведения зданий. Они обеспечивают повышенную теплоизоляцию строений, однако из-за пористой структуры впитывают влагу. Сформировать защитное покрытие стены позволяет штукатурная смесь. Вначале черновая штукатурка для газосиликатных блоков укладывается на подготовленную поверхность. Затем наносится тонкий слой раствора и выполняется затирка. Покрытие стены из газобетона, оштукатуриваемой сухими смесями, позволяет предотвратить растрескивание материала из-за переувлажнения.
Свойства газосиликатного материала и его защита при помощи штукатурного слоя
Силикатные блоки представляют собой современный строительный материал, отличающийся ячеистой структурой. Они изготовлены из смеси кварцевого песка и цемента, в которую добавлены алюминиевая пудра и известь. При перемешивании ингредиентов происходит химическая реакция, в результате которой газосиликатный раствор увеличивает свой объем и затем твердеет в специальных формах.
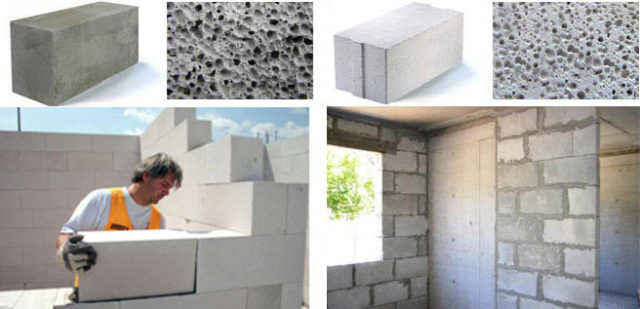
В результате реакции газообразования блоки приобретают пористую структуру, определяющую главные эксплуатационные характеристики материала:
- пониженную теплопроводность. Газосиликатные стены уменьшают потери тепловой энергии и позволяют снизить расходы на отопление;
- способность поглощать шум. Неравномерно распределенные внутри блоков ячейки препятствуют проникновению в помещение посторонних шумов;
- повышенную паропроницаемость. Сквозь поры осуществляется воздушный обмен, улучшающий микроклимат жилого помещения.
Кроме того, блоки обладают энергосберегающими свойствами. Они постепенно аккумулируют тепловую энергию, которая затем передается помещению и повышает в нем температуру.
Силикатные блоки положительно зарекомендовали себя в области малоэтажного и промышленного строительства благодаря следующим достоинствам:
- уменьшенному весу;
- повышенным прочностным характеристикам;
- увеличенному объему;
- правильной геометрии;
- минимальным допускам на габариты;
- хорошей обрабатываемости;
- экологической чистоте;
- морозоустойчивости;
- пожарной безопасности.
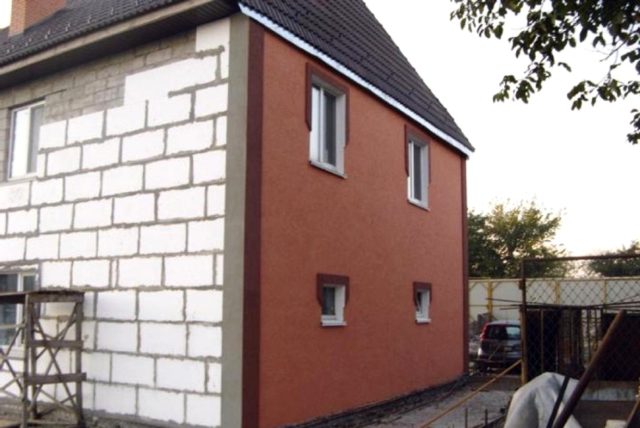
Газосиликат также устойчив к образованию грибков и развитию плесени. По эксплуатационным характеристикам газосиликатные блоки похожи на изделия из вспененного бетона. Однако оба материала имеют ряд серьезных недостатков, для устранения которых производится штукатурка газосиликатных блоков, а также выполняется штукатурка пеноблоков.
Необходимость оштукатуривания поверхности пористых блоков связана со следующими свойствами материала:
- повышенной гигроскопичностью. Пористый газосиликат склонен к поглощению влаги, которая вызывает постепенное разрушение материала при отрицательной температуре, а также способствуют развитию микроорганизмов. Для предотвращения растрескивания блоков выполняется их оштукатуривание;
- пониженным сцеплением ячеистой поверхности блоков с отделочными материалами. К пористому газосиликату плохо пристают штукатурные смеси на основе песка и цемента, а также штукатурки на базе извести. Выполнение отделочных мероприятий позволяет повысить адгезию;
- конденсацией влаги внутри газосиликатного массива. В результате интенсивного воздухообмена, происходящего в условиях температурных перепадов, внутри блоков собирается влага. Она затрудняет выход из помещения воздушных паров и отрицательно влияет на микроклимат.
Для обеспечения адгезии газосиликатной поверхности проводят следующие работы:
- покрывают газосиликат специальным раствором. Проникающий вглубь ячеистого газосиликата грунт улучшает адгезионные свойства;
- усиливают газосиликатную поверхность металлической, капроновой или стекловолоконной сеткой. Она позволяет нанести увеличенный слой штукатурки;
- последовательно наносят несколько слоев штукатурки. Послойная отделка позволяет создать гладкую поверхность с повышенными адгезионными свойствами.
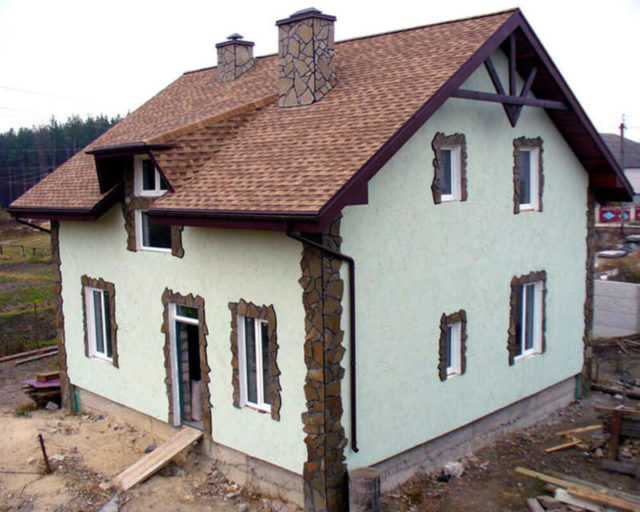
Необходимость защиты поверхности газосиликатных блоков и других изделий из пористых бетонов обусловлена их ячеистой структурой. Отделка газосиликатных стен – обязательное мероприятие.
Назначение оштукатуривания:
- предотвращение разрушения газосиликатных стен в результате температурных колебаний;
- защита газосиликатных блоков от интенсивного поглощения влаги и развития микроорганизмов;
- улучшение внешнего вида различных зданий, стены которых возведены из газосиликатных блоков;
- снижение объема тепловых потерь через незащищенную поверхность газосиликатных стен;
- обеспечение комфортных условий внутри помещения за счет обеспечения повышенной звукоизоляции;
- выравнивание поверхности стен после кладки блоков, позволяющее создать плоскую основу для финишной отделки;
- защита стен из блоков от образования трещин, позволяющая повысить срок эксплуатации здания.
Газобетон восприимчив к влиянию факторов природного характера – воздействию осадков, ультрафиолетовым лучам и выветриванию. Кроме того, пористый газосиликат разрушается в результате повреждений механического характера. Оштукатуривание стен из газосиликатных блоков обеспечивает надежную защиту на протяжении периода эксплуатации.
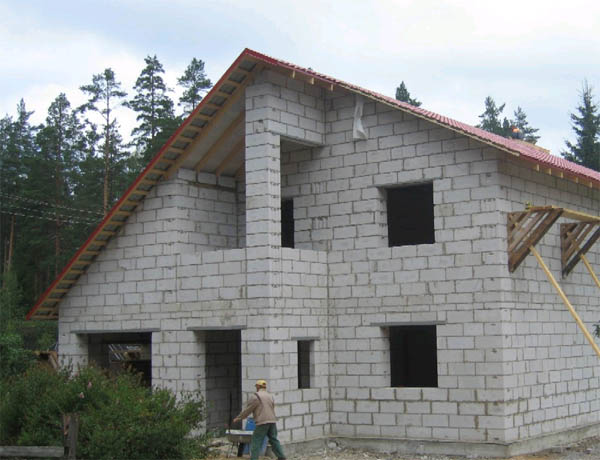
Подготавливаем необходимый инструмент и стройматериалы
Предварительная подготовка строительных материалов и необходимого инструмента ускорит выполнение отделочных работ и повысит их производительность.
Для штукатурки газосиликатных стен следует подготовить:
- правило, предназначенное для растягивания штукатурной смеси вдоль маяков. Длина правила выбирается в зависимости от расстояния между маяками;
- металлические направляющие, называемые маяками, и позволяющие обеспечить плоскостность. Маяки служат ориентиром при работе с правилом;
- дрель с насадкой или миксер. Они используются для обеспечения ускоренного и однородного перемешивания штукатурного раствора;
- мастерок и шпатели с расширенной рабочей поверхностью. Инструмент используется для набрасывания и выравнивания штукатурной смеси;
- отвес, строительный уровень, рулетка. Они применяются в процессе разметки и используются для контроля в ходе штукатурных мероприятий.
Также потребуется широкая кисть или валик для нанесения на поверхность блоков грунтовочного состава. Для выполнения замеса нужна соответствующая емкость, а для фиксации сетки потребуются гвозди или дюбеля.
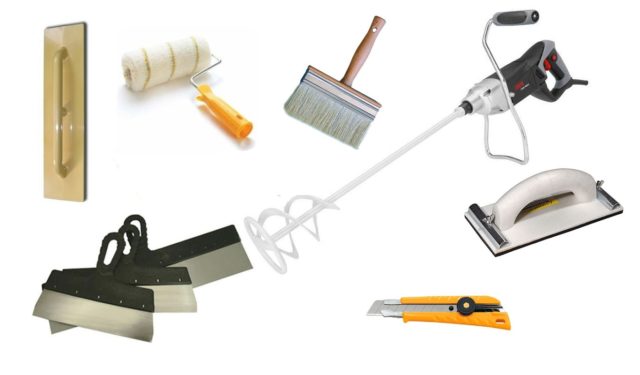
Кроме инструментов необходимо приобрести следующие материалы:
- адгезионную смесь для грунтования. Она обеспечивает повышенную адгезию штукатурки с газосиликатными блоками;
- сетку для армирования поверхности. Сетчатое усиление затрудняет образование трещин и укрепляет слой отделки;
- сухую смесь для штукатурных работ. Готовый состав для штукатурки несложно приобрести в специализированных магазинах.
Подготовив все необходимое, приступайте к выполнению работ.
Штукатурная смесь для газосиликатных блоков – выбор качественной штукатурки
Начинающие отделочники и домашние умельцы часто задают вопрос, чем оштукатурить газосиликатные блоки, а также какие требования предъявляются к штукатурной смеси.
В строительных супермаркетах несложно приобрести штукатурные составы известных производителей:
- фирмы Knauf;
- торговой марки Ceresit;
- компании EuroMix;
- бренда PROFIT.
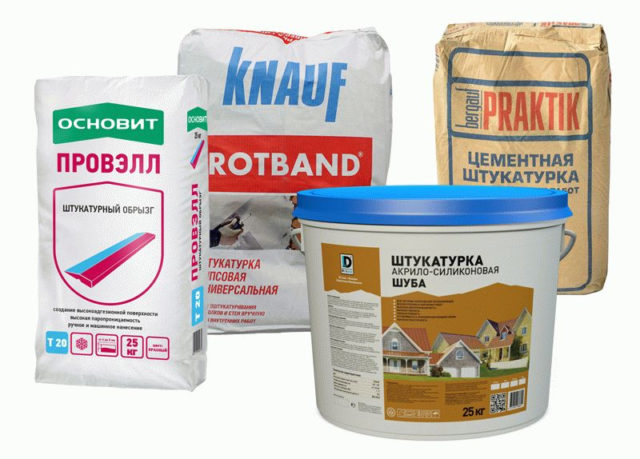
Наряду с импортными штукатурными смесями и грунтовками предлагаются также отделочные смеси, изготовленные отечественными изготовителями. Расширенный ассортимент штукатурных составов затрудняет принятие правильного решения начинающими мастерами. Проконсультироваться, чем штукатурить газосиликатные блоки внутри, можно с продавцами строительных отделов. Профессионалы предложат оптимальный вариант штукатурки и посоветуют также, чем штукатурить газосиликатные блоки снаружи здания.
Приобретая готовую штукатурку для выполнения внешних и внутренних отделочных работ, следует учитывать ряд факторов:
- область использования штукатурки;
- адгезионные свойства смеси;
- стойкость к отрицательной температуре;
- паропроницаемость штукатурки после твердения;
- влагоизоляционные характеристики;
- экологическую чистоту отделочного материала;
- срок годности состава;
- имидж изготовителя;
- продолжительность схватывания.
При наличии необходимых компонентов несложно самостоятельно приготовить штукатурный раствор. Для этого следует взять в равных соотношениях цемент и известь, перемешать с тремя частями песка и разбавить полученную смесь водой до нужной консистенции. Добавление мела повысит пластичность штукатурного состава и облегчит его нанесение.
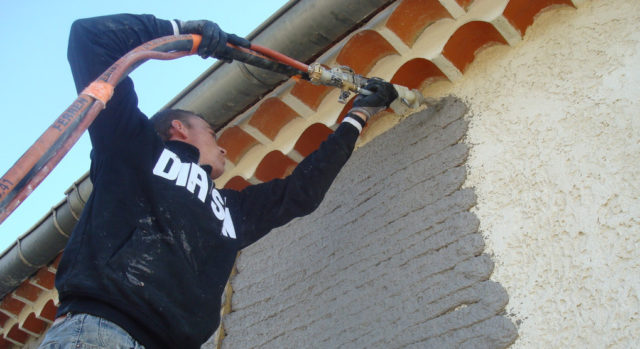
Внутреннее оштукатуривание стен из газосиликатных блоков – этапы работ
Согласно технологии, выполнение внутренних работ по оштукатуриванию газосиликатных стен включает следующие этапы:
- Очистку стен от загрязнений.
- Пропитку газосиликатного материала специальным грунтом.
- Монтаж сетки к газосиликатной поверхности.
- Послойное нанесение штукатурного раствора.
- Заключительные мероприятия по финишной отделке.
Остановимся на особенностях каждой стадии работ.
Подготавливаем поверхность стены к обработке специальной грунтовкой
Подготовка поверхности газосиликата – ответственный этап, обеспечивающий адгезию и влияющий на качество штукатурных работ.
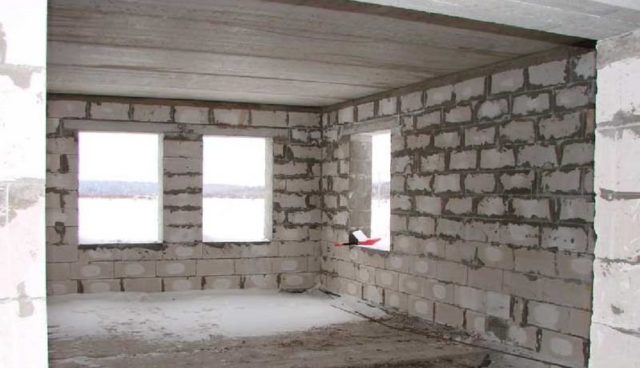
Подготовительные мероприятия включают:
- Обеспыливание газосиликата.
- Удаление старого покрытия и грязи.
- Обезжиривание проблемных участков.
- Ликвидацию маслянистых следов.
- Увеличение глубины швов газосиликатной кладки.
Не всегда имеется возможность удалить металлической щеткой проникшие в газоблочный массив масляные и жировые пятна. В этом случае их вырубают с помощью зубила.
Нанесение грунтовки на газобетон внутренних стен и перегородок
Обработка газосиликата грунтовочным составом решает следующие задачи:
- повышает адгезию блоков с отделочной смесью;
- надежно герметизирует внутренние полости;
- придает газосиликатной поверхности дополнительную шероховатость.
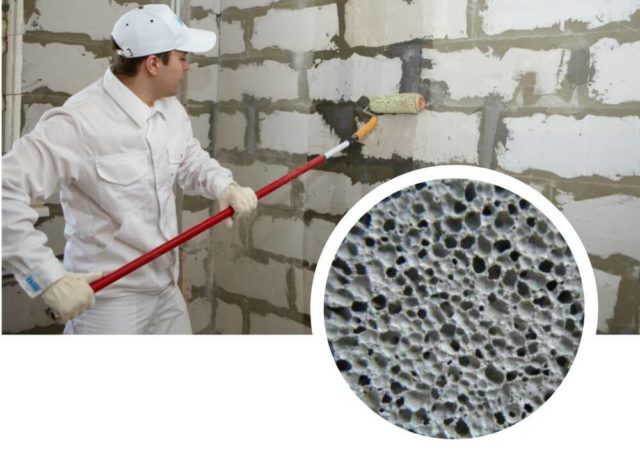
Грунтование блоков осуществляется различными методами:
- вручную, с помощью малярной кисти или широкого валика;
- с применением пульверизатора, позволяющего покрыть увеличенную площадь.
Грунт следует наносить равномерным слоем, уделяя особое внимание труднодоступным местам в области углов и проемов. Штукатурка по газосиликатным блокам выполняется после окончательного высыхания грунта.
Крепим армирующую сетку к газосиликатным блокам
Укрепление блоков штукатурной сеткой обеспечивает улучшенное сцепление штукатурки. Крепление сетки осуществляется различными способами:
- путем крепления металлической сетки к газосиликатной поверхности дюбелями или с помощью гвоздей;
- методом вдавливания стекловолоконной или капроновой сетки в предварительно набросанный слой отделочного состава.
Армирование сеткой в сочетании с грунтованием позволит добиться повышенной адгезии. После монтажа сетки следует закрепить маяки, а также увлажнить газосиликатную поверхность пульверизатором или кистью для лучшего проникновения отделочного состава.
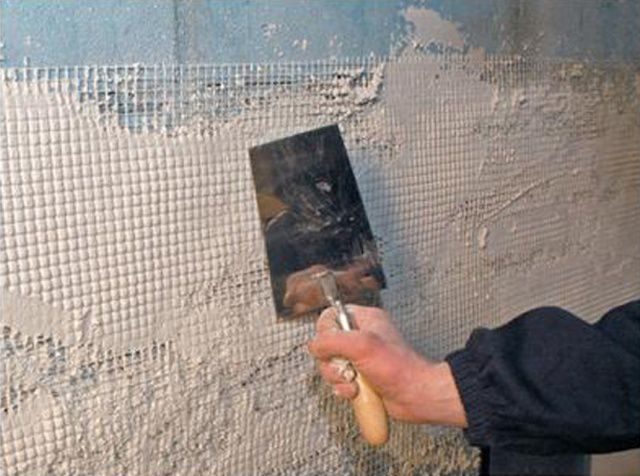
Штукатурка для газосиликатных блоков – процесс отделки газобетонного материала
Разберемся, как правильно штукатурить стены из газосиликатных блоков. Оштукатуривание осуществляйте в указанном порядке:
- Набросьте мастерком слой штукатурной смеси на газосиликатную кладку.
- Распределите правилом отделочный состав вдоль направляющих.
- Удалите затвердевшие комки штукатурки после застывания.
Не нужно пытаться обеспечить идеальную плоскостность. Следует просто распределить смесь по площади стен.
Нанесение финишного слоя после окончания черновых работ
На завершающей стадии отделочных мероприятий выполняются следующие работы:
- Черновая штукатурка покрывается грунтом.
- Осуществляется финишная штукатурка газосиликата.
- Удаляются неровности и наносится финишная шпаклевка.
Внутренняя штукатурка стен из газосиликатных блоков на финишном этапе приобретает необходимую плоскостность в процессе шлифовки и затирки.
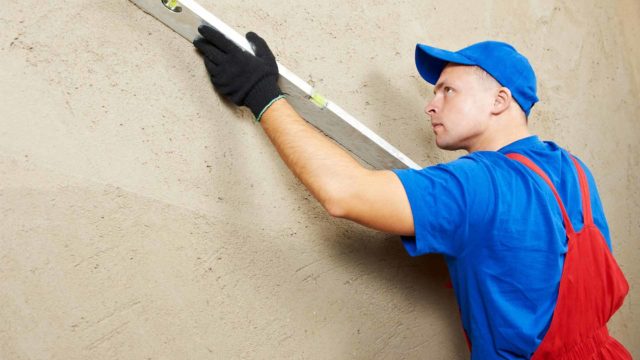
Оштукатуривание внешних стен штукатурными составами
Для фасадной отделки строения применяется оштукатуривание стен цементно-песчаным раствором, в который добавляются ингредиенты для повышения водостойкости.
Такая штукатурка газосиликатных блоков цементным раствором выполняется по следующему алгоритму:
- Очищается фасад строения от загрязнений.
- Наносится грунт на поверхность газосиликата.
- Выполняется монтаж металлической сетки.
- Наносится штукатурка для газосиликатных блоков фасадная.
Улучшенное эстетическое восприятие отделки достигается покрытием поверхности краской.
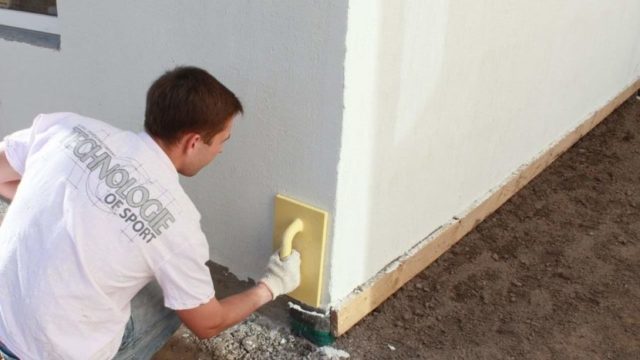
Внешняя и внутреняя штукатурка стен из газосиликата – полезные советы
При самостоятельном выполнении штукатурных работ следует руководствоваться советами и рекомендациями профессиональных отделочников.
Они акцентируют внимание на следующих нюансах:
- выполнении работ при температуре 5-30 градусов Цельсия. При такой температуре окружающей среды обеспечивается нормальное высыхание штукатурки;
- необходимости послойного нанесения отделочной смеси. При этом финишный слой штукатурки наносится только после высыхания основного;
- целесообразности увлажнения поверхности. При повышенной температуре распыление жидкости предотвращает образование трещин;
- соотношении толщин наружной и внутренней отделки, равном 2:1. Это позволяет сместить точку росы и не допустить конденсацию влаги внутри блоков.
Учтите также, что оптимальная толщина внутреннего отделочного слоя составляет 8-14 мм. Профессионалы обращают внимание на то, что отделку газосиликата допускается производить через месяц после завершения кладки стен.
Заключение
Самостоятельно выполненное оштукатуривание стен из газосиликатных блоков позволяет значительно сэкономить. Качественно выполненная штукатурка надежно защитит газосиликатные блоки. Приступая к отделочным работам впервые, тщательно изучите требования технологии и серьезно отнеситесь к выбору отделочного материала. Советы опытных строителей помогут избежать ошибок.
Ценовая доступность и высокие эксплуатационные характеристики сделали газобетон одним из наиболее применяемых строительных материалов при возведении малоэтажных домов. После окончания этапа непосредственной постройки возникает вопрос окончательной отделки дома. Штукатурка газосиликатных блоков снаружи является наиболее распространенным методом. Это связано с относительно невысокой стоимостью самого отделочного материала и простотой технологии проведения работ – любой владелец дома, умеющий держать в руках инструмент, в состоянии осуществить оштукатуривание самостоятельно.
Внутреннее оформление стен подобным способом также применяется довольно часто. Однако существуют определенные нюансы проведения отделки. В первую очередь, это связано со свойствами самого газобетона. Попробуем разобраться подробнее, как, когда и чем штукатурить газосиликатные блоки внутри дома и проводить наружные работы.
Преимущества газосиликата
Для начала кратко остановимся на эксплуатационных характеристиках строительного материала. Газобетон имеет ряд явных достоинств, объясняющих популярность его применения. Помимо уже упоминавшейся привлекательной стоимости, к ним относятся:
- Четко выдержанный размер блоков. Это позволяет производить укладку идеально ровными рядами, причем для сцепления блоков используется не толстый слой обычного раствора, а тонкая прослойка специального клеевого состава. В результате в кладке не образуются доставляющие много неудобств в дальнейшем «мостики холода».
- Малый вес. От общей массы строения зависит интенсивность нагрузки на фундамент и, как следствие, вероятность неравномерной усадки. При соблюдении технологии укладки легких газобетонных блоков и проведении необходимых процедур по армированию строения можно не опасаться перекосов дома и появления стеновых трещин.
- Тепло- и звукоизолирующие свойства. По этому показателю газосиликат занимает лидирующие позиции среди основных строительных материалов. Пористая структура создает отличные энергосберегающие характеристики и препятствует проникновению внешнего шума.
- Высокая паропроницаемость. Это свойство материала обеспечивает поддержание постоянного микроклимата во внутренних помещениях. В доме не будет сыро во время дождя, и не придется пользоваться увлажнителями воздуха в засушливую жару.
Подбор штукатурки
Именно повышенной паропроницаемостью объясняется отличие технологии штукатурки газосиликата от проведения аналогичных работ на поверхности стен из других стройматериалов. Если нанести на газобетон сплошное покрытие, не обладающее соответствующим коэффициентом пропускания влаги, в результате вероятно возникновение неприятных последствий:
- штукатурка будет трескаться и осыпаться, причем этот процесс возможен как снаружи дома, так и изнутри;
- внутри замкнутого помещения влажность будет постоянно повышена;
- как следствие предыдущего пункта – грибок и плесень станут привычными обитателями углов и плинтусов;
- на штукатурке стен будет отчетливо проявляться рисунок кладки блоков, исчезающий после проветривания и высушивания комнаты.
Чтобы избежать подобных проблем, для проведения штукатурных работ нужно использовать специальные составы. В таблице приведен перечень основных требований к отделочным материалам для газобетона.
Уровень адгезии | В пределах 0,5 МПа |
Пропорция разведения | Не более 8 литров воды на 30 кг штукатурной смеси |
Минимальная толщина слоя | 2 мм |
Максимальная толщина слоя | 8 – 15 мм |
Время использования раствора | Не менее 3-4 часов |
Расход сухого состава | 30 кг на квадратный метр при минимальной толщине слоя |
Прежде чем приобретать сухую смесь, внимательно ознакомьтесь с ее характеристиками и определите, можно ли штукатурить газобетонные стены с ее помощью.
Стоимость штукатурных составов, обладающих подобными параметрами, несколько выше, чем у обычной штукатурки, основанной на смеси цемента с песком. Однако за счет более тонкослойного нанесения удается избежать существенного удорожания отделки.
С вопросом «Чем оштукатурить?» разобрались. Теперь переходим непосредственно к описанию того, как правильно штукатурить стены из газосиликатных блоков.
Проведение внутренних работ
Внутренняя отделка всегда начинается с этапа подготовки стен. Поскольку одним из достоинств газобетонных блоков является стандартный размер, предварительное выравнивание поверхности и удаление выступающих излишков клеевого состава легко производится при помощи специальных затирочных сеток или наждачной бумаги. При необходимости можно воспользоваться шлифовальной машинкой.
Далее процесс штукатурки внутри помещения производится по стандартному алгоритму:
- Грунтовка стен. Строительный рынок предлагает широкий выбор различных средств. Рекомендуется использовать составы, изготовленные на основе акрилосилоксана. При выборе необходимо учитывать целевое предназначение помещения: жилые комнаты, санузел (зона повышенной влажности), неотапливаемая часть дома.
- Закрепление армирующей составляющей. Перед тем как оштукатурить стену, по всей поверхности крепим сетку из специального стекловолокна, нечувствительного к воздействию щелочных составов и обладающего высоким сопротивлением к разрывным нагрузкам.
- Установка маячков. Для этого используются длинные профили, размещаемые вертикально вдоль стены на ширину правила и закрепляемые при помощи шпаклевки. Горизонтальность и вертикальность установки маячков проверяется строительным уровнем.
- Наброска шубы. Производится вручную или при помощи штукатурной машины. Не нужно набрасывать слишком много – материал будет отваливаться. Оптимальная толщина слоя – от 4 до 8 мм. Затем при помощи опирающегося на маячки правила производим протяжку сырой штукатурки по поверхности стены. Все работы осуществляются по направлению снизу вверх. Возникающие пустоты заделываем прямо в процессе протяжки. В результате уплотняем слой штукатурки до толщины 2-3 мм.
- Завершающая стадия. Слегка подсохшую штукатурку выравниваем круговыми движениями широкого металлического шпателя. Убираем маячки и заделываем оставшиеся на месте их крепления дефекты. После полного высыхания штукатурки производим окончательную затирку поверхности.
Внешняя отделка
Технология наружного оштукатуривания практически не отличается от описанного выше процесса внутренних работ.
Единственная разница заключается в толщине покрытия: если на внутренней поверхности достаточно 1-2 слоев, то снаружи тонкослойный метод предполагает нанесение 3 слоев, а толстослойный – 5-6. Штукатурка для наружных работ применяется такая же, как и внутри.
Каждый слой накладываемой штукатурки обязательно армируется при помощи сетки из стекловолокна. Естественно, это приводит к определенным расходам. Однако лучше потратить небольшую сумму на этапе отделки, чем заново оплачивать ремонт по прошествии всего нескольких лет.
Нанесенному слою необходимо дать время на полное высыхание, и лишь затем переходить к формированию следующего. Поэтому работы предпочтительнее осуществлять в теплое время года: паузы в производственном процессе будут короче.
После окончательного высыхания штукатурки можно произвести покраску поверхности. При этом рекомендуется использовать только специальные паропроницаемые краски, например, PASTEL, ATLAS или ARKOL S.
Особенности штукатурки
Основные нюансы проведения работ связаны опять же с паропроницаемостью газосиликата. Заводская технология изготовления блоков предусматривает выпуск в продажу изделий с внутренней влажностью 30%. Для проведения наружной отделки этот показатель должен составлять не более 15%. Поэтому желательно не переходить к отделочным работам сразу, а дать строению «подышать» в течение некоторого времени.
В дальнейшем вначале производим внутреннее оштукатуривание. Это обязательное правило. Если начать с проведения наружных работ, накопившаяся в материале влага не будет иметь выхода, и с наступлением холодов в лучшем случае штукатурка начнет отваливаться, а в худшем – появятся трещины в самих стенах.
После окончания работ внутри делаем значительную паузу. В идеале дом должен простоять без внешней отделки не менее 1 — 1,5 года. Прочностные свойства газобетона позволяют пережить такой длительный промежуток без ухудшения дальнейших эксплуатационных характеристик. Зато качественная внешняя штукатурка, нанесенная на выстоявшиеся блоки, способна прослужить не менее 15 лет.
Еще одна особенность, которую нужно учитывать при выборе способа внешнего оформления фасадов — армирование стен в процессе возведения. Наружная штукатурка применяется только в том случае, если технология строительства предусматривала дополнительную закладку арматуры через каждые 3-4 ряда стеновых блоков. Если же укрепление дома ограничилось возведением монолитных поясов на уровнях межэтажных перекрытий и под мауэрлатом, от использования штукатурки рекомендуется отказаться. В таком случае лучше использовать обшивку сайдингом, вагонкой или декоративным камнем. Нарушение этого правила чревато появлением трещин и осыпанием штукатурки.
Ошибки
Все проблемы, возникающие в процессе проведения работ или дальнейшей эксплуатации дома, связаны с применением неподходящих материалов или нарушением технологии. Чтобы гарантировать себе комфортное проживание в уютной обстановке, при проведении оштукатуривания достаточно следовать таким рекомендациям:
- не торопимся начинать работы сразу по окончании строительства;
- не штукатурим дом, в котором отсутствует армирование стен, выбираем другой метод отделки;
- начинаем с внутренней поверхности, планируем такие работы на теплый сезон;
- оставляем дом без внешней отделки минимум на год;
- используем только штукатурку, подходящую по своим свойствам для нанесения на газобетон;
- обязательно производим предварительную грунтовку поверхности;
- не экономим на стекловолоконной сетке, старательно армируя каждый слой внешней штукатурки;
- для покраски используем только составы с соответствующими показателями паропроницаемости.
Резюмируя вышеизложенное, главный принцип работ по оштукатуриванию стен из газобетонных блоков можно сформулировать коротко: не спешите! Только выдержав правильные интервалы между этапами строительства и проведения отделки, обеспечив предусмотренную технологией последовательность действий и использование рекомендованных штукатурных составов, вы получите красивое и надежное покрытие, которое придаст вашему строению эстетически завершенный вид и прослужит долгие годы.
Штукатурка стен из газосиликатных блоков способствует значительному укреплению эксплуатационных характеристик основы из пористого бетона, который подвержен воздействию внешних факторов. Материал востребован в интерьерной отделке строений из газобетона, также с успехом применяется фасадная штукатурка – эффективный вариант экстерьерного оформления дома.
Принципы выбора штукатурной смеси
При обустройстве газобетонных стен применяют такие разновидности штукатурной отделки, как:
- цементно-песчаный раствор;
- гипсовая смесь;
- фасадная штукатурка для газосиликатных блоков.
Специалисты не рекомендуют штукатурить стены клеем для газобетона, так как он предназначен для формирования швов и не подходит для наружной отделки газосиликатной поверхности.
Стоит ли использовать цементно-песчаный раствор?
Как отмечают профессионалы, крайне нежелательно штукатурить газобетон цементным раствором по следующим причинам:
- Цементный отделочный материал располагает более низким коэффициентом паропроницаемости, нежели газобетон. При работе с газосиликатными стенами актуальны отделочные смеси, показатели паропроницаемости которых аналогичны с данными обрабатываемой основы или же несколько превышают их. Это необходимо для обеспечения оптимального микроклимата в доме из газобетона.
- Цементная масса предусматривает повышенное содержание влаги, а газобетон отличается высоким уровнем влагопоглощения. Это негативно отражается на качестве облицовки, так как бетон набирает прочность только при условии равномерного высыхания.
- Цементно-штукатурная субстанция не отличается высокой адгезией и плохо сцепляется с газосиликатной основой по причине большого веса раствора и наличия в составе примесей.
Добавлением извести в классический рецепт цементного раствора в пропорциях 8-10 кг на 100 кг можно повысить показатель адгезии. Поставщики строительно-отделочной продукции предлагают цементно-известковую штукатурку в виде сухой смеси, к примеру:
- КРЕПС Экстра-лайт;
- Основит Стартвэлл Т 21;
- Baumit HandPutz 0,6.
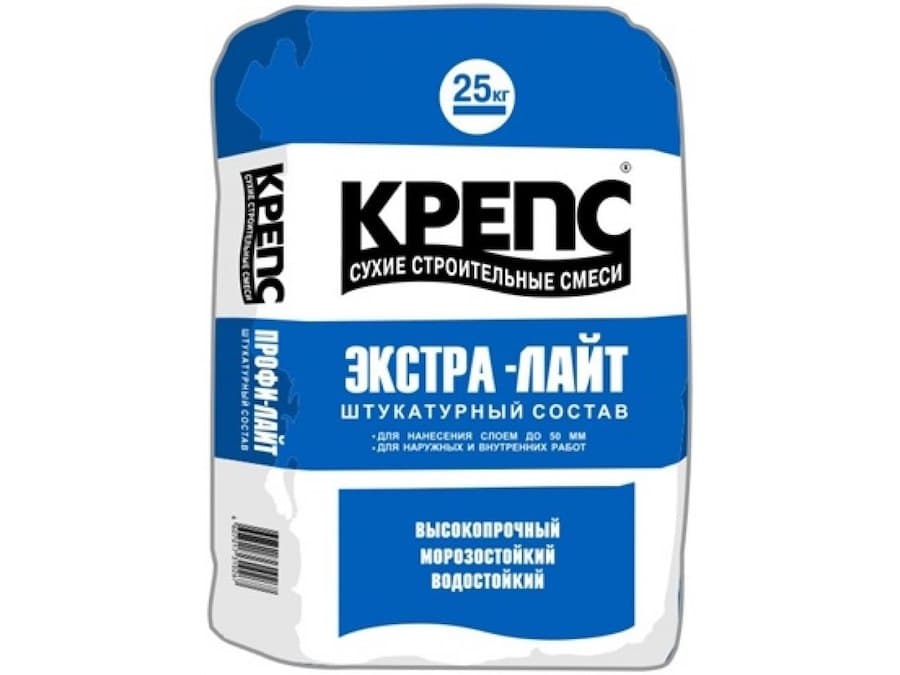
Большим минусом штукатурной отделки цементно-песчаной массой считается необходимость обязательного нанесения финишного покрытия, чтобы улучшить декоративность поверхности.
В чем преимущества и недостатки гипсовой отделочной смеси?
Ключевыми достоинствами гипсовой штукатурки по газосиликатным блокам считают высокую скорость высыхания и безусадочность материала. Примечательно, что при работе с этой облицовочной смесью отпадает необходимость нанесения финального покрытия, так как получается гладкая поверхность.
К недостаткам гипсовой облицовки относят такие моменты, как посредственная паропроницаемость материала и высокий уровень влагопоглощения. Кроме этого, отмечают вероятность образования пятен на поверхности.
Среди популярных решений выделяют следующие виды гипсовой паропроницаемой высокопластичной штукатурки по газосиликатным блокам:
- Победит VELVET G-567;
- Кнауф Ротбанд;
- Bonolit.
Несмотря на отдельные недостатки, гипсовый раствор считается неплохим вариантом облицовки газосиликатных блоков.
Фасадная штукатурка для газобетона
Эта категория отделочного материала по праву считается самым эффективным решением, так как наружная штукатурка для газосиликатных блоков располагает массой необходимых характеристик, в том числе:
- хорошей адгезией;
- показатель паропроницаемости идентичен показателю газосиликатной основы;
- отсутствием необходимости финальной облицовки.
Решая, какая штукатурка лучше для газосиликатных блоков, стоит иметь в виду, что использование фасадной штукатурной смеси позволяет значительно оптимизировать работы по отделке своими руками.
Характеристики штукатурки
Различают такие виды штукатурных основ, как минеральная, силикатная, акриловая и силиконовая.
Материал на минеральной основе относится к отделочным ресурсам демократичного сегмента. К тому же минеральную штукатурку не сложно изготовить самостоятельно. Готовые решения содержат:
- белый цемент;
- известь;
- мраморную крошку и другие наполнители;
- специальные добавки, улучшающие функциональные и декоративные качества изделия.
Продукция представлена в ограниченной цветовой гамме, но проблема легко решается способом окрашивания покрытия.
Минеральная штукатурка располагает высоким уровнем паропропускаемости и водопоглощения, выделяется инертностью к УФ излучению. Чувствительность к загрязнениям и стойкость к биологическим поражениям средняя, а показатель эластичности – низкий.
Силикатная штукатурка по газосиликатным блокам более удобна в нанесении, хотя располагает средними параметрами эластичности. Связующим звеном в составе смеси выступает жидкое стекло. Паропропускаемость силикатной отделки высокая, а уровень водопоглощения средний, все это обуславливает востребованность продукции при финишной облицовке газобетонных блоков. Силикатный состав продается в готовом виде, по стоимости изделие стоит чуть дороже сухих минеральных аналогов.
Основу силиконовой штукатурки составляют кремниево-органические полимеры. Это, пожалуй, самый лучший вариант смеси для облицовки газобетона, так как отличается высокой эластичностью и при усадке основы не покрывается трещинами. Силиконовый материал также известен следующими достоинствами:
- легко наносится;
- располагает высокими характеристиками паропроницаемости и низким уровнем водопоглощения;
- инертность к загрязнениям и биологическим воздействиям.
Силиконовая штукатурка предлагается в широком разнообразии фактур и цветов. Готовая к применению продукция реализуется в дорогом сегменте, это единственный минус в копилку отделочного материала.
Акриловая штукатурка актуальна для газобетонной поверхности лишь при наличии усиленной гидрозащиты стен и качественной вентиляции помещения. Основу облицовки составляет акриловая смола, материал отличается высокой эластичностью. При этом уровень паропроницаемости состава низкий, как и показатели влагопоглощения.
Популярные смеси для штукатурки стен из газосиликатных плит
Рынок отделочных материалов представляет большой ассортимент специальных сухих смесей и универсальных видов штукатурки для стен из газосиликата:
- Baumit Silikon Top – готовая смесь с вяжущей основой из силиконовых смол;
- Baumit Silikat Top – готовый к применению штукатурный состав на силикатной основе;
- Weber.pas Silikon – готовая к применению штукатурка на базе силиконовой эмульсии;
- Atlas DR TYNK – фасадная штукатурка для строений из газобетонных и пенобетонных блоков;
- Ш-36 Декор – состав включает в себя цементную основу с армирующими компонентами из полимеров;
- Profit Контакт МН – цементно-песчаная основа с пластификаторами для машинного нанесения;
- MCKA mix – штукатурная смесь, в состав которой входят полимерные модификаторы и кварцит;
- Дали – состав для облицовки газосиликатных, пенобетонных и полистиролбетонных стен;
- Ceresit CN 24 – специальная смесь на основе комбинированного вяжущего для выравнивания и оштукатуривания стен;
- Ceresit CT 77 – акриловая готовая смесь с минеральным наполнителем.
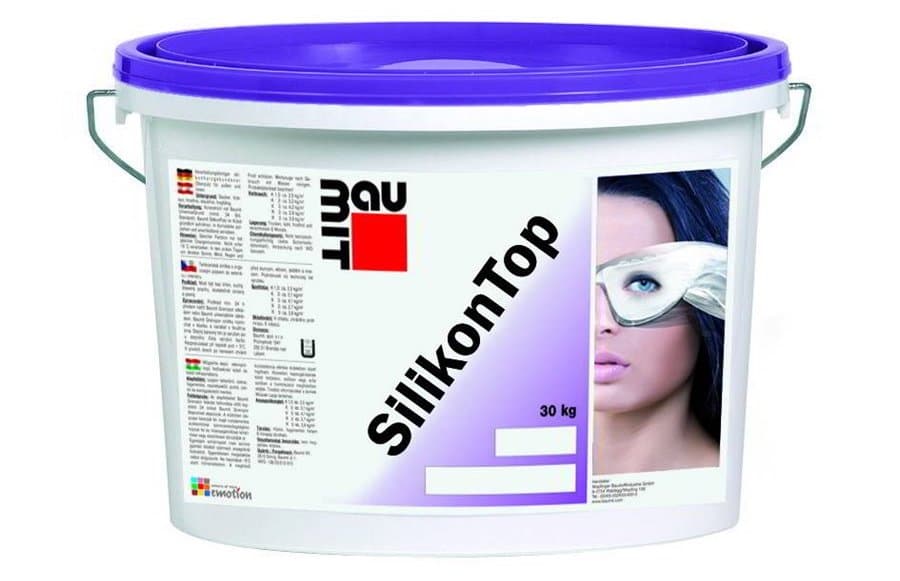
Следует помнить, что ключевыми критериями выбора штукатурного состава для газобетонных плит являются вес отделки и тип вяжущего.
Какие инструменты понадобятся для работы
Штукатурка по газосиликатным блокам выполняется при помощи следующего набора инструментов и приспособлений:
- правило – незаменимое устройство для стягивания раствора по маякам, способное обеспечить идеальное выравнивание поверхности. Начинающим мастерам рекомендуют выбрать не очень широкий вариант приспособления 2 метровой длины;
- пластиковая емкость для приготовления рабочего раствора нужного объема. Можно использовать ведро, подручную тару в виде контейнеров или резервуаров, в которых удобно разводить необходимое количество штукатурного состава;
- электродрель с миксером. Так как объемы предстоящей работы достаточно велики, для замешивания раствора стоит использовать специальный электроинструмент. Это позволяет существенно снизить временные расходы, оптимизируется скорость работ и эффективность процесса;
- специальный ковш для набрасывания рабочей смеси или кельма штукатура. В зависимости от предпочтений можно выбрать удобный вариант этого строительного инструмента, который представлен в большом разнообразии моделей;
- терка. Используется для выравнивания поверхности штукатурного слоя;
- полутер. Инструмент необходим для удаления излишков рабочей смеси с поверхности.
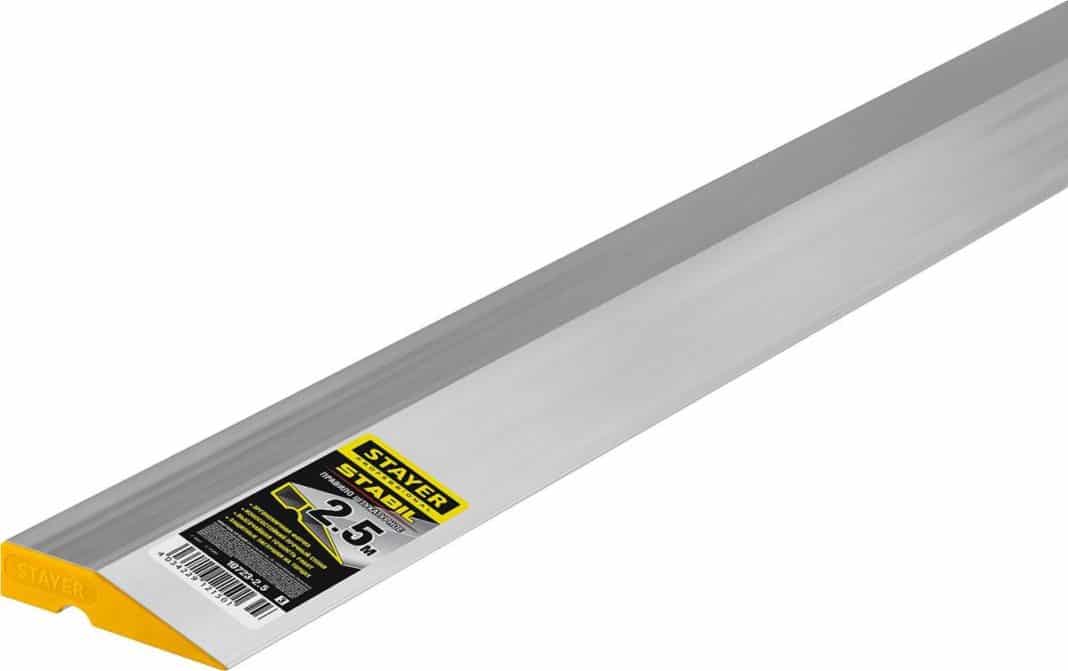
Последние два приспособления различаются только по размеру.
Рекомендации и требования к технологии процесса отделки стен
Работы по штукатурке начинают лишь после завершения всех «мокрых» этапов ремонтно-отделочных мероприятий, когда полностью высохнут поверхности как внутри помещения, так и снаружи. Максимально допустимая влажность газобетонных блоков – 27%. Оштукатуривание фасада выполняется при температуре воздуха в диапазоне от +5 и до +30 °C, при относительной влажности не более 80%.
Нельзя штукатурить при сильном ветре или в жаркую погоду, это чревато быстрым высыханием раствора, и, как следствие, отделка покрывается паутиной микротрещин и отслаивается. Точно к такому же результату приводит работа со штукатурным составом на стене под прямыми лучами солнца.
Этапы процесса отделки
Работы по облицовке дома из газосиликатных плит начинаются с внутренних плоскостей, это обеспечит качественное испарение влаги через наружные поверхности стен.
Этапы штукатурки газосиликатных блоков изнутри:
- подготовка поверхности: по возможности устраняют неровности, перед грунтовкой обрабатывают плоскость валиком, смоченным в воде. Стоит учитывать, что выбор грунтовки для газосиликатных блоков под штукатурку зависит от назначения отделываемого помещения. Так, при обустройстве стен ванной и кухни востребован состав глубокого проникновения из-за высокого коэффициента влажности пространства. При этом в «сухих» помещениях жилого назначения применяют легкие недорогие виды грунтовки;
- установка маяков. При помощи уровня регулируется ровность маяков по вертикали, а для проверки частоты применяют правило;
- нанесение первого штукатурного слоя. Работа выполняется снизу в верх по стене, используется метод набрасывания или разбрызгивания;
- после высыхания начального покрытия поэтапно наносятся еще несколько штукатурных слоев в зависимости от рекомендаций производителя используемой смеси.
В завершение проводится выравнивание покрытия и, при необходимости, финальная отделка в виде окрашивания или оклеивания обоями.
Этапы внешней отделки:
- выравнивание поверхности и грунтовка;
- нанесение тонкого слоя раствора и укладка армирующей сетки, поверх которой выполняется первое штукатурное покрытие;
- после полного высыхания начального покрытия наносят второй штукатурный слой, делая акцент на выравнивание поверхности;
- третий слой наносится после полного высыхания плоскости;
- в финале проводится затирка.
Зная особенности выбора материала и последовательность работ, не сложно выполнить штукатурку газосиликатных блоков своими руками.
Штукатурка стен из газосиликатных блоков – один из самых популярных видов отделки, однако, выполняя ее, многие самодеятельные строители забывают об особенностях ячеистых бетонов. Чтобы не выбрасывать деньги на ветер и не жалеть о напрасных усилиях, перед началом отделочных работ стоит познакомиться с теоретической частью.
Свойства блоков из газобетона
Технология изготовления блоков разработана в Швеции более века назад, однако широкое распространение этот материал получил только в наши дни. Особенностью технологии производства блоков является полная автоматизация процесса, благодаря которой конечный продукт имеет чисто белый цвет.
Блоки из газосиликатного бетона отличает прочность, хорошие звукоизолирующие свойства, малая теплопроводность. Благодаря открытой ячеистой структуре газосиликат обладает хорошей паропроницаемостью, однако из-за этой открытой структуры ячеек материал обладает и, пожалуй, единственным отрицательным качеством – гигроскопичностью, т. е. впитывает влагу.
Действующие нормативные документы запрещают выполнять из газосиликатных блоков конструкции, подверженные влиянию осадков — цоколь, карниз и парапет, а также выполнять внутреннюю кладку стен помещений с мокрым и влажным режимом эксплуатации – душевых, ванн, моечных, прачечных, бассейнов.
Благодаря теплотехническим свойствам материала стена толщиной 500 мм объемным весом блоков 600 кг/м3 обеспечивает требуемое сопротивление теплопередаче в климатической зоне средней полосы России без дополнительного утепления. Для того, чтобы в полной мере использовать положительные и минимизировать отрицательное качество, нежелательно выполнять кладку из блоков на цементно – песчаном растворе и применять в отделке штукатурку этим раствором. Штукатурные растворы для газосиликатного бетона должны иметь пористую структуру для обеспечения паропроницаемости.
Внутренняя отделка стен
Внутреннюю отделку стен из газосиликатных блоков выполняют в первую очередь. Оштукатуривание можно выполнять при температуре воздуха в помещении от +5 до +25°С. Учитывая плохую адгезию штукатурных составов к газосиликату, нанесение адгезионной грунтовки на стены обязательно.
Чем штукатурить газосиликатные блоки? Для оштукатуривания можно использовать растворы сложного состава – цементно-известковые, гипсовые, штукатурки из сухих строительных смесей, предназначенные для газосиликатных стен.
Общие правила нанесения штукатурного раствора:
- Прочность слоя через 28 дней – не менее 20 МПа.
- Адгезия к стене – 0,6 МПа.
- Слой толщиной – 3…6 мм.
- Смесь должна быть гидрофобной (отталкивать воду) и паропроницаемой (обеспечить стене возможность дышать – забирать влагу летом и отдавать ее зимой).
Необходимые инструменты:
- Емкость для разведения штукатурного состава.
- Миксер строительный или дрель со специальной насадкой.
- Мастерок или ковшик (набрасывать смесь на отделываемую поверхность).
- Правило (разравнивать смесь по поверхности).
- Полутерок (им удаляют излишки раствора).
- Терка (для выполнения затирки финишного слоя штукатурки).
- Отвес и строительный уровень (проверка геометрии стен).
- Маяки (профили, по которым производят распределение смеси по стене правилом).
ВАЖНО: профили — маяки, как правило, используются при оштукатуривании стен слоем в 3–5 см. Для выполнения тонкослойных штукатурок общей толщиной 6–15 мм на стенах из блоков высшего качества, уложенных на клее, маячки не требуются.
Последовательность работ:
- Подготовка стены – очистка от загрязнений, излишка раствора.
- Грунтование для улучшения сцепления штукатурной смеси с основанием (адгезионная грунтовка).
- Нанесение первого слоя раствора с разравниванием.
- После схватывания первого слоя наносят второй слой штукатурного состава с разравниванием и затиркой поверхности.
Через 7–10 дней или по рекомендации производителя смеси выполняется финишная отделка – шпатлевка, окраска или оклейка обоями.
Фасадные отделочные работы
Фасадные работы по газосиликатным блокам выполняют после окончания внутренних работ, не менее, чем через полгода после окончания строительства. Оштукатуривание фасадов производят в той же последовательности и тем же набором инструментов, что и внутреннюю отделку. Для выполнения более качественной отделки можно применить пластиковую щелочестойкую сетку и перфорированные профили для отделки углов и откосов.
Выполняют оштукатуривание при сухой погоде, от возможных осадков необходимо защищать стену навесом или пленкой.
Требования к штукатурным составам для фасадных работ:
- Паропроницаемость.
- Морозостойкость – циклов не менее 35.
- Высокая адгезия к материалу стен.
- Прочность.
- Эластичность.
- Устойчивость к неблагоприятным погодным условиям – осадки, ветер, солнце.
- Пожаробезопасность.
Работы выполняют как вручную, так и механизировано, с помощью штукатурной станции.
Количество приготовленного раствора должно соответствовать площади стены, которую надо обработать, пока смесь находится в рабочем состоянии. Разбавление загустевшего состава водой недопустимо.
Итоги
Штукатурные работы вполне доступны для непрофессионалов, главное – придерживаться требований производителя по температурному режиму, приготовлению смеси и нанесения состава на поверхность стен. Оштукатуривание необходимо проводить составами, предназначенными для газосиликатных смесей, экономия на качестве штукатурного состава недопустима.
можно ли шпаклевать, чем и как это делать
Стены из газобетонных блоков достаточно ровные и не нуждаются в усиленном выравнивании, поэтому шпаклевка газобетона может выполняться без предварительного оштукатуривания. В этом случае снижаются затраты на отделку, экономится время, трудовые ресурсы. Можно ли шпаклевать газобетон без штукатурки и как это сделать, расскажем ниже.
Прежде чем ответить на вопрос, можно ли шпаклевать газобетон без штукатурки, нужно разобраться, что это за материал.
Шпаклевка или шпатлевка — строительный материал в виде густого раствора, используемый для выравнивания поверхностей перед финишной отделкой. В состав шпаклевочной смеси входят: пленкообразующие соединения, заполнители, пигменты. В качестве заполнителей используется тальк, мел, барит, гипс, цемент. Назначение материала зависит от крупности заполнителя. Различают два типа шпатлевки:
- стартовая — для грубого выравнивания под обои, содержит крупный заполнитель;
- финишная — для выравнивания стен в «глянец» под подкраску, содержит мелкодисперсный заполнитель.
Стартовая шпатлевка для газобетона внутренняя и наружная имеет серый оттенок, финишная — только белый. Шпаклевка газобетонных блоков может выполняться на слой штукатурки или сразу на газоблоки. При этом перед нанесением шпатлевки по газобетону поверхность всегда предварительно грунтуется. Это необходимо для надежного сцепления материалов с поверхностью.
Шпаклевка стен из газобетона без штукатурки в соответствии со СНиП 3.04.01-87 возможна только в том случае, когда перепады уровня стены не превышают 5 мм. При наличии сколов, отверстий или неровностей глубиной более 5 мм необходимо предварительное оштукатуривание поверхности. При соблюдении технологии кладки газобетонных блоков в большинстве случаев можно делать шпатлевку стен из газобетона без штукатурки.
Достоинства способа, при котором шпаклевка стен из газобетона выполняется без штукатурки, очевидны:
- экономия на материалах;
- быстрое окончание отделочных работ;
- повышение паропроницаемости стен;
- отсутствует уменьшение полезного объема помещения.
Кроме того шпаклевка газоблока без штукатурки позволяет не привлекать к отделочным работам арендное оборудование — штукатурные станции. Большой выбор шпаклевочных составов дает возможность выбрать тот, который будет проще всего наносить, исходя из опыта и квалификации мастера, а также финансовых возможностей владельца газоблочного дома.
Однако способ шпаклевания газоблока без предварительного оштукатуривания имеет свои недостатки:
- если кладочные швы были затерты недостаточно хорошо, то через некоторое время на стене проступит сетка из блоков и швов;
- при наличии неровностей с перепадами более 3 мм потребуется наносить несколько слоев шпаклевочного материала;
- перед нанесением некоторых типов финишной отделки стена нуждается в шлифовке абразивами.
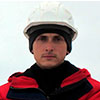
Виталий Кудряшов
строитель, начинающий автор
Обратите внимание, что если шпаклевка газоблока без штукатурки вполне возможно, то конечная отделка поверхности без выравнивания невозможна. Практически все отделочные материалы имеют плохую адгезию со штукатурными составами, поэтому шпаклевка газоблока обязательна.
Шпаклевка стен из газобетона выполняется различными материалами. Выбор шпаклевочного состава зависит от назначения — для внутренних или фасадных работ, финишного покрытия, условий применения, мастерства отделочника, бюджета. Предлагаем краткий обзор материалов, который поможет выбрать, чем шпаклевать газобетон внутри дома и снаружи.
Смесь на основе цемента универсальна, подходит для наружных и внутренних работ. Кроме цемента в состав шпатлевки по газобетону входят полимерные добавки, обеспечивающие идеальную гладкость обрабатываемой поверхности. Для наружных работ может использоваться смесь с теплоизоляционными добавками. Цементная смесь для шпаклевания газоблока продается в сухом виде (в бумажных мешках) или жидком (в пластиковых ведрах).
Технические характеристики:
- тип — стартовая и финишная;
- размер фракции — от 0.1 до 3 мм;
- максимальная толщина слоя — 3-5 мм;
- жизнеспособность раствора — до 90 минут;
- рабочая температура — от +5 до +30°C;
- время затвердевания — 28 суток.
Достоинство шпаклевки стен из газобетона без штукатурки с помощью цементной смеси — низкая цена. Наносить выравнивающий слой достаточно сложно. Про то, как шпаклевать стены из газобетона расскажем ниже.
В состав шпатлевочной смеси входит экологичный клей ПВА, обеспечивающий высокую адгезию. В качестве заполнителя используется мел или тальк. Для легкого нанесения в состав клеевой шпаклевки для газоблоков вводится олифа.
Материал отличается приемлемой ценой, простотой нанесения, отличными эксплуатационными свойствами. Технические характеристики:
- тип — стартовая и финишная;
- размер фракции — от 0.1 до 2 мм;
- максимальная толщина слоя — до 2 мм;
- жизнеспособность раствора — до 120 минут;
- рабочая температура — от +15 до +35°C;
- время затвердевания — 24 ч.
Обратите внимание, что материал на основе клея можно использовать только для внутренних работ. Поэтому, если вы не имеете достаточно опыта в отделке и ищите, чем шпаклевать стены из газобетонных блоков внутри, рекомендуем обратить внимание именно на этот вариант.
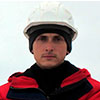
Виталий Кудряшов
строитель, начинающий автор
Еще один важный факт: клеевая смесь наноситься только 1 (!) слоем толщиной не более 2-3 мм. Более толстый слой растрескается, отделка придет в негодность. Шпаклевание газоблока клеевой смесью возможно только при наличии минимальных неровностей.
В состав шпатлевки входит гипс, который имеет грубую фракцию. Поэтому гипсовая шпаклевка стен из газобетона относится к стартовым. Материал подходит для внутренних и наружных работ для подготовки газоблочных стен под обои и другие виды декоративной отделки. Недостаток гипсовой шпаклевочной смеси заключается в необходимости обязательно выполнять шлифовку поверхности.
Технические характеристики:
- тип — стартовая;
- размер фракции — от 0.5 до 5 мм;
- максимальная толщина слоя — 1-5 мм;
- жизнеспособность раствора — 20-30 минут;
- рабочая температура — от +5 до +40°C;
- время затвердевания — от 45 минут до 2-3 часов.
Гипсовая шпаклевка газобетона внутренняя без штукатурки быстро схватывается, образуя плотный монолитный слой высокой прочности. Для нанесения материала нужен опыт работы: на разравнивание смеси у мастера есть не более 3-5 минут до начала схватывания. Поэтому, выбирая, чем шпаклевать газобетон внутри дома, учтите эту особенность и при недостатке опыта покупайте другой материал.
Содержит клей, акрилаты, пластификаторы и воду. В качестве масляной основы используется олифа. Шпаклевка газобетона таким составом возможна только внутри помещения под покраску масляной краской. Этот тип выравнивающего раствора имеет низкую адгезию к обойным клеям, акриловым краскам, винилу. Поэтому сфера применения масляной шпаклевки для газоблока ограничена. При этом масляно-клеевая смесь легко наносится, быстро высыхает. Недостатками материала считаются: высокая гигроскопичность, низкая устойчивость к механическим повреждениям.
Технические характеристики:
- тип — стартовая и финишная;
- размер фракции — от 0.1 до 2 мм;
- максимальная толщина слоя — до 2 мм;
- жизнеспособность раствора — до 1 года;
- рабочая температура — от +15 до +35°C;
- время затвердевания — до 24 часов.
Масляная шпатлевка легко разравнивается на стене, поэтому ее можно рекомендовать использовать тем, кто имеет минимальный опыт отделочных работ. При выборе этого материала нужно учесть, что шпаклевка газобетона должна выполняться при влажности воздуха не выше 85%. При высокой влажности адгезивные свойства масляного состава снижаются и выравнивающий слой ложиться неровно.
Экологически безопасный, универсальный шпаклевочный состав для наружных и внутренних работ. В затвердевшем виде полимерная шпатлевка на газоблоке имеет мелкозернистую структуру. Поверхность легко шлифуется, не дает трещин, усадок. Используется под любые виды конечной отделки. Если вы в поиске, чем шпаклевать газобетон внутри дома и снаружи, то можно с уверенность сказать, что лучше варианта не найти. Полимерная шпаклевка обладает высокой адгезией, прочностью к механическим повреждениям, климатическим факторам.
Технические характеристики:
- тип — стартовая и финишная;
- размер фракции — от 0.1 до 3 мм;
- максимальная толщина слоя — до 5 мм;
- жизнеспособность раствора — от 1 до 24 часов;
- рабочая температура — от +5 до +35°C;
- время затвердевания — до 24 ч.
Полимерная шпаклевка газоблока без штукатурки позволяет создать ровную подготовку под обои или покраску без лишних усилий. Шпатлевка по газобетону на основе полимеров наносится точно так же, как и цементная. Единственный недостаток материала — относительно высокая цена.
Предлагаем универсальный алгоритм, используя который можно выполнить шпаклевку стен из газобетона без штукатурки самостоятельно, не прибегая к помощи специалистов. Алгоритм разработан на основании СНиП 3.04.01-87 и применим для всех типов выравнивающих растворов.
От правильности подготовки газоблока зависит, насколько легко будет ложиться на поверхность шпаклевочная смесь, и насколько долго будет держаться отделка. Подготовка включает следующие действия:
- Удаление остатков кладочного раствора, старой штукатурки.
- Демонтаж гвоздей, болтов, металлических креплений.
- Удаление мусора, плесени, минеральных отложений с газоблоков.
- Заделка трещин, сколов, глубоких впадин.
- Обезжиривание поверхности растворителем.
- Нанесение грунтовки в 1-3 слоя.
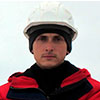
Виталий Кудряшов
строитель, начинающий автор
Грунтовка должна не просто высохнуть, а впитаться внутрь газобетонных блоков. К работам по шпаклевке газоблока после грунтования можно приступать не менее чем через 4 часа.
Перечень инструментов, нужных для шпаклевки газоблока включает:
- Электрический миксер — для размешивания смеси.
- Набор металлических шпателей размером 40-200 мм — для нанесения и разравнивания.
- Кисти, валики малярные — для нанесения грунтовки.
- Строительное правИло — для контроля ровности выравнивающего слоя.
- Шкурки или шлифовальные круги со шлифмашинкой — для окончательной шлифовки стен.
Материалы для шпаклевки стен из газобетона без штукатурки — это грунтовка и сам шпаклевочный состав. Грунтовка выбирается исходя из назначения: для наружных или внутренних работ. О типах шпаклевки и чем шпаклевать стены из газобетона внутри и снаружи мы рассказывали выше. Остается только рассчитать нужное количество материала. Расход шпаклевочной смеси указывается производителем и в среднем составляет:
- для стартовой — 1-1.5 кг на 1 м² при толщине 0.5-5 мм;
- для финишной — 0.3-0.6 кг на 1 м² при толщине 0.5-1 мм.
К полученному результату расчета нужно прибавить 10% на технологические потери.
Перед началом работ следует определить толщину слоя выравнивающего раствора на газоблок без штукатурки. Как правило, толщина выбирается равной перепадам и составляет до 15 мм. При относительно ровной стене нужно учитывать тип конечной отделки:
- под обои — не более 10-15 мм;
- под покраску — не более 10 мм.
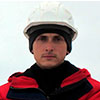
Виталий Кудряшов
строитель, начинающий автор
Обратите внимание, что указанная толщина наносится не в один слой! Максимальная толщина одного слоя составляет 5 мм, значит, шпаклевание газоблока выполняется ви2-3 слоя.
Смесь наносится большим шпателем и разравнивается в одном направлении. При разравнивании нужно следить, чтобы заполнялись все неровности и ямки на поверхности. Второй слой наносится после схватывания первого, а перед этим выполняется повторная очистка поверхности шпателем от частичек смеси из первого слоя. Перед тем, как шпаклевать стены из газобетона нужно позаботиться о хорошем освещении, чтобы видеть все неровности и устранять их до схватывания материала. Третий слой можно наносить, не дожидаясь высыхания предыдущего.
Толщина финишного слоя для газоблока без штукатурки составляет 1-3 мм. Финишная подготовка под отделку наносится точно так же, как и стартовая. Материал нужно стараться наносить максимально тонко. К покраске или оклейке обоями можно переходить после истечения срока затвердевания, указанного производителем.
Газосиликатная стеновая панель
SINOPOWER! Завод газосиликатных блоков, фасадная машина для производства бетонных блоков, автоклав реактора высокого давления!
Введение Кирпич / блок / панель из автоклавного газобетона (AAC)
Кирпич / блок / панель из автоклавного газобетона (AAC) — это легкий, многоклеточный новый строительный материал; особенности включают в себя более низкую плотность, теплоизоляцию, возможность, огнь и акустические свойства устойчивых. AAC сделан из материала кремния (кварцевый песок, или переработанного летучей золы) и материала кальция (известь, цемент), смешивания с пеной добавки (алюминиевый порошок), дозировочная, реакция между алюминием и бетоном вызывает микроскопические пузырьки водорода, чтобы из, расширение бетону примерно в пять раз его первоначального объема.Это сделано в продукт силиката с несколькими сот процессами формования, предварительно отверждения, резки, испарения и отверждения.
Внедрение производственной линии по производству автоклавного газобетона (AAC)
1) Вес продукта соответствует 500 кг / м3, 600 кг / м3 700 кг / м3 для контроля.
2) годовой объем производства 100 000-400 000 м³.
3) установить пропорцию сырья: цемент 6,5%, сырье извести 23%, флеш или песок 68%, гипс 3%, порошок алюминиевой пасты 350 г / м3.
4) расход воды и материала 0,631
5) один продукт формы 3,024M3, 3,456M3, 4,23M3
6) Время цикла разливки 5-6 минут, время цикла резки 5 минут.
7) температура жидкого раствора 38-42 градусов
8) бесшумная остановка кузова. Время составляет 1,5-2,5 час, температура 50-90 градусов, после бесшумной остановки сила тела составляет 0,15-0,18 МПа
9) Время цикла отверждения паром, входить и выходить в автоклаве около 0,5 часа, время цикла отверждения паром около 7.5 часов / 1,6Mpa, всего 8 часов
Аэробетон производит технологический процесс:
1. Хранение сырья в хранилище материалов (или хранилище) после обработки запасов, таких как известь, цемент, гипс , Песок (или летучая зола)
2. Алюминиевая пудра или алюминиевый лосьон проходят через работу с резервным материалом для использования
3. Сырье измеряют в соответствии с определенным соответствием с помощью электронного баланса, алюминиевого порошка, воды, помещенной в смеситель для алюминиевого порошка. после измерения
суспендируют жидкость для перемешивания 4.Дозируемая вода (холодная вода или горячая вода в кувшине горячей воды) измеряется электронным водным балансом
. 5. Поместите в смесители и разлейте их в определенном порядке после того, как сырье, алюминиевый порошок приостановят измерение жидкости, вылейте и введите пресс-форма после равномерного перемешивания (панель должна быть заранее помещена в пресс-форму сетчатым ломтиком арматурного стержня).
6. Чтобы заранее приподнять ее, чтобы припарковаться при определенной температуре и времени, можно ли ее транспортировать к режущему станку для подвешивания на подъемном устройстве. На 90 ° после того, как основание достигнет определенной интенсивности, рисунок рисунков обрезается
a.Основное тело опирается на боковую сторону и режет и фрезерует желоб вертикально
сначала
b. Затем перенести на вертикальный уровень, чтобы вырезать
c. Вырезать горизонтально окончательно
г. Вырежьте хороший базовый корпус, поднимите к котлу. Машина пойдет на один ярд полок, организовайте в группы, чтобы готовить пар на транспорте, чтобы повесить, чтобы ехать на машине, чтобы загрузить
7. Хорошо поднимите продукты, произведите после того, как котел отломит доску пальцами и большим пальцем отрывая доску пальцами и большим пальцем машины до пара
8.Сваи из лебедки готового продукта или вилочного погрузчика в поле готового продукта складывают контрфорс в соответствии с техническими условиями для перевозки
. Пропаривание и подъем машины и бокового борта, а также выход на следующую доску циркуляции и возвращение после этого, выгрузка готового продукта с подъемным подъемом связь рамы пресс-формы, при которой отрисовка рисунков прекращается, восстановление на 90 °, возврат к заливке смесителя снова после очистки
Основные машины из автоклавного газобетона (AAC) кирпич / блок
Оборудование будет разделено на две части: специализированное оборудование и универсальное оборудование.
Специализированное оборудование включает в себя:
1. Режущее оборудование: опрокидной кран, резак.
2. Дозирующее оборудование: электронная измерительная шкала, машина для взбивания суспензии,
бак для хранения пульпы, смеситель для пульпы.
3. Разливочное и автоклавное оборудование: смеситель алюминиевого порошка. Смеситель для заливки, пресс-форма, боковая панель
, автоклав, автоцистерна.
4. Транспортное оборудование: кран для полупродуктов, кран для конечных продуктов.
Универсальное оборудование включает в себя:
1.Оборудование под давлением сосуд: котел, автоклав.
2. Дробильное оборудование: шаровая мельница, дробилка.
3 Транспортное оборудование: кран, подъемная машина, питатель, ленточный конвейер, шламовый насос
, винтовой конвейер.
4.Enviornment Защищают оборудование: пыль для удаления
Тип емкости
ПУНКТ | SP-AAC-5 | SP-AAC-10 | SP-AAC-15 | 6 SP-AAC- SP-AAC- -AAC-30 | |
Емкость, x103m3 / год | 50 | 100 | 150 | 200 | 300 |
торт Размер, м3 | 4.2×1,2×0,6 | 4,2×1,2×0,6 | 4,2×1,5×0,6 | 4,8×1,2×0,6 | 6,0×1,2×0,6 | 600 | 800 | 900 | 1300 | 1400 |
ProductionCycle, плесень / мин | 5 | 6 | 6 | 6 | 6 |
мастерская Площадь, м2 | 3000 | 3000 | 3500 | 4000 | 5000 |
Площадь завода, м3 | 20000 | 20000 | 25000 | 30000 | 35000 |
Преимущества конструкции блока из автоклавного газобетона (AAC)
1.Звукоизоляция
Стена AAC имеет превосходный класс звукоизоляции (STC), рейтинг 44. Результат: практически звукоизоляция интерьеров
2. Тепловая изоляция
Обладает самым высоким тепловым рейтингом в отрасли… .R30! Таким образом, обеспечивает хорошо изолированы интерьер, сохраняя теплый воздух летом и холодного воздуха в winters.AAC снижает стоимость кондиционирования воздуха на 30%.
3. Устойчивость к землетрясениям
Силы землетрясения на конструкции пропорциональны весу здания, поэтому AAC демонстрирует отличную устойчивость к силам землетрясения.Регионы с высокой сейсмической активностью, как Япония используют исключительно AAC. Доказано, что оно выдерживает ветровые нагрузки тропических штормов категории 5. пространство пола между 3-5%.
5. Экономия затрат
Легкий вес AAC значительно снижает собственный вес здания, что приводит к снижению стальных (до 27%) и цементных (до 20%) конструкционных затрат.Будучи 8 раз размера глиняного кирпича, строительство ААС стенки включает в себя 1/3 суставов, таким образом, общую экономию строительного раствора до 66%.
Благодаря своему автоматическому процессу производства AAC обладает исключительной точностью размеров и гладкими поверхностями, что устраняет необходимость в трехслойных штукатурных стенах и позволяет получить окончательное 6-миллиметровое скользящее покрытие (шпаклевка / POP).
6. Огнестойкость
Лучшая в своем классе огнестойкость 4 часа. Температура плавления AAC составляет более 1600 ° С, более чем в два раза типичная температура в здании пожара 650 ° С.
7. Устойчивые к вредителям термиты ненавидят AAC
Будучи изготовленными из неорганических минералов, они не способствуют росту плесени.
8. Водяной барьер
Его структура не допускает капиллярного воздействия, что делает его непроницаемым для воды. Его вода барьерные свойства дополнительно улучшены за счет добавления на силиконовой основе добавки.
Соотношение прочности и веса, выше, чем даже у бетона M150, и намного превышает требования индийских строительных норм.
Приглашаем посетить наш завод.!
,Силикат натрия — это общее название для составного метасиликата натрия, Na2SiO3, также известного как жидкое стекло или жидкое стекло . Это доступно в водном растворе и в твердой форме и используется в цементах, пассивной противопожарной защите, огнеупорах, текстильной и лесоперерабатывающей промышленности, и автомобилях. Карбонат натрия и диоксид кремния реагируют при расплавлении с образованием силиката натрия и диоксида углерода. В этом техническом бюллетене обсуждаются лишь некоторые из его многочисленных областей применения для пользователей: керамика, изготовление металлических форм, герметизация бетона и гипса, а также адгезивы.
РЕЗЮМЕ ПРЕИМУЩЕСТВ:
● Низкая стоимость
● Негорючий
● Устойчив к температурам до 3000o F
● Без запаха и нетоксичен
● Влагостойкий
● Связывается с металлами, частицами (например, огнеупорными материалами), волокнистыми материалами (например, бумагой) , стекловолокно), стекло, керамика
● прочный и жесткий
Применение в керамике Мгновенное античное покрытие : Чистка поверхности брошенного сосуда силикатом натрия, быстрое высыхание поверхности с помощью теплового пистолета или паяльной лампы до тех пор, пока поверхность не станет липкой, а затем расширение формы изнутри может дать Кусок керамики аура мгновенной старины.Силикат натрия образует тонкую оболочку, которая при воздействии тепла быстро затвердевает на поверхности, покрывая ее) и, следовательно, до пластичного глиняного цилиндра внизу. Обычно используемый в качестве дефлокулянта для отливки слипов, при этом он быстро высыхает на ощупь с небольшим количеством тепла от паяльной лампы. На данный момент это как леденцовое яблоко, хрустящее снаружи и так) внутри. Когда форма затем расширяется под давлением изнутри, трещины на поверхности кожи увеличиваются в размере в зависимости от величины давления и расширения.Остаточный силикат натрия дает слегка остекленную поверхность, похожую на тонкую соляную глазурь. Суть процесса заключается в скорости, с которой он выполняется, так как покрытие должно оставаться твердым и не впитывать влагу от так называемой глины под ним.
Глиняный дефлоккулянт: Силикат натрия является наиболее распространенным экономичным и мощным дефлокулянтом для глинистого скольжения, поскольку он уменьшает усадку. Начальные добавления силиката натрия служат для разжижения (дефлокуляции) партии. Однако есть момент, после которого силикат натрия начинает оказывать противоположное действие, фактически делая партию более густой (флокулируя ее).Трудности усугубляются тем фактом, что силикат натрия ускоряет свою эффективность по мере приближения к точке чрезмерной дефлокуляции. Например, вы можете добавить одну унцию к партии с небольшим улучшением вязкости, но четвертое добавление отправит партию сверх лимита. Вот почему рекомендуется использовать небольшие дополнения, пока вы не знакомы с изготовлением слипов. ; Если вы добавляете силикат натрия и слип становится толще, а не тоньше, он чрезмерно дефлокулируется, и у вас есть два варианта: вы можете попытаться восстановить партию или выбросить ее.Если ваша квитанция сильно излишне дефлоккулирована, ее очень трудно исправить, и она будет стоить вам больше времени и разочарований, чем покупка новой квитанции. Если партия немного перегружена, вы можете вернуть ее, добавив больше сухого материала. Определение правильного количества будет методом проб и ошибок, но с каждым добавлением глины вы должны смешивать партию в соответствии с полностью рекомендованным _me (то есть 3 часа для партии 300 фунтов). Если вы считаете, что близки к чрезмерной дефлоккуляции, пришло время перейти от силиката натрия к диспергированию.Диспергирующие агенты, такие как дарван, могут быть добавлены после добавления максимального количества силиката натрия. Типичная формула глиняной накладки: · Глиняная смесь 100 фунтов. · карбоната бария 1/2 унции (14,75 гр.) · кальцинированной соды 1 унция (23,35 грамма) · воды 5 галлонов (19,50 литра) · жидкого силиката натрия 5 жидких унций.
Применение для изготовления металлических или литейных форм Силикат натрия используется в качестве связующего для формования форм и стержней из песка, в который заливается расплавленный металл.После добавления и смешивания с песком он вступает в реакцию с газообразным CO2 или сложными эфирами для схватывания (системы с кислотным отверждением). Как его использовать: Смешайте мелкозернистый песок (для начала попробуйте примерно 100 меш) с 3-4% по массе силиката натрия ArtMolds. Смешивание может быть выполнено в небольшом контейнере вручную для небольших работ. Большие партии могут быть смешаны в мюллер. Упакуйте обработанный песок в основную коробку, которая формирует желаемую форму. Вставьте любые провода, стержни или другие вспомогательные элементы по мере необходимости. Чтобы затвердеть ядро, подайте газ CO2 из источника низкого давления, такого как баллон с напитком.Газ можно подавать с помощью шланга и любой удобной насадки. Сопло может быть просто концом трубки или диффузором, таким как стандартная кухонная воронка. Цель состоит в том, чтобы протолкнуть газ через ядро от одного конца к другому и активировать силикат натрия, чтобы связать песок. Также практично поместить всю форму ядра в пластиковый пакет и залить его СО2, чтобы запустить ядро внутри. Ядра будут готовы к использованию сразу после того, как станут твердыми.
Герметизирующий бетон и гипсовые гипсы Бетон, обработанный жидким раствором силиката натрия ArtMolds, помогает значительно снизить пористость в большинстве каменных изделий, включая бетон, штукатурку и штукатурки.Химическая реакция происходит с избытком Ca (OH) 2 (портландит), присутствующим в бетоне, который постоянно связывает силикаты с поверхностью, делая их гораздо более износостойкими и водоотталкивающими. Обычно рекомендуется применять это лечение только после того, как начальное лечение состоялось (7 дней или около того, в зависимости от условий). Это идеальный метод для создания водоотталкивающих растворов. Нанесите тонкий слой на неокрашенную штукатурку или бетонные поверхности и дайте высохнуть. сохнуть.
Использование в качестве связующего вещества Жидкий силикат натрия ArtMolds обладает физическими и химическими свойствами, которые полезны при склеивании и нанесении покрытий.При нанесении в виде тонкого слоя на или между поверхностями других материалов, раствор силиката высыхает, образуя прочную, плотно прилегающую неорганическую связь или пленку, которая может проявлять следующие характеристики: · Низкая стоимость · Негорючий · Устойчив к температурам до 3000 ° F. · Не имеет запаха и нетоксичен. · Влагостойкий. · Связывается с металлами, частицами (например, огнеупорными материалами), волокнистыми материалами (например, бумагой, стекловолокном), стеклом, керамикой. · Прочный и жесткий. Нанесите тонкую непрерывную силикатную пленку между поверхностями для оптимальной адгезии
Непрозрачность и цвет Силикатные пленки можно сделать непрозрачными с помощью диоксида титана или алюминиевых пигментов. Наполнители, такие как глина, используются для полупрозрачных пленок. Щелочестойкие пигменты необходимы для использования в силикатных транспортных средствах. Предлагаются следующие: · белый — диоксид титана; · Красный — оксид железа без извести; · Синий — ультрамарин; · Зеленый — оксид хрома; · Черный — безмасляный технический углерод. · Желтый — охра; · Коричневый — амбер или сиенна;
Приемлемость для окружающей среды Силикаты натрия изготавливаются из песка и щелочи и по общему мнению считаются нетоксичными и экологически безвредными в пресноводных средах.Они полностью неорганические и поэтому не представляют опасности взрыва или воспламеняемости.
Срок годности При правильном хранении нераскрытые контейнеры могут быть полезны бесконечно долго. Тем не менее, мы настоятельно рекомендуем использовать продукт в течение года после даты изготовления.
Хранение Хранить в прохладном, сухом, хорошо вентилируемом месте, удаленном от окислителей, кислот, активных металлов, источников тепла или возгорания и пищевых продуктов.Убедитесь, что контейнеры имеют соответствующую маркировку, защищены от физического повреждения и запечатаны, когда они не используются. Большие складские помещения должны быть связаны и иметь соответствующие системы вентиляции.
Предупреждение о замерзании Лучше всего предотвращать замерзание растворов силиката натрия. После замораживания контейнера с силикатом натрия его иногда можно разморозить с помощью косвенного нагрева или нагрева с низкой плотностью и восстановить путем тщательного перемешивания.
ОСТОРОЖНО В ОБРАЩЕНИИ С Информация по безопасности и обращению Жидкий силикат натрия ArtMolds может вызвать раздражение или ожог кожи и глаз при контакте.Перед использованием внимательно прочитайте этикетку продукта. Рекомендуется использовать безопасные методы работы, чтобы избежать контакта с глазами или кожей и вдыхания. Следует соблюдать меры предосторожности при обращении, указанные на этикетках упаковок. Паспорта безопасности материалов доступны для всех продуктов для дальнейшего руководства.
Носить брызгозащитные очки, резиновые или ПВХ перчатки и комбинезон. При использовании в больших количествах или там, где возможно сильное загрязнение, наденьте: фартук из ПВХ и резиновые сапоги.
.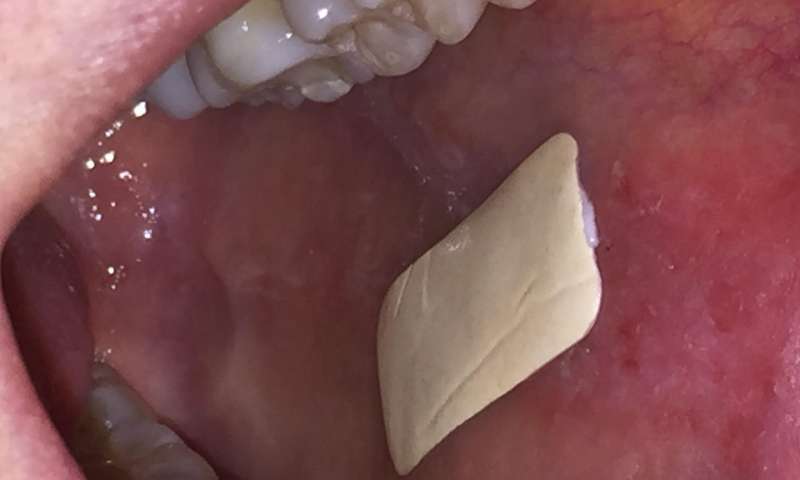
Пластырь, который прилипает к вашему рту, революционизирует лечение болезненных повторяющихся язв.
Ученые из Школы клинической стоматологии Университета Шеффилда, работающие в тесном сотрудничестве с Dermtreat A / S из Копенгагена, разработали уникальный патч с использованием специальных полимеров, способных прилипать к влажным поверхностям.
Пластырь успешно вводит стероиды непосредственно в язвы или повреждения полости рта, одновременно создавая защитный барьер вокруг пораженной области, ускоряя процесс заживления.
Новый пластырь — это революционная терапия для лечения состояний слизистой оболочки, таких как красный плоский лишай (OLP) и рецидивирующий афтозный стоматит (RAS), которые являются болезнями, вызывающими болезненные поражения и поражающими 1-2 процента населения.
До настоящего времени язвы и повреждения во рту обрабатывались с помощью кремов или полосканий для рта, которые используются во всем рту, а не нацелены на конкретную область, что делает их менее эффективными.Тем не менее, биоразлагаемый пластырь Ривелин имеет длительное время адгезии и высокую гибкость, которая соответствует поверхности внутри рта.
Доктор Крейг Мердок, читатель Школы клинической стоматологии Oral Bioscience и ведущий автор исследования, сказал: «Хронические воспалительные состояния, такие как OLP и RAS, которые вызывают эрозивные и болезненные поражения полости рта, оказывают значительное влияние на качество жизни.
«Современные методы лечения состоят из использования стероидов в форме жидкости для полоскания рта, кремов или мазей, но они часто оказываются неэффективными из-за неадекватного времени контакта лекарства с поражением.
«Пластырь действует как пластырь во рту, а это значит, что он очень эффективен при прямом нацеливании на конкретную область, а также при создании защитного барьера.
«Пациенты, которые опробовали пластырь, сочли его очень удобным для ношения, и им очень понравилась длина адгезии, которая делает его особенно эффективным и действенным».
Йенс Хансен, главный исполнительный директор Dermtreat A / S, добавил: «Сотрудничество с Университетом Шеффилда, несомненно, ускорило перевод нашей интеллектуальной собственности на клиническое использование.Наша компания очень уверена в том, что вскоре мы получим одобрение регулирующих органов на первую технологию доставки адгезивных препаратов для удовлетворения насущных клинических потребностей в оральной медицине.
«Мы с нетерпением ждем продолжения этого сотрудничества, которое будет все больше направлено на поиск новых клинических применений для слизисто-адгезивных пластырей».
Dermtreat A / S недавно получил 17,7 млн долларов от венчурной фирмы Sofinnova. Благодаря финансированию патчи перейдут во вторую фазу клинических испытаний, которые пройдут в нескольких местах как в США, так и в Великобритании, в том числе в стоматологической больнице имени Чарльза Клиффорда в Шеффилде.Кроме того, Dermtreat финансирует дальнейшие исследования в стоматологической школе для разработки следующего поколения пластырей, которые содержат другие полезные лекарства.
Результаты исследования опубликованы в журнале Биоматериалы .
Проблемы с сухостью во рту могут быть связаны с заболеванием век
Дополнительная информация: ЧАС.E. Colley et al. Доклиническая оценка новых мукоадгезивных двухслойных пластырей для локальной доставки клобетазол-17-пропионата в слизистую оболочку полости рта, Biomaterials (2018). DOI: 10.1016 / j.biomaterials.2018.06.009 Предоставлено Университет Шеффилда
Цитирование : Пластырь, который застревает во рту, может улучшить лечение заболеваний полости рта (2018 г., 25 июня) восстановлено 25 июля 2020 г. с https: // физ.орг / Новости / 2018-06-гипсовый рта лечебно-орально-conditions.html
Этот документ защищен авторским правом. Кроме честных сделок с целью частного изучения или исследования, нет Часть может быть воспроизведена без письменного разрешения. Содержание предоставлено исключительно в информационных целях.
,Теплопроводность выбранных материалов и газов
Теплопроводность — это свойство материала, которое описывает способность проводить тепло. Теплопроводность может быть определена как
«количество тепла, передаваемого через единицу толщины материала — в направлении, перпендикулярном поверхности единицы площади — из-за градиента температуры единицы в установившемся режиме»
Теплопроводность Единицами измерения являются [Вт / (м К)] в системе СИ и [БТЕ / (ч футов F)] в системе Imperial.
См. Также теплопроводность вариации с температурой и давлением , для: Воздуха, аммиака, диоксида углерода и воды
Теплопроводность для обычных материалов и изделий:
Теплопроводность — k — Вт / (м К) | ||||||||||||
---|---|---|---|---|---|---|---|---|---|---|---|---|
Материал / Вещество | Температура | |||||||||||
25 o C (77 o F) | 125 o C (257 o F) | 225 o C (437 o F) | ||||||||||
Acetals | 0.23 | |||||||||||
Ацетон | 0,16 | |||||||||||
Ацетилен (газ) | 0,018 | |||||||||||
Акрил | 0,2 | |||||||||||
Воздух, атмосфера (газ) | 0,0262 | 0,0333 | 0,0398 | |||||||||
Воздух, высота над уровнем моря 10000 м | 0,020 | |||||||||||
Агат | 10.9 | |||||||||||
Спирт | 0,17 | |||||||||||
Глинозем | 36 | 26 | ||||||||||
Алюминий | ||||||||||||
Алюминий Латунь | 121 | |||||||||||
Алюминий оксид | 30 | |||||||||||
Аммиак (газ) | 0,0249 | 0,0369 | 0,0528 | |||||||||
Сурьма | 18.5 | |||||||||||
Яблоко (влажность 85,6%) | 0,39 | |||||||||||
Аргон (газ) | 0,016 | |||||||||||
Асбестоцементная плита | 0,744 | |||||||||||
Асбест- цементные листы | 0,166 | |||||||||||
Асбестоцемент | 2,07 | |||||||||||
Асбест сыпучий | 0.15 | |||||||||||
Доска асбестовой мельницы | 0,14 | |||||||||||
Асфальт | 0,700 | |||||||||||
Древесина бальзы | 0,048 | |||||||||||
Битум | 0,182 9007 | |||||||||||
Битумные / войлочные слои | 0,5 | |||||||||||
Говядина постная (влажность 78,9%) | 0.43 — 0,48 | |||||||||||
Бензол | 0,16 | |||||||||||
Бериллий | ||||||||||||
Висмут | 8,1 | |||||||||||
Битум | 0,17 | Печь газовая 8878 | (газ) | 0,02 | ||||||||
Вес котла | 1,2 — 3,5 | |||||||||||
Бор | 25 | |||||||||||
Латунь | ||||||||||||
Бриз-блок | 0.10 — 0,20 | |||||||||||
Кирпич плотный | 1,31 | |||||||||||
Кирпич огнеупорный | 0,47 | |||||||||||
Кирпич изоляционный | 0,15 | |||||||||||
Кирпич обыкновенный обыкновенный (Строительный кирпич ) | 0,6 -1,0 | |||||||||||
Кирпичная кладка плотная | 1,6 | |||||||||||
Бром (газ) | 0.004 | |||||||||||
Бронза | ||||||||||||
Коричневая железная руда | 0,58 | |||||||||||
Сливочное масло (влажность 15%) | 0,20 | |||||||||||
Кадмий | ||||||||||||
Силикат кальция | 0,05 | |||||||||||
Углерод | 1,7 | |||||||||||
Углекислый газ (газ) | 0.0146 | |||||||||||
Окись углерода | 0,0232 | |||||||||||
Чугун | ||||||||||||
Целлюлоза, хлопок, древесная масса и регенерированные | 0,23 | |||||||||||
Ацетат целлюлозы, формованный, лист | 0,17 — 0,33 | |||||||||||
Нитрат целлюлозы, целлулоид | 0,12 — 0,21 | |||||||||||
Цемент, Портленд | 0.29 | |||||||||||
Цемент, раствор | 1,73 | |||||||||||
Керамические материалы | ||||||||||||
Мел | 0,09 | |||||||||||
Древесный уголь | 0,084 | 9008 | Хлорированный полиэфир0,13 | |||||||||
Хлор (газ) | 0,0081 | |||||||||||
Хром никель Сталь | 16.3 | |||||||||||
Хром | ||||||||||||
Оксид хрома | 0,42 | |||||||||||
Глина сухая до влажности | 0,15 — 1,8 | |||||||||||
Глина насыщенная | 0,6 — 2,5 | |||||||||||
Уголь | 0,2 | |||||||||||
Кобальт | ||||||||||||
Треска (влажность 83%) | 0.54 | |||||||||||
Кокс | 0,184 | |||||||||||
Бетон легкий | 0,1 — 0,3 | |||||||||||
Бетон средний | 0,4 — 0,7 | |||||||||||
Бетон плотный | 1,0 — 1,8 | |||||||||||
Бетон, камень | 1,7 | |||||||||||
Константин | 23.3 | |||||||||||
Медь | ||||||||||||
Кориан (керамический наполнитель) | 1,06 | |||||||||||
Пробковая доска | 0,043 | |||||||||||
Пробка с повторной грануляцией | 0,044 | |||||||||||
Пробка | 0,07 | |||||||||||
Хлопок | 0,04 | |||||||||||
Вата | 0.029 | |||||||||||
Углеродистая сталь | ||||||||||||
Вата теплоизоляционная | 0,029 | |||||||||||
мельхиор 30% | 30 | |||||||||||
Алмаз | 1000 | |||||||||||
Диатомовая земля (Sil-o-cel) | 0,06 | |||||||||||
Диатомит | 0,12 | |||||||||||
Дуралий | ||||||||||||
Земля сухая | 1.5 | |||||||||||
Эбонит | 0,17 | |||||||||||
Эмери | 11,6 | |||||||||||
Моторное масло | 0,15 | |||||||||||
Этан (газ) | 0,018 | |||||||||||
Эфир | 0,14 | |||||||||||
Этилен (газ) | 0,017 | |||||||||||
Эпоксидная смола | 0.35 | |||||||||||
Этиленгликоль | 0,25 | |||||||||||
Перья | 0,034 | |||||||||||
Войлочная изоляция | 0,04 | |||||||||||
Стекловолокно | 0,04 | 9004 изоляционная плита | 0,048 | |||||||||
Древесноволокнистая плита | 0,2 | |||||||||||
Огнеупорный кирпич 500 o C | 1.4 | |||||||||||
Фтор (газ) | 0,0254 | |||||||||||
Пеностекло | 0,045 | |||||||||||
Дихлордифторметан R-12 (газ) | 0,007 | Дан R-12 (жидкий) | 0,09 | |||||||||
Бензин | 0,15 | |||||||||||
Стекло | 1.05 | |||||||||||
Стекло, Жемчуг, сухое | 0,18 | |||||||||||
Стекло, Жемчуг, насыщенное | 0,76 | |||||||||||
Стекло, окно | 0,96 | |||||||||||
Стекло Изоляция шерсти | 0,04 | |||||||||||
Глицерин | 0,28 | |||||||||||
Золото | ||||||||||||
Гранит | 1.7 — 4.0 | |||||||||||
Графит | 168 | |||||||||||
Гравий | 0.7 | |||||||||||
Грунт или почва, очень влажная зона | 1.4 | |||||||||||
Грунт или почва, влажная площадь | 1,0 | |||||||||||
Земля или почва, сухая зона | 0,5 | |||||||||||
Земля или почва, очень сухая зона | 0.33 | |||||||||||
Гипсокартон | 0,17 | |||||||||||
Войлок | 0,05 | |||||||||||
ДСП высокой плотности | 0,15 | |||||||||||
Лиственные породы (дуб, клен ..) | 0,16 | |||||||||||
Hastelloy C | 12 | |||||||||||
Гелий (газ) | 0,142 | |||||||||||
Мед (12.Влажность 6%) | 0,5 | |||||||||||
Соляная кислота (газ) | 0,013 | |||||||||||
Водород (газ) | 0,168 | |||||||||||
Сероводород (газ) | 0,013 | |||||||||||
Лед (0 o C, 32 o F) | 2,18 | |||||||||||
Инконель | 15 | |||||||||||
Слиток железа | 47 — 58 | |||||||||||
Изоляционные материалы | 0.035 — 0,16 | |||||||||||
Йод | 0,44 | |||||||||||
Иридий | 147 | |||||||||||
Железо | ||||||||||||
Оксид железа | 0,58 | 900ok | ||||||||||
Kap изоляция | 0,034 | |||||||||||
Керосин | 0,15 | |||||||||||
Криптон (газ) | 0.0088 | |||||||||||
Свинец | ||||||||||||
Кожа сухая | 0,14 | |||||||||||
Известняк | 1,26 — 1,33 900,7 | |||||||||||
Литий | ||||||||||||
Магнезия ( 85%) | 0,07 | |||||||||||
Магнезит | 4,15 | |||||||||||
Магний | ||||||||||||
Магниевый сплав | 70 — 145 | |||||||||||
Мрамор | 2.08 — 2,94 | |||||||||||
Меркурий, жидкость | ||||||||||||
Метан (газ) | 0,030 | |||||||||||
Метанол | 0,21 | |||||||||||
Слюда | 0,71 | |||||||||||
Молоко | 0,53 | |||||||||||
Изоляционные материалы из минеральной ваты, шерстяные одеяла .. | 0,04 | |||||||||||
Молибден | ||||||||||||
Монель | ||||||||||||
Неон ( газ) | 0.046 | |||||||||||
Неопрен | 0,05 | |||||||||||
Никель | ||||||||||||
Оксид азота (газ) | 0,0238 | |||||||||||
Азот (газ) | 0,024 | |||||||||||
Закись азота (газ) | 0,0151 | |||||||||||
Нейлон 6, нейлон 6/6 | 0,25 | |||||||||||
Масло машинное смазочное SAE 50 | 0.15 | |||||||||||
Оливковое масло | 0,17 | |||||||||||
Кислород (газ) | 0,024 | |||||||||||
Палладий | 70,9 | |||||||||||
Бумага | 0.05 | 9005 | ||||||||||
Парафиновый воск | 0,25 | |||||||||||
Торф | 0,08 | |||||||||||
Перлит, атмосферное давление | 0.031 | |||||||||||
Перлит, вакуум | 0.00137 | |||||||||||
Фенольные литые смолы | 0,15 | |||||||||||
Фенолформальдегидные формовочные смеси | 0,13 — 0,25 | Фосфорбронза | 110 | |||||||||
Пинчбек | 159 | |||||||||||
Шаг | 0.13 | |||||||||||
Каменный уголь | 0,24 | |||||||||||
Гипс легкий | 0,2 | |||||||||||
Гипс, металлическая рейка | 0,47 | |||||||||||
Гипс, песок | 0,71 | |||||||||||
Гипс, деревянная планка | 0,28 | |||||||||||
Пластилин | 0,65 — 0,8 | |||||||||||
Пенопласт (изоляционные материалы) | 0.03 | |||||||||||
Платина | ||||||||||||
Плутоний | ||||||||||||
Фанера | 0,13 | |||||||||||
Поликарбонат | 0,19 | Полиэфир | 9005 Полиэстер | |||||||||
Полиэтилен низкой плотности, ПЭЛ | 0,33 | |||||||||||
Полиэтилен высокой плотности, PEH | 0.42 — 0,51 | |||||||||||
Натуральный каучук полиизопреновый | 0,13 | |||||||||||
Твердый каучук полиизопреновый | 0,16 | |||||||||||
Полиметилметакрилат | 0,17 — 0,25 | |||||||||||
Полипропилен 0,1 — 0,22 | ||||||||||||
Полистирол, пенополистирол | 0,03 | |||||||||||
Полистирол | 0.043 | |||||||||||
Пенополиуретан | 0,03 | |||||||||||
Фарфор | 1,5 | |||||||||||
Калий | 1 | |||||||||||
Картофель, сырая мякоть | 0,55 | Пропан (газ) | 0,015 | |||||||||
Политетрафторэтилен (ПТФЭ) | 0,25 | |||||||||||
Поливинилхлорид, ПВХ | 0.19 | |||||||||||
Пирекс | 1,005 | |||||||||||
Кварц минеральный | 3 | |||||||||||
Радон (газ) | 0,0033 | |||||||||||
Красный металл | ||||||||||||
Рений | ||||||||||||
Родий | ||||||||||||
Камень твердый | 2 — 7 | |||||||||||
Камень пористый вулканический (туф) | 0.5 — 2,5 | |||||||||||
Изоляция из каменной ваты | 0,045 | |||||||||||
Канифоль | 0,32 | |||||||||||
Каучук сотовый | 0,045 | |||||||||||
Каучук натуральный | 0,13 | |||||||||||
Рубидий | ||||||||||||
Лосось (влажность 73%) | 0.50 | |||||||||||
Песок сухой | 0,15 — 0,25 | |||||||||||
Песок влажный | 0,25 — 2 | |||||||||||
Песок насыщенный | 2 — 4 | |||||||||||
Песчаник | 1.7 | |||||||||||
Опилки | 0,08 | |||||||||||
Селен | ||||||||||||
Овечья шерсть | 0.039 | |||||||||||
Кремнезем аэрогельный | 0,02 | |||||||||||
Силиконовая литая смола | 0,15 — 0,32 | |||||||||||
Карбид кремния | 120 | |||||||||||
Силиконовое масло | 0,1 | |||||||||||
Серебро | ||||||||||||
Шлаковая вата | 0,042 | |||||||||||
Шифер | 2.01 | |||||||||||
Снег (температура <0 o C) | 0,05 — 0,25 | |||||||||||
Натрий | ||||||||||||
Хвойные породы (ель, сосна ..) | 0,12 | |||||||||||
Грунт, глина | 1,1 | |||||||||||
Грунт с органическими веществами | 0,15 — 2 | |||||||||||
Грунт насыщенный | 0.6 — 4 | |||||||||||
Припой 50-50 | 50 | |||||||||||
Сажа | 0,07 | |||||||||||
Пар насыщенный | 0,0184 | |||||||||||
Пар, низкое давление | 0,0188 | |||||||||||
Стеатит | 2 | |||||||||||
Сталь, углерод | ||||||||||||
Сталь нержавеющая | ||||||||||||
0.09 | ||||||||||||
Пенополистирол | 0,033 | |||||||||||
Диоксид серы (газ) | 0,0086 | |||||||||||
Сера, кристалл | 0,2 | |||||||||||
Сахар | 0,087 — 0,22 | |||||||||||
Тантал | ||||||||||||
Смола | 0,19 | |||||||||||
Теллур | 4.9 | |||||||||||
Торий | ||||||||||||
Пиломатериалы, ольха | 0,17 | |||||||||||
Пиломатериалы, ясень | 0,16 | |||||||||||
Пиломатериалы, береза | 0,14 | 9004 | ||||||||||
Пиломатериалы из лиственницы | 0,12 | |||||||||||
Пиломатериалы из клена | 0,16 | |||||||||||
Пиломатериалы из дуба | 0.17 | |||||||||||
Пиломатериалы 9004 | 0,14 | |||||||||||
Пиломатериалы | 0,19 | |||||||||||
Пиломатериалы красного бука | 0,14 | |||||||||||
Пиломатериалы красного сосны | 0,15 | |||||||||||
Пиломатериалы из белой сосны | 0,15 | |||||||||||
Пиломатериалы из грецкого ореха | 0,15 | |||||||||||
Олово | ||||||||||||
Титан | Вольфрам | |||||||||||
Уран | ||||||||||||
Уретановая пена | 0.021 | |||||||||||
Вакуум | 0 | |||||||||||
гранулы вермикулита | 0,065 | |||||||||||
виниловый эфир | 900 900 | |||||||||||
9005 | ||||||||||||
9005 | 9005 | 9005 | 9005 | 9005 | 9005 | 9005 | 900 0 9009 | 900 0 9009 | 900 0 9009 | 0,606 | ||
Вода, пар (пар) | 0,0267 | 0,0359 | ||||||||||
Мука пшеничная | 0.45 | |||||||||||
Белый металл | 35 — 70 | |||||||||||
Дерево через зерно, белая сосна | 0,12 | |||||||||||
Дерево через зерно, бальза | 0,055 | |||||||||||
Дерево поперек зерна, желтая сосна, древесина | 0,147 | |||||||||||
Дерево, дуб | 0,17 | |||||||||||
Шерсть, войлок | 0.07 | |||||||||||
Древесная вата, сляб 9009 | 0,1 — 0,15 | |||||||||||
Ксенон (газ) | 0,0051 | |||||||||||
Цинк |
Пример — Проводящая теплопередача через Алюминиевый горшок или горшок из нержавеющей стали
Проводящий теплообмен через стенку резервуара можно рассчитать как
q = (к / с) A dT (1)
или альтернативно
q / A = (к / с) dT
, где
q = теплообмен (Вт, БТЕ / ч)
A = площадь поверхности (м 2 , фут 2 )
q / A = теплопередача на единицу площади (Вт / м 2 , БТЕ / (h ft 2 ))
90 007 k = теплопроводность (Вт / мК, БТЕ / (ч футов ° F) )
dT = t 1 — t 2 = разность температур ( o C, o F)
s = толщина стенки (м, футы)
Калькулятор кондуктивного теплопередачи
k = теплопроводность (Вт / мК, БТЕ / (ч футов F) )
s = толщина стенки (м, футы)
A = площадь поверхности (м 2 , футы 2 )
dT = t 1 — t 2 = разность температур ( o C, o F)
Примечание! — что общая теплопередача через поверхность определяется «общим коэффициентом теплопередачи », который в дополнение к проводящей теплопередаче зависит от
Кондуктивная теплопередача через алюминиевую стенку резервуара толщиной 2 мм — разность температур 80 o C
Теплопроводность для алюминия составляет 215 Вт / (м К) (из таблицы выше).Кондуктивный теплообмен на единицу площади может быть рассчитан как
q / A = [(215 Вт / (м К)) / (2 10 -3 м)] (80 o C)
= 8600000 (Вт / м 2 )
= 8600 (кВт / м 2 )
Проводящая теплопередача через стенку из нержавеющей стали толщиной 2 мм — перепад температур 80 o C
Теплопроводность для нержавеющей стали составляет 17 Вт / (м К) (из таблицы выше).Кондуктивный теплообмен на единицу площади можно рассчитать как
q / A = [(17 Вт / (м К)) / (2 10 -3 м) ] (80 o C)
= 680000 (Вт / м 2 )
= 680 (кВт / м 2 )
.