Клинкер и керамогранит: в чем отличие
В последнее время клинкером стали называть практически любую фасадную керамику. Даже в профессиональных кругах можно услышать, что клинкером, дескать, облицована столичная гостиница «Юбилейная», или что клинкер начала производить «Березакерамика». В действительности же в обоих случаях речь о керамограните. Поскольку клинкер значительно качественнее и дороже керамогранита, мы расскажем, в чем разница между двумя этими материалами.
Клинкерная плитка — уникальный по своим свойствам продукт со сложным, трудоемким и, соответственно, затратным процессом производства. Для клинкерной плитки используются особые сорта тугоплавких глин, добываемые преимущественно в карьерах северных районов Европы. Такая глина не имеет примесей извести, что исключает появление высолов и потерю цвета.
Часто продавцы, желая выдать керамогранит за клинкер, оперируют понятиями высокая температура обжига (1000–1300°), низкое водопоглощение (4–7 %), хорошая морозостойкость (50 циклов). Но это отнюдь не означает, что перед вами клинкер! Все эти параметры характерны как для качественного керамогранита, так и для клинкера.
Основное отличие этих двух материалов в самом процессе производства. Помимо особого очень качественного сырья (которым вряд ли могли разжиться на «Березакерамике») при изготовлении клинкера используется технология экструзии. Глиняная масса выдавливается из экструдера, а затем больше суток спекается в длинной (до 100 м) печи при температуре свыше 1300°. Именно благодаря такой технологии в плитке остаются капилляры, делающие клинкер паропроницаемым. И это его основное достоинство! Остальная же облицовочная керамика изготавливается методом сухого прессования, в результате которого в структуре материала появляются пустоты, способные накапливать влагу.
Печь для обжига клинкера
Один из признаков, по которым можно отличить клинкер — продольные полосы на оборотной стороне, они возникают в результате выдавливания массы из экструдера, у керамогранита будут клетки — следы от формы.
При облицовке клинкером, благодаря его паропроницаемости, можно не устраивать вентфасад: плитка клеится сразу на основание (керамогранит этого себе «позволить» не может).
Кроме того, пористая обратная сторона хорошо впитывает клеящий состав, что позволяет клинкеру практически намертво сцепиться с основанием. А вот у керамогранита обратная сторона имеет плотную, гладкую, частично остекленевшую поверхность. Сцепление такой плитки с клеями и растворами невелико и при температурных нагрузках плитка может отколоться.
Качественный клинкер устойчив практически к любым химическим и механическим воздействиям, УФ-излучению, он не бьется, не трескается, выдерживает не менее 25 лет эксплуатации (заметьте, не циклов!), кроме того, он значительно менее скользкий, чем керамогранит.
«Платой» за подобные уникальные свойства можно назвать ограниченную линейку размеров. Дело в том, что технология мокрого формования (экструзии) очень чувствительна к малейшим нарушениям — плитку попросту скручивает при сушке. Даже у именитых заводов может отбраковываться и уходить на вторичную переработку до половины продукции (одна из причин дороговизны клинкера). Максимальный размер, представленный на отечественном рынке, 400×800 мм. Причем, чем больше формат и чем сильнее форма плитки будет отличаеться от квадратной, тем дороже она обойдется. Узкая длинная плитка и вовсе встречается у единичных производителей (например, немецкого STROEHER ).
Основной потребитель клинкера в Беларуси — владельцы частных домов и небольших производств. Наши заводы пока не могут позволить себе, подобно российскому Микояновскому мясокомбинату, выкладывать немецким клинкером целые цеха.
Цена клинкера зависит от производителя, польский дешевле немецкого. В любом случае речь идет о стоимости в 1,5–3 раза превышающей стоимость керамогранита. Отсюда вывод: для облицовки жилого помещения вполне подойдет керамогранит, он прекрасно выдержит все нагрузки, поэтому не стоит переплачивать за клинкер. Но для улицы либо любой другой агрессивной среды более прочного и долговечного материала, чем клинкер, вы не найдете.
Автор: Екатерина Кулабухова, Stroyka.by. Фото: STROEHER
Плитка на Ступени: Керамогранит или Клинкерная Плитка
Сегодня для облицовки открытых террас, фасадов, полов чаще всего выбирают керамогранит или клинкерную плитку. Оба эти материалы выгодно отличаются многочисленными преимуществами, они при активной эксплуатации способны сохранять свои первоначальные характеристики на протяжении десятилетий. Но все же что лучше клинкерная плитка или керамогранит? Чтобы правильно дать ответ важно внимательно изучить особенности и преимущества каждого материала в отдельности.
Керамогранит или клинкер, что выбрать?
Итак, сразу отметим, что при условии если укладка керамогранита будет выполнена с учетом всех требований и технологий, то этот материал даже в экстремальных условиях способен выдерживать любые перепады температур, негативное воздействие химических веществ и большие нагрузки.
Основные отличия материалов заключаются в используемых при производстве технологиях и расходных материалах. Так, клинкерную плитку производят из тугоплавкой глины без примесей извести. Благодаря чистоте используемого сырья на плитке после длительной эксплуатации не появляются белые пятна, а также полностью исключена вероятность изменения цветового оттенка.
Если будет принято решение сделать ступени из керамогранита, то важно знать, что при его производстве могут применяться различные сорта огнеупорной глины с примесями красящих пигментов, шпата, кварцевого песка, других компонентов. Производится керамогранит с применением технологии сухого прессования под высоким давлением с последующим обжигом при температуре 1250 градусов.
Керамогранит сегодня пользуется особым спросом, он широко используется как при внутренней, так и при внешней отделке. Его популярность объясняется повышенной устойчивостью к нагрузкам, высокой температурной устойчивостью, а также устойчивостью к биологическому и химическому воздействию.
Сравнительный анализ керамогранита и клинкерной плитки
Если вам нужно плитка на ступени, и вы выбираете между этими двумя материалами, то важно знать, что их производство выполняется по схожим технологиям, поэтому материалы имеют много общего, но и различия также имеются.
- Оба варианта выгодно отличаются высокой прочностью, они способны выдерживать большие нагрузки, а также имеют хорошие показатели морозоустойчивости.
- На обратной стороне клинкерной плитки имеется особый профиль, наличие которого обеспечивает отличное сцепление с рабочей поверхностью, у керамогранита он отсутствует.
- Что касается эстетической стороны, то более эффектно выглядит керамогранит, однако сегодня многие производители предлагают клинкер, который не уступает по красоте керамограниту, на его поверхности может быть нанесено различное цветовое оформление.
Индивидуальные особенности керамогранита и клинкерной плитки
Особенностью клинкера можно отметить отсутствие определенного номера, она не калибруется и не имеет конкретного тона. Имеет клинкерная плитка натуральный природный оттенок, придающий материалу эффект старины. По краям имеются едва заметные неровности.
Преимуществом и особенностью керамогранита является повышенные характеристики прочности, твердости, износоустойчивости. Этот материал не боится резких перепадов температуры, стоек перед природными воздействиями и химически активными веществами. Именно благодаря этим преимуществам, часто можно встретить ступени из керамогранита для лестниц, но все же этот материал не рекомендован для использования при отделке ступеней под открытым небом, поскольку его поверхность очень скользкая.
Оба рассматриваемые варианта не требовательны в уходе, они способны надежно служить многие годы вне зависимости от эксплуатационных условий. При выборе следует учитывать определенные требования. Так, наличие шероховатой поверхности, которая имеется на клинкерной плитке, повышает антискользящие свойства, а значит, передвижение по такой плитке будет намного безопаснее.
И в заключение отметим, что вне зависимости от того какая плитка для ступеней крыльца будет выбрана доверять ее укладку следует только опытному мастеру, который все сделает грамотно и с учетом всех технологий и требований.
Предыдущая запись Комплексные системы изоляции в строительных конструкциях Следующая запись Монтаж цокольного сайдингаПохожие статьи
Комментарии
Клинкер и керамогранит: в чём разница?
Слово
По версии словаря «Российская архитектура» (1995 г.в.) клинкером называют марку высокопрочного кирпича для мощения дорог и настилки полов в промышленных зданиях. Пользуясь доверчивостью покупателей, недобросовестные продавцы очень часто апеллируют к этому понятию, стремясь повысить интерес клиентов к собственной продукции. Неизменно одно – за клинкер пытаются выдать самые разные строительные материалы, приписывая им уникальные показатели морозостойкости, экологической чистоты и особой прочности (до М1000).
Между тем, клинкер сегодня – это определённый стандарт глины, из которой в процессе сложнейшего сертифицированного немецким законодательством производства, изготавливаются такие строительные материалы как облицовочный кирпич, фасадная плитка под кирпич, напольная и террасная плитка, а также ступени высочайшего качества.
Такое качество материал приобретает благодаря входящим в его состав избранным — особым тугоплавким – глинам. Сырьё для клинкерных материалов добывают в карьерах между Англией и Голландией. Этот слой глины, вышедший на поверхность во время ледникового периода не имеет примесей извести. И именно поэтому поверхность изготовленного из нее кирпича со временем не теряет цвет и на его поверхности не образуются «высолы» и белесые пятна.
Помимо сырья стандарт определяет условия и процесс производства. Оговоримся сразу, керамические изделия, произведенные в процессе «сухого» прессования – не являются клинкером. В специальных формах под гигантским прессом глиняная пыль прессуется в почти сухом зернистом состоянии (содержание влаги – не более 4-5%), а затем обжигается также при температурах 1000-1200°. Именно так производят керамогранит – не менее эффектный и износостойкий облицовочный материал, однако, демонстрирующий совсем другие свойства. Водопоглощение керамогранита очень низкое, однако, к примеру, в отношение паропроницаемости он полностью непрозрачен, в отличие от клинкера. При сухой прессовке в структуре материала возникают неупорядоченные частицы с большими пустотами, которые долго накапливают воду, а значит, разрушают саму плитку при низких температурах.
Как отличить экструдированную керамику от керамики, созданной по технологии сухого прессования?
Именно по штамповочной сетке, имеющейся на обратной стороне любой керамической плитки, созданной методом «сухого» прессования можно отличить керамическое изделие, изготовленное по методу сухого прессования, от клинкера. У клинкерной плитки с обратной стороны – продольные полосы.
Клинкерный материал производится только методом экструзии, или влажной формовки. По аналогии с тем, как это происходит при производстве лапши, сырье «выдавливается» из большого отсека через сопла нужной формы будущего профиля. При этом в массе до сих пор находится около 15% влаги. Затем масса разрезается под определенный формат, отправляется в сушку и на длительный, более 36 часов, обжиг в туннельной печи длиной свыше 100 метров при высочайшей температуре около 1300 градусов до полного спекания, однако, без остекловывания поверхности. Такой стандарт производства, предполагающий использование определенного материала и условий технического процесса, позволяет создавать высокоплотный мелкопористый, но однородный – без больших пустот и каверн – материал. Однородная структура с капиллярными каналами позволяет быстро и беспрепятственно выводить проникшую влагу на поверхность плитки в виде водяного пара.
Именно структура и обеспечивает высокие эксплуатационные характеристики клинкера. А изделия из него делает удивительно паропроницаемыми, морозостойкими, износостойкими и невосприимчивыми к воздействию агрессивной, в том числе и химической, среды. Низкое водопоглощение характеризует все как глазурованые, так и неглазурованный виды клинкерных изделий – у ведущих немецких производителей, таких как Feldhaus klinker, коэффициент составляет менее 2%. Именно низкое водопоглощение позволяет использовать клинкер как для мощения улиц, так и для отделки фасадов домов и внутренних помещений, с обычной и влажной средой.
Различные технологии производства керамических изделий определяют свойства крепления такого материала к поверхности. Так, обратная сторона прессованной плитки имеет очень плотную, гладкую, частично даже «остекленевшую» поверхность. Она допускает лишь незначительное включение вспомогательных веществ и элементов для небольшого же сцепления с клеями растворами. При обусловленных температурных нагрузках такая плитка достаточно легко откалывается. Учитывая низкую паропроницаемость керамогранита, именно эта особенность данного облицовочного материала приводит к тому, что керамику, изготовленную методом сухого прессования, не рекомендуется клеить прямо на стены зданий без создания вентилируемого фасада.
Оборотная сторона экструдированной керамики, наоборот, — фактурная и шероховатая. Клеевые кристаллы проникают в открытые поры обратной стороны такой плитки, что обеспечивает большую площадь сцепления, а значит – оптимальную сцепку.
Какую керамику выбрать? Самое главное — разделить продукцию на группы товара, основываясь на их отличиях.
ЭКСТРУДИРОВАННАЯ КЕРАМИКА | КЕРАМИКА ПО ТЕХНОЛОГИИ СУХОГО ПРЕССОВАНИЯ |
Например, пустотелый кирпич или плоская экструдированная керамика приобретают свою форму, выталкивая пластичные компоненты вместе с остаточной влагой около 15%, проходя по замкнутой конвеерной ленте через особое контурное сопло / насадку. Данная технология называется экструзия (выдавливание). Norm: DIN EN 14411, Gr. A1 and A2 (formerly DIN EN 121 and DIN EN 186, part 1) |
Например, керамический природный камень или мелкопористый керамический природный камень прессуется отдельно в формах под гигантским прессом в почти сухом зернистом состоянии с остаточным количеством влаги около 4-5% Norm: DIN EN 14411, Gr. Bla and Blb (formerly DIN EN 176) |
Как отличить настоящий клинкер от экструдированного керамогранита
В салонах по продаже клинкера, керамогранита и керамической плитки можно увидеть на демонстрационных стендах «батареи» ступеней: натуральных цветов, глазурованных и покрашенных в разные рисунки и цвета на любой вкус с любыми фактурами от совсем нескользящих до антискользящих R13. А вот в действительности, настоящего «клинкера» там практически нет. А где же настоящий клинкер спросите Вы ? Давайте разбираться вместе!Сегодня «клинкером» называют напольную плитку и ступени (фронтальные, угловые) для облицовки крыльца и ступеней то есть, преимущественно для экстерьерной отделки домов, зон мангала, барбекю, лестниц.
Клинкерные ступени и напольная плитка – это материал который производится исключительно из сортов тугоплавких глин. В составе «рецепта» настоящего клинкера только тугоплавкая глина и ничего другого кроме нее в рецепте нет. Обязательным составом рецепта настоящего клинкера является «шамот» — это по сути тот же самый клинкер, который уже прошел обжиг в туннельной печи, но после этого его дробят на специальном оборудовании и добавляют в массу глины до формовки. Шамот необходим для «отощения массы» – т.е. снижения пластичности, он улучшает сушильные характеристики, снижает огневую усадку, облегчает режим обжига (режим нагрева и режим охлаждения), не меняет химический состав шихты (сырья). Кроме того, применение в шихте шамота, важно с точки зрения охраны окружающей среды и создания безотходной технологии производства. Процент шамота, в зависимости от рецептов, может составлять от 5% до 15%. Месторождения тугоплавких глин есть в Европе и России.
Клинкер производится методом ВЕРТИКАЛЬНОЙ экструзии (выдавливания) – такой метод позволяет делать ступень с литым капиносом т.е. носик ступени составляет единое целое с плиткой. Такое изделие прослужит долгие годы и не сломается. При формовании, из экструдера выдавливаются заготовки, соединенные между собой техническими перемычками (ребрами жесткости). Это дает возможность за одну формовку производить больше материала, кроме того – это необходимо для обеспечения устойчивости материала на конвейерной ленте и при последующих этапах работы с ним.
Далее, заготовки по конвейеру направляются на нарезку под определенный размер (режет как правило специальная струна) и после этого материал поступает в сушильные камеры, там заготовки сушатся до 40 часов при температуре от 90 до 98 градусов. После предварительной сушки, заготовки по конвейерной ленте поступают на глазуровку и покраску (если необходимо). Далее, заготовки роботизированными механизмами расставляются специальным образом на вагон в 2-3-4 ряда в высоту и проходят обжиг на вагоне в туннельной печи длинной 100 и более метров при температуре от 1100 до 1300 градусов на протяжении 70-80 часов (3 суток). После того, как ступени и плитка прошли обжиг в туннельной печи – они «разделяются» друг от друга на специальном оборудовании, при этом удаляются технические перемычки (ребра жесткости). Таким образом, две соединенных вместе ступени или плитки отделяются друг от друга и получаются два отдельных элемента. Далее следует упаковка в коробки и на паллеты. После чего материал отправляется покупателям.
Экструдированные керамогранитные ступени и напольная плитка – это материал который производится методом ГОРИЗОНТАЛЬНОЙ экструзии (не путать с методом сухого прессования). ГОРИЗОНТАЛЬНАЯ формовка необходима для того, чтобы уменьшить высоту изделия на конвейерной ленте (чтобы изделия могли поместиться в узкую камеру обжига роликовой печи). В составе «рецепта» экструдированного керамогранита есть в обязательном порядке полевой шпат (это измельченная горная порода), кварцевый песок (могут добавлять а могут и нет) каолиновые глины и различные добавки (пластификаторы, красители). Как правило, «полевой шпат» составляет от 30 до 50% состава рецепта, остальные 50% это кварцевый песок и каолиновые глины (не тугоплавкие!!!).
Полевой шпат производят горно-обогатительные комбинаты в Европе и России. Именно он является основой любого экструдированного керамогранита, и именно от него сам керамогранит и получил свое название «Керамический гранит»: а полевой шпат, это по сути и есть измельченный в порошок гранит, горная порода. Керамогранит может производится методом сухого прессования (на прессе) или методом горизонтальной экструзии (выдавливания) – такой метод изобрели относительно недавно, и он позволяет делать ступень с «литым капиносом» т.е. носик ступени составляет единое целое с плиткой, так же, как и у настоящего клинкера. Технология производства экструдированного керамогранита следующая: Сначала подготавливается масса — смешиваются все ингредиенты рецепта (полевой шпат, кварцевый песок, каолин, пластификаторы, красители и т.д.), далее увлажненная керамогранитная масса попадает в экструдер из которого выдавливается горизонтально.
Ступень с литым капиносом выдавливается на специальной подложке, которая соединена со ступенью техническими перемычками (ребрами жесткости) — это придает ступени ровную поверхность для транспортирования по конвейеру, глазуровке и покраске), а напольная плитка выдавливается горизонтально сразу на конвейерную ленту (без подложки, там нет технических перемычек). Далее, происходит обрезка ступеней и плитки под нужный размер специальным резаком (прямо на конвейерной ленте). После этого, заготовки проходят короткий предварительный обжиг или сушку от 30 минут до нескольких часов в сушильной камере (горячий воздух для нее забирается из основной роликовой печи для обжига), далее происходит глазурование и покраска, после чего, заготовки отправляются по конвейеру в роликовую печь (ступени и плитка транспортируются в самой роликовой печи по крутящимся роликам (отсюда и ее название) – где они проходят окончательный обжиг при температуре до 1300 градусов на протяжении 2-3 часов (в зависимости от рецепта массы, обжиг может составлять до 10 часов и более, но как правило он длиться гораздо меньше).
После этого, ступень отделяется от подложки соединенными техническими перемычками (ребрами жесткости), их разъединяют специальные молотки, а просто плитка сразу проходит далее на упаковку т.к. она не соединена с подложкой, а транспортируется по конвейеру в виде готового изделия. Далее изделия упаковываются в коробки на паллеты и отправляются покупателям.
Это вкратце о методе производства настоящего клинкера и экструдированного керамогранита. А теперь давайте разбираться, как это выглядит в жизни и как отличить настоящий клинкер от экструдированного керамогранита. В настоящее время визуально отличить экструдированный керамогранит от настоящего клинкера сложно даже специалисту, не то что обычному покупателю.
Напольная плитка из Клинкера и Экструдированного керамогранита
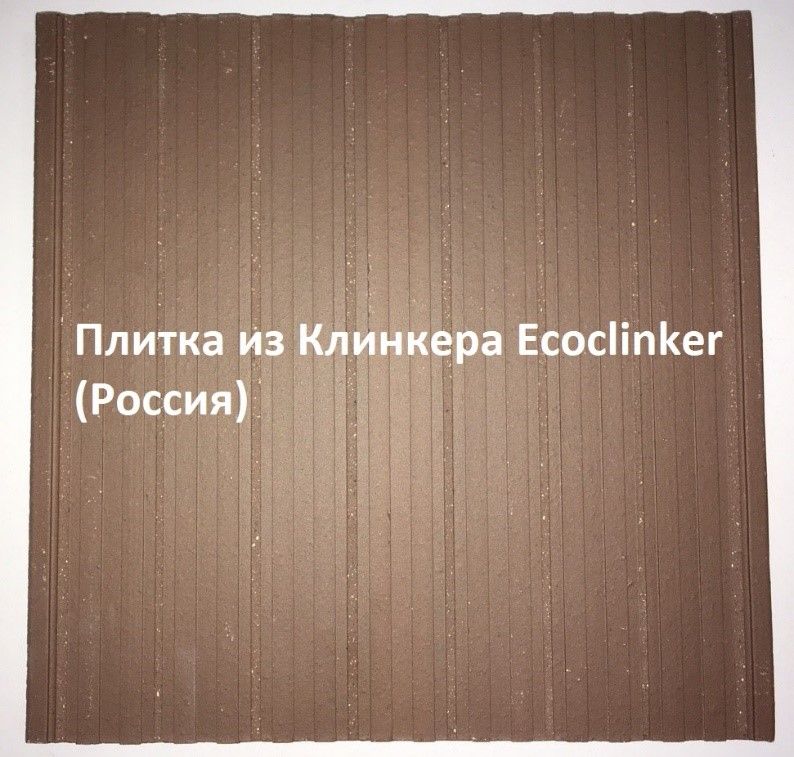
Ступени из клинкера и Экструдированного керамогранита
Ступени из клинкера и экструдированного керамогранита: имеют идентичную монтажную (обратную) поверхность. Имеются «отломы» – места где были технические перемычки, соединявшие клинкерные ступени друг с другом или где керамогранитная ступень соединялась с подложкой. Отличить их можно только по следующим параметрам: На месте отлома ребер жесткости «технических перемычек» у настоящей клинкерной ступени и клинкерной плитки выступают частицы «шамота» мелкой фракции белого или темного цветов. В экструдированном керамограните шамота нет.
Керамогранитная ступень, как правило серого цвета (обесцвеченная масса, цвет светлый или цвет цемента-бетона, но некоторые заводы добавляют красители, которые красят керамогранитную массу в темные цвета для того чтобы снизить контраст покрашенной лицевой поверхности и обратной стороны «монтажной поверхности, в некоторых случаях используют полевой шпат или каолин другого цвета, чтобы «затемнить» заготовку). Настоящий клинкер может иметь несколько цветовых вариаций (полная масса коричневая, желтая, кирпичного цвета, как правило это 5-7 натуральных цветов + оттенки или флэш-обжиг) Клинкер — толщина ступеней 12-16 мм. Клинкер — толщина напольной плитки варьируется от 12 до 30 мм. Толщина клинкерной напольной плитки и ступеней никогда не бывает тоньше 12 мм.
В то же время, толщина экструдированной керамогранитной ступени не более 8-10 мм, толщина экструдированной керамогранитной плитки 6-8 мм, очень редко 9 мм. Толщины более 9 мм не бывает. Обычно тонкие изделия из клинкера – это фасадная плитка, которую нельзя использовать в качестве напольной плитки. В этой статье мы ее не рассматриваем.
Напольная плитка из Клинкера и Экструдированного керамогранита: а вот тут отличить легко. Отличия очень заметны. Клинкерная плитка имеет такие же «отломы» перемычек (от ребер жесткости) как и у ступени т.к. экструдер выдавливает настоящий клинкер (плитку) соединенными друг с дружкой при помощи технических перемычек т.е. в одном блоке две ступени или две плитки (см фото выше). А потом, они отделяются друг друга на специальном оборудовании – в результате чего и у ступени и у плитки есть характерные места «отломов технических перемычек» на обратной стороне (монтажной поверхности).
А вот у экструдированной керамогранитной плитки таких отломов от перемычек НЕТ т.к. выдавливание керамогранитной плитки из экструдера идет в одну линию и сразу на конвейер. В 100% случаев экструдированный керамогранит (ступени и плитку) в обязательном порядке глазуруют и красят на специальном покрасочном оборудовании (цифровая печать-покраска или с помощью ротоколора). Вы никогда не встретите ступени из «неглазурованного и некрашенного» экструдированного керамогранита J т.к. цвет некрашенного керамогранита – это цвет обычного бетона или цемента, т.е. он светлый и бесцветный, именно по этой причине ЕГО ВСЕГДА глазуруют и красят т.к. мало какой покупатель захочет покупать себе домой ступени и плитку цвета бетона по цене в десятки раз дороже бетона J А вот настоящий клинкер бывает натуральный неглазурованный и не крашенный (цвет достигается путем смешения друг с другом тугоплавких глин разных сортов) и смотрится он великолепно и очень дорого. Отличаются так же и технические характеристики клинкера и экструдированного керамогранита:
Клинкер: водопоглощение до от 3% до 6%, паропроницаем (можно использовать на стенах домов без вентилируемых фасадов и клеить клинкер напрямую к зданию) Клинкер на много лучше держит ударные нагрузки чем керамогранит. Случаи сколов не заметны т.к. поверхность снаружи и внутри — одного цвета. Отлично подходит для входных групп домов (зоны ступеней, площадки для парковки а/м, крыльцо, дорожки и т.д.) т.к. именно там происходит чистка снега и уборка при помощи «специализированных инструментов в виде лома и лопаты J» и все это сопровождается ударными нагрузками т.к. лед и снег счищают с крыльца отнюдь не при помощи мягкой швабры или пылесоса J
Экструдированный керамогранит: водопоглощение от 0,5 до 3%, Не паропроницаем (по этому использовать экструдированный керамогранит на стенах домов можно ТОЛЬКО на системах с вентилируемыми фасадами). За счет того, что экструдированный керамогранит в процессе обжига в роликовой печи «остекловывается» и не имеет в своем составе тугоплавких глин – он более хрупкий чем настоящий клинкер. Очень боится ударных нагрузок (лопатой, ломом, падения на них любых предметов, особенно металлических).
Весь экструдированный керамогранит глазурован и покрашен, а значит, в лучшем случае что произойдет – это отколется кусок глазуровки и краски (пострадает эстетический внешний вид, оголится внутренняя часть плитки цвета бетона или цемента) а в худшем – плитка или ступень просто треснут и разобьются. При монтаже необходимо использовать не только специальный уличный клей для керамогранита, но и специальным образом подготовленное армированное основание!! т.к. адгезия к клею у экструдированного керамогранита очень плохая (необходимы специализированные клея которые на молекулярном уровне при помощи химической реакции соединят бетонное основание с керамогранитом).
Вы можете сами провести данный эксперимент. Он показывает, что есть настоящий клинкер, а что есть экструдированный керамогранит……Для этого достаточно расположить рядом интересующие Вас ступени и плитку и по очереди кидать на них с одинаковой высоты любой предмет, можно начинать с высоты 50 см (шарик от подшипника, столовый нож тупым закругленным концом «тыльником», все что найдете под рукой…).
Производители:
Настоящий клинкер производят в Германии, Испании, Польше и России. Отличный по качеству настоящий клинкер делают Немецкие заводы Stroher, Interbau, ABC. Хороший клинкер делают Испанские заводы: Gres de Aragon, Gresmanc, Gres de Breda. В Польше клинкер методом вертикальной экструзии делает только завод King Klinker (ступени и плитка таких Польских заводов как Paradiz, Opocno, Tubadzin и т.д. — не имеют ничего общего с клинкером, материал этих заводов делается методом сухого прессования с последующим обжигом в роликовой печи, состав рецептов неизвестен, но это не керамогранит и не клинкер). В России, единственный завод, который производит клинкерные ступени и напольную плитку это Ecoclinker.
Экструдированный керамогранит производят Stroher, Interbau, Gres de Aragon, Exagres и многие другие заводы Испании и Германии. Практически все заводы переориентировали свои производства на выпуск этой продукции, т.к. эта технология дешевле в себестоимости и производительность по сравнению с клинкерным производством выше от 20 до 40 раз. Представьте себе, что за одинаковый промежуток времени можно произвести 1000 м2 клинкера или 30000 м2 экструдированного керамогранита !! Что заводу выгоднее делать….? J В России пока не производят керамогранит методом горизонтальной экструзии. У нас делают керамогранит методом сухого прессования – такая технология для производства напольной плитки гораздо лучше, чем методом экструзии (т.к. пресс под высоким давлением гораздо качественнее и плотнее делает заготовку) но методом сухого прессования невозможно сделать фронтальную ступень с «литым капиносом», по этому, все ступени отечественных керамогранитных плиточных заводов (Керама Марацци, Эстима, Италон, и т.д.) делаются с клееными капиносами или производятся путем нарезки «насечек» на обычной плитке или они и вовсе не имеют в своем ассортименте фронтальных ступеней, а продают только напольную или настенную плитку.
Клинкер или керамогранит что лучше
Итог: Если материал отформован методом вертикальной экструзии-высушен в сушильных камерах и обожжен в туннельной печи – это КЛИНКЕР. Если материал отформован методом горизонтальной экструзии-обожжен в роликовой печи – это НЕ КЛИНКЕР. Настоящий клинкер невозможно обжечь в роликовой печи – а экструдированную керамогранитную массу невозможно обжечь в туннельной печи.
Итак, подведем итог: если вы выбираете себе материал для облицовки крыльца, ступеней, площадки под автомобиль, зоны мангала или барбекю, то вам в равной степени неплохо подойдут оба вида рассматриваемого нами материала. Но настоящий клинкер, в любом случае, будет иметь преимущество как более прочный, практичный и более долговечный материал.
Экструдированный керамогранит порадует своих покупателей обилием всевозможных рисунков и расцветок. Радовать правда будет не долго, т.к. при неаккуратном использовании он склонен к разрушению глазуровки и покраски и в конечном итоге потерей эстетики и внешнего вида с последующим ремонтом или замены на настоящий клинкер!
Статья предоставлена производителем клинкерной продукции Экоклинкер (Россия).
Керамогранит или клинкер 🌟 Заходите ✔
Сегодня одним из наиболее популярных материалов, используемых для облицовки фасадов зданий, открытых террас, полов и даже садовых дорожек является керамогранит или клинкер. Главной особенностью данного строительного и отделочного материала является его способность при активном использовании простоять около столетия и при этом не расстаться со своими эстетическими свойствами. Правильная укладка керамогранита даже в экстремальных условиях позволяет выдержать вес более тонны и любые перепады температур, а также негативные химические воздействия.
Особо популярен клинкер стал не только благодаря своим техническим свойствам, но и благодаря своему внешнему виду, его эстетическим качествам. В связи с этим производители керамического гранита стали выпускать материалы разнообразнейших стилистических видов и направлений. Однако, несмотря на простор выбора, упор был сделан на определенные стилистические группы – «под старину», хай-тек, классика, минимализм, кантри и «под дерево».
Процесс изготовления керамогранита схож с процессом появления на свет настоящего природного камня, однако происходит он в ускоренном виде. В связи с этим клинкер является более приемлемой по стоимости альтернативой натуральному камню и в то же время отличается высокими техническими свойствами.
При производстве ненатурального камня используется высококачественная смесь из глин двух сортов, в которую добавляют кварц, полевой шпат и натуральные красители. Эта смесь прессуется под высоким давлением, после чего сушится, обжигается в специальной печи при высоких температурах. В итоге и получается особо прочный, непористый монолит. Клинкер получается из глин высокого качества пластичных сортов при помощи продавливания через специальную форму (экструзии), а порой также методом прессования.
Данный стройматериал был известен еще со времен Древнего Рима, когда мостовые выкладывались из обожженного кирпича, который отличался особой прочностью. Однако клинкерный кирпич в современном его понимании был изобретен и нашел применение только лишь в конце 19-го столетия в Нидерландах. Изначально этот материал использовался только лишь для мощения дорог – такие дороги были особо прочными и долговечными. В качестве подтверждения прочности клинкера можно привести немало примеров, взять даже перекресток Итальянской и Ланжероновской улиц в Одессе, которые покрыты ярко-желтым керамическим гранитом – с той поры, как был уложен первый камень прошло более полутора столетий, а брусчатка на этих улицах выглядит так, будто бы ее уложили только на прошлой неделе.
На сегодняшний день керамогранит широко используется и для внешней отделки зданий, и даже для внутренней. Благодаря тому, что этот материал является особо прочным, отличается высоким показателем температурной устойчивости, а также устойчивым к химическим и биологическим воздействиям, ему удалось заслужить признание во всем мире.
Виды керамогранита
Керамогранит бывает глазурованным и неглазурованным. При изготовлении неглазурованного клинкера используется исключительно натуральное сырье, что и позволяет ему сохранить яркие цвета на протяжении всего эксплуатационного периода. Зачастую его применяют при наружной отделке.
Глазурованный керамогранит отличается от своего неглазурованного «брата» наличием специального покрытия, которое покрывает сформированную плитку двумя слоями. При однократном обжиге данное покрытие (его и называют глазурь) прекрасно спекается с основой из керамики. В результате получается материал, представленный в разнообразной цветовой гамме, который в добавок ко всему обладает всеми свойствами керамического гранита. Зачастую глазурованный клинкер используется для оформления интерьеров.
По своей форме керамогранит может быть представлен не только плоскими плитками и кирпичиками, но и разнообразными геометрическими фигурами, благодаря методу экструзии, который позволяет реализовать самые смелые дизайнерские решения с плавными переходами горизонтальной плоскости в вертикальную, не прибегая к самостоятельному вырезанию деталей необходимой формы из готового материала.
Керамический гранит используется в разных областях строительства. К примеру, им полностью облицовывают бассейны, прекрасно смотрится облицовка цоколя клинкером, водостоки, ступени и многие другие конструктивные элемента. На сегодняшний день рынок предлагает нам различные декоративные элементы из клинкера – это и наружные и внутренние уголки, различные декоры, канты, сангвины, поручни, молдинги, раковины для ванных комнаты из керамогранита и прочие элементы.
Укладка керамогранита и уход за ним
Чаще всего клинкерную плитку укладывают на водостойкий и морозостойкий плиточный клей, для того чтобы как можно лучше сохранить свойства клинкера. Во время укладки керамогранита применяется быстросхватывающаяся затирка, что несколько усложняет укладку плитки, потому как очень легко испачкать шероховатую поверхность клинкера. Специалисты советуют при укладке клинкерной плитки, дабы сохранить ее чистоту, вдоль швов проклеить ее специальным строительным скотчем, а уже после затирания швов с легкостью его удалить. К тому же, можно покрыть плитку слоем специальной пропитки, либо лака.
Для того, чтобы поддерживать керамогранит в первоначальном состоянии, нет необходимости в каком-либо специальном уходе – для этого достаточно промыть плитки любым моющим средством.
Дата публикации: 08.02.2014 года
Автор: Сергей Ярцев
Чем отличается клинкер и керамогранита?
Совсем недавно мы рассказывали об отличиях керамогранита от керамической плитки, а сегодня не менее важная тема! Чем же отличается клинкерная плитка от керамогранита? Итак, ответ читайте далее.
На самом деле у материалов есть определенные сходства. Например, и клинкер и керамогранит изготавливаются по очень похожим технологиям, практически из одних и тех же компонентов. Разница в пропорциях этих компонентов, смесях глины и добавляемых компонентах.
И клинкер и керамогранит могут применятся для уличных работ. Оба этих материала морозоустойчивы и достаточно крепки, изнашиваются мало и прослужат долго. Но есть и другие, весьма интересные отличия.
Шероховатость поверхности
Клинкер имеет шероховатую поверхность, тогда как керамогранит – гладкую. К тому же у клинкера на этой шероховатой поверхности нет швов. Из этого вытекает самый главный вывод – клинкер можно использовать для создания нескользких дорожек и ступенек. Обувь будет скользить намного меньше и меньше риск упасть.
«По ту сторону» плитки
«Лицевой» поверхностью дело не ограничивается. Клинкер имеет особый профиль, расположенный на оборотной стороне. Благодаря этому клинкерная плитка имеет более хорошее сцепление с другими материалами.
Ступени будут крепче
Подмечено многими строителями, что ступени, облицованные клинкером, крепче, чем те, что облицованы керамогранитом. Виновата в этом толщина материала: керамогранит тоньше и легче, а клинкер – толще и тяжелее.
Если вес имеет значение
А вот с транспортировкой клинкера уже не так все просто – он тяжелее, чем керамогранит. Перевозка на дальние расстояния выйдет дороже.
Внешний вид
Может керамогранит и не имеет шероховатой поверхности, но считается, что выглядит он очень эффектно. Благодаря обилию цветов и расцветок можно реализовать многие смелые дизайнерские решения.
Правда это утверждение можно оспорить — клинкер уже не сильно уступает внешне, да и можно купить клинкерную плитку с очень оригинальными узорами.
Купить клинкерную плитку и керамогранит Вы всегда сможете в Торговой Сети «Сибирь-Керамика». В Вашим услугам наши продавцы-консультанты, которые помогут подобрать цвет, размер, подсчитать нужное количество, оформят доставку по городу.
Клинкер или Экструдированный Керамогранит — в чем отличие ?
Сегодня «клинкером» называют все подряд… и напольную плитку и ступени (фронтальные, угловые) для облицовки крыльца, фасадную плитку и другие материалы преимущественно для экстерьерной отделки домов, зон мангала, барбекю, лестниц и т.д. А в действительности, настоящего «клинкера» там практически нет, вместо клинкера продается «экструдированный керамогранит» который имеет принципиальные отличия от клинкера. А где же настоящий клинкер спросите Вы?
В салонах по продаже клинкера, керамогранита и керамической плитки можно увидеть на демонстрационных стендах «батареи» ступеней: натуральных цветов, глазурованных и покрашенных в разные рисунки и цвета на любой вкус с любыми фактурами от умеренно нескользящих до антискользящих R13.
Клинкерные ступени и напольная плитка – это материал который производится исключительно из сортов тугоплавких глин. В составе «рецепта» настоящего клинкера только тугоплавкая глина и ничего другого кроме нее в рецепте нет и именно тугоплавкая глина делает клинкер одним из самых прочных и износоустойчивых материалов. Обязательным составом рецепта настоящего клинкера является «шамот» — это по сути тот же самый клинкер, который уже прошел обжиг в туннельной печи, но после этого его дробят на специальном оборудовании и добавляют в массу глины до формовки. Шамот необходим для «отощения массы» – т.е. снижения пластичности, он улучшает сушильные характеристики, снижает огневую усадку, облегчает режим обжига (режим нагрева и режим охлаждения), не меняет химический состав шихты (сырья). Кроме того, применение в шихте шамота, важно с точки зрения охраны окружающей среды и создания безотходной технологии производства. Процент шамота, в зависимости от рецептов, может составлять от 5% до 15%. Месторождения тугоплавких глин есть в Европе и России. Клинкер производится методом ВЕРТИКАЛЬНОЙ экструзии (выдавливания) – такой метод позволяет делать ступень с литым капиносом, т.е. носик ступени составляет единое целое с плиткой. Такое изделие прослужит долгие годы и не сломается. При формовании, из экструдера выдавливаются заготовки, соединенные между собой техническими перемычками (ребрами жесткости). Это дает возможность за одну формовку производить больше материала, кроме того – это необходимо для обеспечения устойчивости материала на конвейерной ленте и при последующих этапах работы с ним. Далее, заготовки по конвейеру направляются на нарезку под определенный размер (режет как правило специальная струна) и после этого материал поступает в сушильные камеры, там заготовки сушатся до 40 часов при температуре от 90 до 98 градусов. После предварительной сушки, заготовки по конвейерной ленте поступают на глазуровку и покраску (если необходимо). Далее, заготовки роботизированными механизмами расставляются специальным образом на вагон в 2-3-4 ряда в высоту и проходят длительный обжиг на вагоне в туннельной печи длинной 100 и более метров при температуре от 1100 до 1300 градусов на протяжении 70-80 часов (3 суток). После того, как ступени и плитка прошли обжиг в туннельной печи – они «разделяются» друг от друга на специальном оборудовании, при этом удаляются технические перемычки (ребра жесткости). Таким образом, две соединенных вместе ступени или плитки отделяются друг от друга и получаются два отдельных элемента. Далее следует упаковка в коробки и на паллеты. После чего материал отправляется покупателям.
Вот небольшой фильм как делают настоящий клинкер на заводе Ecoclinker (Россия). Обратите внимание: Вертикальная экструзия (т.е. плитка формуется вертикально и перемещается по конвейеру вертикально), туннельная печь, обжиг на вагоне.
Экструдированные Керамогранитные ступени и напольная плитка – это материал который производится методом ГОРИЗОНТАЛЬНОЙ экструзии (не путать с методом сухого прессования). ГОРИЗОНТАЛЬНАЯ формовка необходима для того, чтобы уменьшить высоту изделия на конвейерной ленте (чтобы изделия могли поместиться в узкую камеру обжига роликовой печи) и для того, чтобы заготовки было удобно глазуровать и красить. В составе «рецепта» экструдированного керамогранита есть в обязательном порядке «полевой шпат» (это измельченная горная порода), кварцевый песок (могут добавлять а могут и нет) каолиновые глины и различные добавки (пластификаторы, красители). Как правило, «полевой шпат» составляет от 30 до 50% состава рецепта, остальные 50% это кварцевый песок и разновидности каолиновых глин (не тугоплавких!!!). Полевой шпат производят горно-обогатительные комбинаты в Европе и России. Именно он является основой любого экструдированного керамогранита, и именно от него сам керамогранит и получил свое название «Керамический гранит»: а полевой шпат, это по сути и есть измельченный в порошок гранит, горная порода. Керамогранит может производится методом сухого прессования (на прессе) или методом горизонтальной экструзии (выдавливания) – такой метод изобрели относительно недавно, и он позволяет делать ступень с «литым капиносом» т.е. носик ступени составляет единое целое с плиткой, так же, как и у настоящего клинкера. Технология производства экструдированного керамогранита следующая: Сначала подготавливается масса — смешиваются все ингредиенты рецепта (полевой шпат, кварцевый песок, каолин, пластификаторы, красители и т.д.), далее увлажненная керамогранитная масса попадает в экструдер из которого выдавливается горизонтально (см фото). Ступень с литым капиносом выдавливается на специальной подложке, которая соединена со ступенью техническими перемычками (ребрами жесткости) — это придает ступени ровную горизонтальную поверхность для транспортирования по конвейеру, глазуровке и покраске, а напольная плитка выдавливается горизонтально сразу на конвейерную ленту (без подложки, там нет технических перемычек). Далее, происходит обрезка ступеней и плитки под нужный размер специальным резаком (прямо на конвейерной ленте). После этого, заготовки проходят короткий предварительный обжиг или сушку от 30 минут до нескольких часов в сушильной камере (горячий воздух для нее забирается из основной роликовой печи для обжига), далее происходит глазурование и покраска, после чего, заготовки отправляются по конвейеру в роликовую печь (ступени и плитка транспортируются в самой роликовой печи по крутящимся роликам (отсюда и ее название) – где они проходят окончательный скоростной обжиг при температуре до 1300 градусов на протяжении 2-3 часов (в зависимости от рецепта массы, обжиг может составлять от 1 часа до 3 часов и более, но как правило он длиться гораздо меньше, именно в скоростном обжиге весь смысл роликовой печи). После этого, ступень отделяется от подложки соединенными техническими перемычками (ребрами жесткости), их разъединяют специальные молотки, а просто плитка сразу проходит далее на упаковку т.к. она не соединена с подложкой, а транспортируется по конвейеру в виде готового изделия. Далее изделия упаковываются в коробки на паллеты и отправляются покупателям.
Это вкратце о методе производства настоящего клинкера и экструдированного керамогранита. А теперь давайте разбираться, как это выглядит в жизни и как отличить настоящий клинкер от экструдированного керамогранита. В настоящее время визуально отличить экструдированный керамогранит от настоящего клинкера сложно даже специалисту, не то что обычному покупателю….
Напольная плитка из Клинкера и Экструдированного керамогранита:
Именно по «отломам технических перемычек» на НАПОЛЬНОЙ ПЛИТКЕ можно отличить настоящий клинкер от экструдированного керамогранита.
Ступени из клинкера и экструдированного керамогранита: имеют идентичную монтажную (обратную) поверхность. Имеются «отломы» – места где были технические перемычки, соединявшие клинкерные ступени друг с другом или где керамогранитная ступень соединялась с подложкой. Отличить их можно только по следующим параметрам: На месте отлома ребер жесткости «технических перемычек» у настоящей клинкерной ступени и клинкерной плитки выступают частицы «шамота» мелкой фракции белого или темного цветов. В экструдированном керамограните шамота нет. Керамогранитная ступень, как правило серого цвета (обесцвеченная масса, цвет светлый или цвет цемента-бетона, но некоторые заводы добавляют красители, которые красят керамогранитную массу в темные цвета для того чтобы снизить контраст покрашенной лицевой поверхности и обратной стороны «монтажной поверхности, в некоторых случаях используют полевой шпат или каолин другого цвета, чтобы «затемнить» заготовку). Настоящий клинкер может иметь несколько цветовых вариаций (полная масса коричневая, желтая, кирпичного цвета, как правило это 5-7 натуральных цветов + оттенки или флэш-обжиг) Клинкер — толщина ступеней 12-16 мм. Клинкер — толщина напольной плитки варьируется от 12 до 30 мм. Толщина клинкерной напольной плитки и ступеней никогда не бывает тоньше 12 мм. В то же время, толщина экструдированной керамогранитной ступени не более 8-10 мм, толщина экструдированной керамогранитной плитки 6-8 мм, очень редко 9 мм. Толщины более 9 мм не бывает. Обычно тонкие изделия из клинкера – это фасадная плитка, которую нельзя использовать в качестве напольной плитки. В этой статье мы ее не рассматриваем.
Напольная плитка из Клинкера и Экструдированного керамогранита: а вот тут отличить легко. Отличия очень заметны. Клинкерная плитка имеет такие же «отломы» перемычек (от ребер жесткости) как и у ступени т.к. экструдер выдавливает настоящий клинкер (плитку) соединенными друг с дружкой при помощи технических перемычек т.е. в одном блоке две ступени или две плитки (см фото выше). А потом, они отделяются друг друга на специальном оборудовании – в результате чего и у ступени и у плитки есть характерные места «отломов технических перемычек» на обратной стороне (монтажной поверхности). А вот у экструдированной керамогранитной плитки таких отломов от перемычек НЕТ т.к. выдавливание керамогранитной плитки из экструдера идет в одну линию и сразу на конвейер. В 100% случаев экструдированный керамогранит (ступени и плитку) в обязательном порядке глазуруют и красят на специальном покрасочном оборудовании (цифровая печать-покраска или с помощью ротоколора). Вы никогда не встретите ступени из «неглазурованного и некрашенного» экструдированного керамогранита 🙂 т.к. цвет некрашенного керамогранита – это цвет обычного бетона или цемента, т.е. он светлый и бесцветный, именно по этой причине ЕГО ВСЕГДА глазуруют и красят т.к. мало какой покупатель захочет покупать себе домой ступени и плитку цвета бетона по цене в десятки раз дороже бетона 🙂 А вот настоящий клинкер бывает натуральный неглазурованный и не крашенный (цвет достигается путем смешения друг с другом тугоплавких глин разных сортов) и смотрится он великолепно и очень дорого. Отличаются так же и технические характеристики клинкера и экструдированного керамогранита:
Клинкер: водопоглощение от 3% до 6%, паропроницаем (можно использовать на стенах домов без вентилируемых фасадов и клеить клинкер напрямую к зданию). Клинкер кислотоустойчив, его можно использовать в промышленных целях (химические и пищевые производства с агрессивной средой). Настоящий клинкер (в отличие от экструдированного керамогранита) менее требователен к подготовке основания и к используемым в процессе укладки клеям и затиркам. Клинкер на много лучше держит ударные нагрузки чем керамогранит. Сколы и выбоины не заметны на нём т.к. лицевая поверхность, монтажная поверхность и само «тело» ступени или плитки и снаружи и внутри — одного цвета, это одна глиняная масса без красителей и различных добавок. Клинкер превосходно подходит для входных групп домов (зоны ступеней, площадки для парковки а/м, крыльцо, дорожки и т.д.) т.к. именно там происходит чистка снега и уборка при помощи специализированных инструментов типа лопаты 🙂 и все это сопровождается ударными нагрузками т.к. лед и снег и грязь счищают с крыльца отнюдь не при помощи мягкой швабры или пылесоса 🙂
Экструдированный керамогранит: водопоглощение от 0,5 до 3%, Не паропроницаем т.к. произведен методом скоростного обжига в роликовой печи, покрыт глазурью и краской и не имеет в своем составе тугоплавких глин (по этому использовать экструдированный керамогранит на стенах домов можно ТОЛЬКО на системах с вентилируемыми фасадами). НЕ кислотоустойчив. За счет того, что экструдированный керамогранит в процессе скоростного обжига в роликовой печи «остекловывается» и не имеет в своем составе тугоплавких глин как клинкер – он более хрупкий чем настоящий клинкер. Очень боится ударных нагрузок (лопатой, острыми и тяжелыми предметами, падений любых предметов, особенно металлических). Весь экструдированный керамогранит глазурован и покрашен, а значит, в лучшем случае что произойдет – это отколется кусок глазуровки и краски (пострадает эстетический внешний вид, оголится внутренняя часть плитки цвета бетона или цемента) а в худшем – плитка или ступень просто треснут и разобьются. При монтаже необходимо использовать не только дорогой специальный уличный клей и затирки для керамогранита, но и специальным образом подготовленное армированное основание с пластичной гидроизоляцией!! т.к. адгезия к клею у экструдированного керамогранита очень плохая, а значит необходимы специализированные клея которые на молекулярном уровне при помощи химической реакции соединят бетонное основание с керамогранитом.
Видео с этого теста:
Вы можете сами провести данный эксперимент. Он показывает, как отличить настоящий клинкер от экструдированного керамогранита……Для этого достаточно расположить рядом интересующие Вас ступени и плитку и по очереди кидать на них с одинаковой высоты любой предмет весом 60-70 грамм, можно начинать с высоты 50 см, шарик от подшипника, столовый нож тупым закругленным концом «тыльником», все что найдете под рукой…
Производители:
Настоящий клинкер производят в Германии, Испании, Польше и России. Немецкие заводы: Stroher, Interbau, ABC, ADW и др. Испанские заводы: Gres de Aragon, Gresmanc, Gres de Breda и др. В Польше клинкер методом вертикальной экструзии делает только завод King Klinker, ступени и плитка таких Польских заводов как Paradyz, Opoczno, Tubadzin, Cerrad и т.д. — не имеют ничего общего с клинкером, материал этих заводов делается методом сухого прессования (не экструзия!!) с последующим скоростным обжигом в роликовой печи, материал по свойству ближе к обычному керамограниту, он всегда глазурован и покрашен. В России, единственный завод, который производит настоящие клинкерные ступени и напольную плитку это Ecoclinker.
Экструдированный керамогранит производят Stroher, Interbau, Gres de Aragon, Exagres, Gresmanc, Mayor и многие другие заводы Испании и Германии. Практически все заводы переориентировали свои производства на выпуск этой продукции, т.к. эта технология дешевле в себестоимости и производительность по сравнению с клинкерным производством больше от 20 до 40 раз. Представьте себе, что за одинаковый промежуток времени можно произвести 1000 м2 клинкера или 30000 м2 экструдированного керамогранита !! Что заводу выгоднее делать….? 🙂 В России пока не производят керамогранит методом горизонтальной экструзии. У нас делают керамогранит методом сухого прессования – такая технология для производства напольной плитки гораздо лучше, чем методом экструзии (т.к. пресс под высоким давлением гораздо качественнее и плотнее делает заготовку) но методом сухого прессования невозможно сделать фронтальную ступень с «литым капиносом», по этому, все ступени отечественных керамогранитных плиточных заводов (Керама Марацци, Эстима, Италон, и т.д.) делаются с клееными капиносами или производятся путем нарезки «насечек» на обычной плитке или они и вовсе не имеют в своем ассортименте фронтальных ступеней, а продают только напольную или настенную плитку.
ВАЖНО: Если материал отформован методом вертикальной экструзии-высушен в сушильных камерах и обожжен в туннельной печи – это КЛИНКЕР. Если материал отформован методом горизонтальной экструзии-обожжен в роликовой печи – это НЕ КЛИНКЕР и можно назвать его как угодно, например: Каменная керамика, Концептуальная керамика, Морозоустойчивая керамика и т.д. Настоящий клинкер невозможно обжечь в роликовой печи – а экструдированную керамогранитную массу невозможно обжечь в туннельной печи.
Подведем итог: если вы выбираете себе материал для облицовки крыльца, ступеней, площадки под автомобиль, зоны мангала или барбекю, то вам в равной степени неплохо подойдут оба вида рассматриваемого нами материала. Но настоящий клинкер, в любом случае, будет иметь преимущество как более прочный, практичный и более долговечный материал. Экструдированный керамогранит порадует своих покупателей обилием всевозможных рисунков и расцветок. Радовать правда будет не долго, т.к. при неаккуратном использовании он склонен к разрушению глазуровки и покраски и в конечном итоге потерей эстетики и внешнего вида с последующим ремонтом или замены на настоящий клинкер 🙂
Цвет Градиент Керамика Неровная Поверхность Керамогранит Облицовка Клинкером Плитка 60×240мм Дешевая Цена
Описание продукта
Название продукта |
Цветная керамическая клинкерная плитка Turn Color |
Серия изделий | Y серии |
Размер (мм) | 60×240 мм |
Толщина (мм) | 11 мм |
Водопоглощение | 3% -6% |
Обычный продукт | Есть |
Образцы | Бесплатно |
Индивидуальные | Да для заказа свыше 5000SQM |
Advantange | Деревенский, Легкий для переноски, Экологичный, Низкая стоимость |
Использование | Высокий средний тип европейского здания, виллы, административного здания, коммерческого здания, супермаркета, общественных культурных мест, художественной галереи, музея, клуба отдыха, площади, школы, резиденции, Gradens и т. Д. |
Разнообразие цветов и стилей для справки
Проектное шоу
Информация о компании
Цюаньчжоу Aitop строительных материалов CO ,. LTD — предприятие по производству и продаже строительных материалов, специализирующееся на производстве керамической / фарфоровой, полнотелой / глазурованной / полированной, настенной / напольной плитки. Наши заводы расположены в зарубежных китайских — Цюаньчжоу, Фуцзянь.Имея более чем 20-летний опыт производства и продажи, наше основное производство высококачественного стенового кирпича марки «AITOP» и высококачественного ручного кирпича марки «LANGYU», продажа продукции на внутреннем и внешнем рынке, особенно на Ближнем Востоке и в Западной Азии. , Юго-Восточная Азия, Африка, Южная Америка и другие регионы, пользующиеся спросом у потребителей, сеть продаж становится все более зрелой!
.
полированных керамических плиток из керамической плитки Super White Nano Spain Neo Tiles
Керамогранит Super White Nano Spain Neo Tiles
Материал | Полностью полированная | 60x60cm / 80x80cm |
Поверхность | Фарфор |
Водопоглощение | 0.5% |
Упаковка | Картонные коробки и поддон из фанеры |
Применение | Стена и пол |
Размер (мм) | Толщина (мм) | Шт. / КОРОБКА | М² / кг | кг / КОРОБКА | КОРОБКИ / ПОДДОН |
600×600 | 10 | 4 | 1,44 | 34 | 40 |
800×800 | 10 | 3 | 1 .92 | 51 | 28 |
1.Realgres Ceramics имеет более чем 10-летний опыт экспорта в области плитки, мы знаем все правила международной торговли
разных стран.
2. 80% продукции на нашем заводе находится на складе, поэтому мы можем осуществить доставку по вашему запросу.
3.Realgres Ceramics может заниматься оптовой торговлей, розничной торговлей, зарубежными проектами и частным домашним украшением
и некоторыми специальными дизайнерскими продуктами, которые запрашиваются у всех клиентов.
4. Мы всегда уделяем особое внимание качеству нашей плитки и лучшему обслуживанию наших уважаемых клиентов.
.