Керамзитобетон – это тот же цементный раствор, который применяется для заливки стяжки. Но поскольку в качестве крупного заполнителя здесь используется не тяжелый щебень, а вспученные глиняные гранулы, пол получается более теплым. Керамзит довольно хрупок и не годится для полноценного выравнивания активно эксплуатируемых поверхностей. Его главное предназначение – создание легкого тепло- и звукоизоляционного слоя, не дающего серьезного увеличения нагрузки на основание.
Оглавление:
- Из чего состоит керамзитобетон?
- Необходимые пропорции для различных марок
- Нюансы приготовления
- Особенности работы с раствором
Компоненты смеси
Чтобы сделать керамзитобетон своими руками, понадобятся вспученные гранулы крупностью 5-10 или 5-20 мм с насыпной плотностью 600-700 кг/м3. Мелкий песок не столь эффективен, но используется при устройстве тонкой заливки до 30 мм. Крупные фракции чаще применяют для сухой и полусухой стяжки. Окончательный выбор зависит от нагрузок на будущий пол:
1. Лучшие результаты показывают смеси, где присутствуют все классы крупности от 5 до 40 мм в равном соотношении. В этом случае стяжка получается чуть более плотной и тяжелой, зато достаточно прочной. При этом одновременно снижается расход цемента.
2. Для уменьшения нагрузки на перекрытия керамзит выбирают покрупнее. Готовая стяжка при большой толщине со временем может дать усадку, но только так удастся выровнять серьезные перепады поверхности, достигающие 10-15 см.
3. При небольшой толщине бетона и необходимости избавиться от усадочных явлений остается только один вариант – мелкий керамзитовый песок.
Что касается цемента, то здесь экономить нельзя, поскольку только от него зависит, насколько крепко друг с другом сцепятся гранулы вспученной глины. Как минимум, это должно быть вяжущее с марочной прочностью М400, но можно использовать и более дорогой ПЦ М500. Главное, чтобы портландцемент шел без замещающих шлаковых добавок.
К мелкофракционным заполнителям также предъявляются повышенные требования, поскольку они тоже способны влиять на прочностные характеристики керамзитобетона. Это и обычный карьерный песок, но непременно просеянный и мытый. Для уменьшения плотности стяжки и увеличения ее теплоизоляционных свойств фракции песка лучше выбирать покрупнее.
Поскольку готовый раствор не обладает достаточной подвижностью (его характеристики соответствуют самому низкому классу П1), для улучшения удобоукладываемости смеси в нее вводят пластифицирующие добавки. Можно использовать воздухововлекающие модификаторы типа СДО, которые дополнительно поризуют цементную матрицу. Но дешевле и проще самостоятельно влить в бетоносмеситель жидкое мыло из расчета 50-100 мл на ведро ПЦ.
Пропорции для разных марок
Для определения масштаба работ понадобится измерить площадь помещения и рассчитать высоту будущего слоя керамзитобетона. Объем заливки – это и есть количество глиняного заполнителя в кубометрах, от которого следует отталкиваться в дальнейших расчетах. «Теплый» монолит можно получить разной плотности – от 1000 до 1700 кг/м3 (хотя для пола лучше использовать наиболее прочные покрытия), в соответствии с этим будут изменяться и пропорции для стяжки.
Плотность керамзитобетона, кг/м3 | Вес на кубометр смеси, кг | ||
Керамзит М700 | Цемент М400 | Песок | |
1500 | 560 | 430 | 420 |
1600 | 504 | 400 | 640 |
1700 | 434 | 380 | 830 |
При хорошем увлажнении керамзита для таких пропорций хватит 140-200 л воды на куб раствора. Если же замачивание оказалось недостаточно эффективным, количество жидкости может быть увеличено до 300 л/м3.
Традиционно строители пользуются упрощенным соотношением для получения керамзитобетона марочной прочности М100 – оптимальной для устройства своими силами «теплой» стяжки. Для этого на 1 часть цемента берут:
- 3 ч песка;
- 4 ч вспученного керамзита;
- 1 ч воды.
При таких пропорциях можно даже приобрести готовую сухую смесь пескоцемента, где сыпучие материалы как раз идут в соотношении 1:3. Если же стяжка нужна попрочнее, для нее просто выбирают другую рецептуру приготовления:
Марка керамзитобетона | Цемент | Песок | Керамзит |
М150 | 1 | 3,5 | 5,7 |
М200 | 2,4 | 4,8 | |
М300 | 1,9 | 3,7 | |
М400 | 1,2 | 2,7 |
При работе с цементом более высокой марки М500 и устройства стяжки в бытовых помещениях с эксплуатационными нагрузками не выше среднего рекомендуется использовать следующее соотношение компонентов на куб керамзита:
- 295 кг цемента;
- 1186 кг крупнозернистого песка;
- 206 л воды.
Легкие стяжки готовятся из керамзита плотностью 200-300 кг/м3 без добавления песка. Здесь понадобится составить раствор с таким соотношением:
- 720-1080 кг гранул вспученной глины;
- 250-375 кг цемента;
- 100-225 л воды.
Рекомендации по приготовлению
Первым в емкость засыпается керамзит. Гранулы перед этим нужно вымочить в воде, чтобы они напитались влагой и потом не тянули ее из бетона. Долив еще немного жидкости, в корыто или барабан смесителя высыпают пескоцемент, тщательно перемешивая раствор. При правильно подобранных пропорциях керамзитобетона все гранулы в процессе изготовления должны стать одинакового серого цвета – без коричневых пятнышек.
Если смесь покажется недостаточно текучей, можно добавить в нее еще немного воды. При избытке влаги досыпать сухие компоненты не следует, так как это не позволит размешать их до однородности и ухудшит качество керамзитобетона, нарушив соотношение цемента. В этом случае лучше дать немного настояться, после чего еще раз перемешать.
Приготовление должно выполняться быстро и без задержек. Как только гранулы полностью покроются цементной кашицей, состав нужно сразу выливать на основание, разравнивая по установленным маякам. Раствор с керамзитовым заполнителем схватывается быстрее обычного бетона, зато уже через неделю по такому полу можно будет свободно перемещаться. Окончательный набор прочности происходит в течение 28 дней.
Особенности работы с керамзитобетоном
На пол перед заливкой обязательно нужно постелить гидроизоляцию или обмазать его и нижнюю часть стен битумной мастикой. В противном случае влага впитается в основание, не дав цементу набрать требуемую прочность. Такая заливка получится немонолитной и очень хрупкой – будет расползаться под нагрузкой и пылить. Также по периметру комнаты обязательно следует закрепить демпферную ленту, чтобы компенсировать тепловое расширение. По окончании работ стяжка из керамзитобетона потребует дополнительной защиты от испарения влаги. Для этого ее сверху накрывают пленкой, которую через пару-тройку дней можно будет снять.
Готовый слой «теплого» бетона нуждается в финишном выравнивании – желательно с предварительной шлифовкой. Сверху он заливается обычным раствором из пескоцемента толщиной не более 30 мм (без добавления гравия). Этого достаточно, чтобы скрыть неровности, но не ухудшить теплоизоляционные характеристики чернового основания. Финишную заливку выполняют по маякам, тщательно выравнивая смесь правилом. Рейки на следующий день аккуратно извлекают, а оставшиеся следы заделывают свежим составом.
Полусухая стяжка – еще один вариант утепления и выравнивания пола с помощью керамзита, позволяющий обрабатывать небольшие участки один за другим. В этом случае на подготовленное основание с установленными маяками засыпают сухие гранулы вспученной глины – на такую высоту, чтобы 20 мм маячкового профиля оставались незакрытыми. Сверху их проливают жидким цементным раствором (молочком) и утрамбовывают, склеивая зерна керамзита между собой. Через день-два поверхность заливается финишной стяжкой – приготовление бетона для нее ничем не отличается от уже рассмотренного «мокрого» способа.
Пропорции керамзитобетона для стяжки пола
Первые попытки использовать легкий наполнитель для раствора были предприняты еще во времена античности. Но керамзит, гранулы с высокими строительными характеристиками, смогли создать только во второй половине ХХ века. При замене ими щебня или гравия в бетоне получили новый материал – керамзитобетон. Пропорции керамзитобетона зависят от назначения раствора.
Характеристика керамзитобетонного раствора

Характеристики керамзитобетона
Из смеси можно строить очень многое. Монолитные и блочные здания, теплоизоляционные покрытия, перекрытия и стяжка для пола – вот далеко не полный список возможностей применения этого материала. Гранулы дали ему новые свойства: небольшой вес, что позволяет использовать материал там, где обычная бетонная смесь слишком тяжела (при этом потерь прочности нет), а также пористую структуру, которая увеличивает теплопроводность.
Отрицательное качество у него только одно – гранулы хорошо поглощают влагу. Из керамзитобетона нельзя строить там, где возможны частые атмосферные осадки (потребуется дополнительная гидроизоляция).
Его марку определяют прочность (М) и плотность (D). Бетон с наполнителем из пористых гранул подойдет для различных целей. От них зависит необходимая плотность материала.
Назначение | D |
теплоизоляция | До 700 |
перегородки | 700–1400 |
стены | 1400–2000 |
Марка керамзита для приготовления керамзитобетона характеризует объемную массу, то есть насыпную плотность. Чем мельче фракция, тем выше марка.

Фракции керамзита
Состав керамзитобетона
Керамзитобетон – необычный строительный материал. Его прочность и теплопроводность зависит от применяемой фракции гранул. Если они имеют большой размер, теплопроводность смеси будет выше, но она будет легче и менее прочной, подойдет для теплоизоляции, но не для несущих конструкций.
Их делают из раствора с мелкой фракцией, у которого высокая прочность, но меньшие теплоизоляционные свойства.
Для приготовления керамзитобетона с универсальными свойствами берут наполнитель из смеси различных фракций. Он должен отвечать всем предъявляемым требованиям.

Таблица качественных и геометрических пропорций керамзитобетона
Количество связующих меняется в зависимости от предназначения. Основные составляющие:
- керамзит с различным размером фракций;
- вода для приготовления бетона, соответствующая ГОСТу;
- песок строительный кварцевый – он делает бетон пластичным;
- цемент обычный или алитовый, портландцемент – с ним можно сделать раствор и без пластификатора.
Состав керамзитобетона напоминает обычный бетон. Отличие – не только особый наполнитель, но и наличие пластификатора, а иногда – золы либо опилок.
Приготовление керамзитобетона – соотношение количества материалов
Пропорции керамзитобетона зависят от его назначения. Для теплоизоляции и перегородок его делают с небольшим количеством песка или совсем без него. Стены обязаны выдерживать высокие силовые нагрузки, поэтому в стеновом материале связующих веществ больше.
Для возведения монолитных зданий пропорции керамзитобетона меняются: гранул в материал добавляют больше для улучшения теплоизоляционных свойств. Чтобы раствор получился одновременно вязким и текучим, его готовят по следующему рецепту (в частях):

Пропорции составляющих компонентов керамзитобетона
- керамзит – от 4 до 5;
- цемент – 1;
- песок – от 3 до 4.
При измерении в ведрах, воды на это количество требуется около 1,5 ведер, объем зависит от консистенции полученного бетона. Он не должен терять вязкости, оставаясь пластичным. Можно добавить заводской пластификатор по инструкции. На практике часто используют мыльный раствор или жидкое мыло. На 1 такой замес мыльного пластификатора потребуется от 2 до 3 крышечек от обычной пластиковой пятилитровой бутылки.
Для возведения зданий часто используются керамзитобетонные блоки фабричного производства. Их производят со специальной фасадной стороной, не требующей дополнительной отделки и гидроизоляции. Многие застройщики с успехом делают такой строительный материал самостоятельно. Но постройка из него потребует гидроизоляции и дополнительной отделки фасада.
Материал для блоков готовят в бетономешалке. В отличие от обычной смеси с наполнителем из гравия или щебенки, размешать бетон с керамзитовыми гранулами вручную очень сложно, добиться однородности не получится.
Как замесить керамзитобетон в бетономешалке?
Пропорции для керамзитных блоков на один замес в бетономешалке:
- цемент марки М400 – 7 кг;
- вода – 5 л;
- мыльный раствор – 50 мл;
- песок – 28 кг;
- наполнитель – от 0 до 10 мм – 36 кг.

Состав керамзитобетона
Для качества материала немаловажен порядок замеса:
- Вливают в чашу бетономешалки воду и жидкое мыло.
- Включают ее, добавляют цемент.
- После перемешивания высыпают песчаную составляющую.
- Последним засыпают наполнитель, к этому времени смесь должна стать полностью однородной.
Время приготовления бетона не должно быть больше 7 мин., если мешать дольше, он станет менее качественным. За это время все гранулы равномерно обволакиваются жидкими составляющими. Смесь выливают в специальные формы поэтапно слоями и дают полностью застыть. Чтобы создать полые изделия, при заливке в формы помещают стеклянные бутылки горлышком вверх на одинаковом расстоянии. После застывания их вынимают.

Преимущества керамзита
Пользуясь таблицей, можно приготовить бетон в бетономешалке для любых строительных надобностей. Все составляющие даны в частях.
Для чего | Вода | Цемент | Песок | Наполнитель |
Стяжка для пола | 1 | 1 | 3 | 2 |
Стены | По потребности | 1 | 1,5 (песок керамзитовый) | 1(мелкая фракция) |
Перекрытия | 1,5 | 1 | 3–4 | 4–5 |
При изготовлении монолитных стен, стяжки пола и перекрытий, укладывая бетон, нельзя забывать об армировании.

Процесс стяжки пола керамзитобетоном
Видео по теме: Приготовление керамзитобетона
Керамзитобетон для стяжки: необходимые пропорции
Оглавление:- Состав керамзитобетона
- Заливка стяжки пола из керамзитобетона
- Сухая и полусухая стяжка пола
Керамзитобетон строительный материал, основой которого является керамзит. Воздушные гранулы получаются в результате термической обработки глины. Благодаря хорошим характеристикам теплоизоляции и легкому весу керамзитобетон используют для стяжки пола.
Керамзитобетон – вид легкого бетона, предназначенный для теплоизоляции и строительства различных конструкций.
Данный материал обладает такими достоинствами:
- экологичность,
- стойкость к горению и химическому воздействию,
- отсутствие коррозии,
- сыпучесть, что позволяет выравнивать перепады на горизонтальных плоскостях,
- звукоизоляция,
- прочность,
- долговечность.
Недостатком керамзитобетона можно считать хрупкость и необходимость в дополнительной обработке стяжки.
Состав керамзитобетона
Этот стройматериал в своем составе имеет такие компоненты: цемент, песок, вода, керамзит.
Таблица пропорций материалов при изготовлении керамзитобетона.
Керамзитобетон для стяжки может выступать в качестве гравия, щебня или песка. Гранулы имеют овальную форму средних размеров. Щебень многогранные куски больших размеров с острыми углами. Керамзитовый песок получается в результате раскола больших кусков материала на мелкие.
Для стяжки пола из керамзитобетона используют гравий. Пропорции для стяжки в классическом варианте имеют такой вид:
- цемент 1 часть,
- вода 1 часть,
- песок 3 части,
- керамзит 2 части.
После заливки пола из керамзитобетона поверхность надо будет обработать финишной стяжкой. Это необходимо, для того чтобы выровнять пол.
Пропорции для стяжки пола из керамзитобетона зависят от способа заливки: сухого или мокрого. Соотношение различных компонентов позволяет получить раствор разных марок.
Чтобы получить керамзитобетон марки М150, пропорции цемента, песка и керамзита должны быть 1:3,5:5,7. Пропорции данных элементов для марки М300 будут 1:1,9 :3,7, для марки М400 1:1,2:2,7.
На 1 кв.м стяжки толщиной 3 см понадобится 16 кг цемента и 50 кг песка.
Вернуться к оглавлениюЗаливка стяжки пола из керамзитобетона
По способу заливки различают: мокрую, полусухую и сухую стяжку.
Для мокрой стяжки пола требуются такие пропорции компонентов:
- 1 часть цемента,
- 3 части песка,
- 4 части керамзита.
Схема блока из керамзитобетона.
Это значит, что на 25 кг керамзита необходимо взять 30 кг пескоцемента. Керамзитовый гравий высыпают в большую емкость и добавляют воду небольшого количества. Гранулы должны некоторое время побыть под водой, чтобы впитать ее.
Затем в данную емкость добавляют цемент и песок, постоянно помешивая. Мешать надо до тех пор, пока гранулы не станут цвета цемента, а сам раствор не приобретен вязкую сметано подобную консистенцию. При густом растворе надо немного добавить воды.
Перед заливом стяжки на бетоне должна быть уложена гидроизоляция, иначе керамзитобетон не наберет нужной прочности. Сверху залитый пол также необходимо накрыть пленкой на 2-3 дня, чтобы влага не испарялась.
Затем необходимо провести финишную стяжку, чтобы выровнять все бугорки. Результат получится более эффективным, если перед финишной заливкой пол прошлифовать.
Финишный слой должен быть не более 3 см. Для его приготовления необходим цементный раствор, только без добавления щебня. Чтобы добиться ровной поверхности, надо соорудить новые маяки из металлических профилей, высотой 27 мм. Далее заливают финишную стяжку, выравнивая правилом.
Возможен вариант выполнения двух слоев стяжки одновременно, который делает конструкцию более однородной. Метод заключается в следующем:
Схема устройства полусухой стяжки, на подготовку из керамзитобетона.
- На небольшом участке засыпают керамзитобетон.
- На маяки устанавливают направляющий профиль.
- Поверх заливают финишную стяжку, выравнивая по профильным маякам.
- Приступают к заливке следующего участка.
Таким образом площадь заливается отдельными участками.
На следующий день после финишной заливки достают направляющие профили, а свободные канавки заполняют раствором. Лазерным уровнем проводят контрольный замер ровности пола.
Благодаря легкому весу пол из керамзитобетона можно обустраивать даже на чердачном перекрытии из деревянных балок. К тому же керамзитобетон дешевле цемента, что делает его доступнее к использованию.
Вернуться к оглавлениюСухая и полусухая стяжка пола
Способы полусухой и сухой стяжки немного отличаются от предыдущего варианта. Технология полусухой стяжки подразумевает поэтапную засыпку материалов.
Вначале надо качественно очистить бетонное основание, заделать цементным раствором все трещины и неровности.
Укладку бетонной смеси следует начинать с дальней стены комнаты в направлении дверного проема.
Далее выполняют слой гидроизоляции. Для этого можно покрыть бетон битумной мастикой или постелить гидроизоляционную пленку. Эту мембрану укладывают с захлестом на стены не менее 15 см. Все электропровода следует уложить в изоляционные короба. По периметру комнаты проклеивают демпферную ленту.
После того как основание подготовлено, приступают к выставлению маяков. Они нужны для того, чтобы уровень пола был ровный, так как по ним ориентируют высоту засыпки гранул. Расстояние между соседними маяками должно быть не менее 0,5 м.
Керамзитовые гранулы следует засыпать с дальнего угла, двигаясь к двери. Верх засыпки должен быть на 2 см ниже уровня маяка. Керамзитовый слой периодически ровняют правилом.
Пол поливают сверху жидким цементом и трамбуют. Гранулы должны хорошо сцепиться между собой.
Через сутки заливают песчано-цементный раствор, выравнивая поверхность. Следует избегать появления выбоин и луж.
Готовой стяжке надо постоять не менее суток, а уже потом доставать из нее маяки. Получившиеся зазоры заделывают раствором и слегка сбрызгивают водой. После высыхания поверхность шлифуют.
Полное высыхание пола происходит в течение 3-4 недель, но ходить по нему при необходимости можно уже через 2-3 дня. Через 2 недели стяжку можно покрывать напольным покрытием: ламинатом, линолеумом, паркетом.
Сухой метод стяжки пола из керамзита самый быстрый. Все подготовительные этапы работ такие же, как в предыдущем варианте. Отличие состоит в том, что на уложенный слой керамзита не заливают цементный раствор, а покрывают его фанерой или гипсокартонном. Последний материал стелют в 2 слоя, перекрывая швы, закрепляя саморезами.
Таким образом, пол из керамзита это не только надежно, но и экологически чисто. Такое основание будет надежно служить жильцам долгие годы.
состав и пропорции, своими руками
Керамзитобетон — аналог бетонного раствора, используемого для половой стяжки. Только в составе стройматериала вместо мелкой щебенки используются вспученные глиняные гранулы, в результате получается теплое половое основание. Соблюдая для керамзитобетона пропорции, установленные строительными нормами, его можно приготовить самостоятельно. Но керамзитобетон — это хрупкий строительный материал, поэтому его не используют для выравнивания поверхностей, которые будут впоследствии подвергаться постоянным нагрузкам.


Материал представляет собой композит с пористой структурой, применяемый в строительстве.
Виды керамзитобетона и их характеристики
Основные характеристики керамзитобетона определяют его марка и плотность. Эти показатели зависят от используемых компонентов в составе строительного материала и их фракций.
По плотности различают 3 категории стройматериалов:
- беспесчаные;
- поризованные;
- плотные.


Плотный бетон содержит повышенное количество цементного состава.
Для производства беспесчаных бетонов применяется цемент, гравий и вода. Песок в раствор не добавляется. Материал недорогой, применяется для обустройства малоэтажных зданий: стен, перекрытий и половых оснований.
Из поризованных смесей производят 3 типа строительных блоков, отличающихся друг от друга прочностными показателями:
- теплоизоляционные блоки d(400-700) — применяются для утепления стен зданий;
- теплоизоляционно-конструкционные изделия d(800-1400) — предназначены для утепления и возведения внутренних перегородок;
- стеновые стройматериалы d(1400-2000) — используются для строительства инженерных конструкций.
В состав плотного керамзитобетона входит большое количество цемента, при этом его характеристики сочетают свойства поризованного и беспечанного бетона. Этот стройматериал дорогой, поэтому в строительстве используется редко.
Также керамобетон классифицируется по объемной массе.
По этому показателю строительный материал делится на 3 категории:


- тяжелый — объемная масса 1200-1400 кг/куб. м, значение прочности — 25 МПа;
- легкий — объемная масса 800-1000 кг/куб. м, в его состав входит легкий керамзитовый компонент;
- особо легкий — объемная масса 600-1800 кг/куб. м, значение прочности — 7,5-40 МПа.
При самостоятельном изготовлении бетонного раствора в него можно добавлять, кроме керамзита, шлаковую пемзу или зольный гравий.
Какие марки бывают
Керамзитобетон по прочностным характеристикам может быть следующих марок:
- М300 — материал отличается повышенными прочностными показателями, поэтому его используют при строительстве фундаментных оснований и несущих инженерных конструкций.
- М200 — используется для отливки легких цокольных перекрытий и производства строительных блоков для возведения стен.
- М150 — материал предназначен для отливки стеновых панелей, производства легких керамзитовых блоков.
- М100 — состав часто используют для обустройства половых стяжек.
- М(50,75) — стройматериал предназначен для обустройства перегородок в помещениях и теплоизоляции наружных стен.


Фракции керамзитобетона.
Что строят из этого вида бетона
Керамзитобетон — это универсальный материал, который широко применяется в строительной области. Его особенность — возможность регулировать необходимую плотность готового стройматериала.
Применение керамзитобетона:
- В малоэтажном строительстве. Из легкого керамзитобетонного раствора производят строительные блоки, панели, прочие материалы перекрытия. Часто этот стройматериал используют для возведения бань и как внутренний слой многоуровневых стеновых панелей.
- Для обустройства стяжки половых оснований, внутренних перегородок. При заливке стяжки пола материал выполняет теплоизолирующую функцию. Чтобы половая стяжка быстрее затвердела и набрала необходимую прочность, рекомендуется делать раствор в следующей пропорции: 1 часть цемента, 3 части песка, 2 части камня, 1 часть воды.
- Производство плит перекрытия. Строительный материал изготавливается по литьевой технологии. Преимущества готовых изделий: сохранение тепла внутри дома, небольшая масса, влагостойкость, продолжительный период эксплуатации. Единственный недостаток — стройматериал достаточно хрупкий.
- Возведение фундаментов и несущих стен зданий. Для этих целей применяются высокопрочные керамзитобетоны, изготовленные из портландцемента. Монолитные плиты дополнительно армируют стальным каркасом, что увеличивает прочность материала.
Блоки из керамзита
Блоки из керамзитобетона в зависимости от их назначения изготавливают разных размеров. Изделия могут иметь различный внешний вид. Основными видами стройматериала являются полнотелые и пустотелые блоки.
Пустотелые изделия по форме полостей делятся на следующие подвиды:
- цилиндрические;
- прямоугольные;
- щелевые;
- мелкощелевые.
Полнотелые изделия, в отличие от пустотелых блоков, имеют высокую прочность, но низкие теплоизоляционные качества. Под заказ такие блоки производятся с отверстиями для металлических штырей.
Основным связывающим компонентом строительных блоков является цемент. При изготовлении материала своими руками необходимо помнить следующее: чем больше цемента добавить в раствор, тем ниже у изделия будут теплоизоляционные показатели. Для повышения водоотталкивающих качеств стройматериала часто используют гидрофобный цемент.
При необходимости выполнения термообработки керамзитобетонных блоков рекомендуется в смесь добавлять незначительную долю алитового цемента. В этом случае при нагревании будет быстрее осуществляться полимеризация изделий.
Состав
Сделать керамзитобетонную смесь самостоятельно несложно. Главное — выдержать пропорции составных компонентов раствора, которые зависят от предназначения материала.
Стандартные пропорции составных компонентов керамобетона:
- 1 доля цемента;
- 2 доли песка;
- 5 долей керамзита.
Дополнительно в керамзитобетон могут подмешиваться опилки или зола.


Таблица пропорций бетона.
При изготовлении керамобетона сухие компоненты первоначально тщательно перемешиваются без воды, а уже после этого с жидкостью. Такую смесь можно изготовить самостоятельно. Для приготовления керамзитобетонной смеси рекомендуется использовать только чистую холодную воду, т.к. примеси ухудшают затвердевание бетона. При использовании загрязненной воды на поверхности готовых изделий будет проявляться белый налет, поэтому лучше брать питьевую жидкость.
Если нужно сделать строительные блоки, понадобятся специальные формы. В них заливается готовая смесь, уплотняется с помощью вибрационного устройства, при необходимости добавляется нужное количество раствора. После заливки изделия выдерживаются неделю на свежем воздухе.
Пропорции смеси с керамзитом для различных целей
Керамзитобетон используют не только для изготовления строительных блоков. Это универсальный материал, подходящий для разных целей: заливки половых оснований, возведения стен и обустройства перекрытий сооружений.
Для пола
Пропорции компонентов смеси для выполнения половой стяжки:
- 1 часть цемента М500 и выше;
- 2 части мелкофракционного гравия;
- 3 части керамзитового песка;
- 1 часть воды.
Сначала все компоненты перемешиваются насухо, затем с водой.
Для стен
Рецепт смеси для возведения монолитных стен сооружений:
- 1 часть цемента М400;
- 1,5 части песка;
- 1 часть мелкофракционного керамзита;
- 1 часть воды.
Такой раствор применяют в малоэтажном строительстве — до 3 этажей.
Для перекрытий
Соотношение компонентов смеси для обустройства армированных керамзитобетонных перекрытий:
- 1 часть цемента;
- 3-4 части песка;
- 4-5 частей керамзита;
- 1,5 части воды.
Чтобы бетон получился эластичным, в него нужно добавлять пластификатор. Способ применения материала указывается в инструкции от производителя.
Стяжка для пола с применением керамзита нужна для того чтобы поднять уровень пола на 1-1,5 см. Такую методику применяют, когда требуется вывести полы на один уровень во всех комнатах. Когда смешивают керамзит с пескобетоном, пропорции должны быть соблюдены. Керамзитобетонный раствор применяют для таких типов поверхности:
- горизонтальной;
- внутренней;
- внешней;
- наклонной;
- жилой;
- производственной.
Перед началом строительных работ по заливке пола, рассчитывают толщину слоя керамзита и пескобетона, при этом следует учитывать нагрузку, которая будет влиять на пол. Если поставлена задача, утеплить полы на первых этажах в здании либо в комнатах, которые расположены над помещением без отопления. Рекомендуется делать слой керамзита не меньше 10 сантиметров. В противном случае надежная теплоизоляция не получится. Для устройства тонкой стяжки толщиной 6 см понадобится 21 мешок пескобетона и 12 мешков керамзита.
Достоинства керамзитобетонной стяжки
- повышенные теплоизоляционные качества;
- высокий уровень звукоизоляции;
- стройматериал экологически чистый не оказывает отрицательное влияние на здоровье человека;
- готовая конструкция обладает высоким запасом прочности;
- материал устойчив к грибкам и плесени;
- длительные ресурсы эксплуатации;
- отсутствие образования трещин при перепадах температур;
- производить работы по заливке не составит особого труда;
- имеется возможность выровнять неравномерное основание;
- отличное сочетание с разными типами покрытий;
- небольшой вес;
- пожароустойчивость;
- стойкость к влиянию химических составов;
- влагоустойчивость.
Вышеперечисленные достоинства позволяют формировать качественное покрытие, которое предназначено для длительного использования и монтажа различных типов финишных стройматериалов для пола.
Недостатки
- слой керамзитобетонного основания получается повышенной толщины;
- необходимы дополнительные шлифовальные работы;
- увеличение уровня затрат труда при бетонировании.
Пропорции составных элементов
Какое соотношение цемента и песка и керамзита понадобится для стяжки? Расчеты производятся по такой схеме:
- Если толщина слоя керамзита составляет 10 см, значит понадобится 1,5 м3 на 15 м2.
- Требуемое количество пескобетонного материала рассчитывается по инструкции, которую указал производитель на упаковке.
Рекомендуется для заливки стяжки применять готовые смеси керамзит и пескобетон, в состав стройматериалов входит сбалансированное количество компонентов.
При любой методике выполнения работ для приготовления смеси понадобятся такие ингредиенты:
- Керамзит в гранулах.
- Пескобетон.
- Вода.
Для того чтобы стяжка получилась качественной нужно соблюдать соотношение керамзита и пескобетона. К примеру, для заливки основы в жилом здании нужно смешать гранулы керамзита и пескобетона 1:1. Когда формируют классический вариант основания, толщина которого составляет 4 см, понадобится 52 кг пескобетона и 45 кг керамзита.
Приготовление раствора
- Вместительную емкость заполняют керамзитом.
- Добавляют воду.
- Гранулированный стройматериал перемешивают тщательным образом, после ждут, пока вода впитается.
- Остатки воды, которые не впитал в себя керамзит, сливают.
- Влажные гранулы загружают в автобетономешалку либо оставляют в емкости.
- Добавляют необходимое количество пескобетона.
- Вливают в полученный состав воду и производят перемешивание до получения однородной массы.
До каких пор нужно продолжать перемешивать ингредиенты? Смешивание прекращают, когда гранулы керамзита перестают выделяться из массы замеса.
Укладку керамзитобетонной смеси осуществляют разными способами
- Влажный. Для такой методики следует предварительно подготовить песчано-цементный состав, а затем залить его на прослойку керамзита и равномерно распределить по всей площади.
- Полусухой. Гранулы керамзита смешивают с пескобетоном и водой, после производят заливку.
- Сухой. Пескобетонный раствор перемешивают с керамзитом, укладывают на подготовленное основание.
Выбор методики формирования основания будет зависеть от индивидуального случая. Когда соблюдаются технологические рекомендации, каждой из типов стяжки разрешает формировать надежные основания для сооружения чистового слоя.
Мокрый метод
Смесь будет изготовлена с применением керамзита, соотношение составит 2:1. Должно получиться на объемы керамзита 80 см3 понадобится 80 мешков и 0.4 м3 сухого состава — 21 мешок пескобетона. Для замеса рекомендуется взять большую емкость.
Ход работ:
- Определение перепадов высоты основания, и определения максимально погруженного участка.
- Засыпают керамзит и равномерно распределяют.
- Пропитывают керамзитовые гранулы раствором цементного молочка.
- Заливают пескобетонный раствор и разравнивают, начинать рекомендуется с отдаленной зоны помещения и после перемещаться к выходу.
- Далее потребуется поддерживать благоприятные условия влажности, при помощи периодического увлажнения поверхностного слоя.
Нельзя подвергать массивную конструкцию механическим воздействиям впервые 24 часа, категорически не рекомендуется. Когда молочко затвердеет можно приступать к дальнейшим ремонтным работам. Квалифицированные строители советуют предохранять сформированную поверхность от механических повреждений 4 недели с момента заливки.
Полусухой метод
Особенности способа, который способен обеспечить сокращение сроков работы заключается в том, что керамзит добавляется непосредственно в пескобетонный раствор.
Ход работ:
- Бетономешалку заполняют керамзитом, после добавляют воду для того чтобы материал впитал ее.
- Добавляют пескобетон и производят смешивание ингредиентов до получения однородной массы.
- Производят армировку сеткой.
- Заполняют готовым раствором рабочую поверхность. Твердеющую поверхность следует периодически увлажнять и предохранять от сдвигов.
Техника полусухого метода требует обязательного устройства бетонного основания под прослойкой керамзита. Простота укладки и позволяет сформировать стяжку слоями, применяя существующие объемы рабочего состава. Расход материалов составит 1:1, берется 60 см3 керамзита – 12 мешков, плюс 60 см3 раствора пескобетона – 27-31 мешок, 20 м2 сетки для армировки. Сухой тип стяжки для основы делают без применения цементного раствора.
Сколько будет застывать материал
Полы из пескобетона и керамзита будут застывать по различной продолжительности времени в зависимости от влияния таких факторов:
- Температура окружающей среды.
- Толщина сделанной стяжки.
- Концентрация влаги в растворе.
- Циркуляция потоков воздуха в помещении.
Исправлять неровности на поверхности рекомендуется не ранее, чем через 24 часа после того как пол был залит. Когда влага полностью испарится и стяжка приобретет эксплуатационную прочность можно производить нарезку швов при помощи специальных инструментов.
Расчет керамзита и пескобетона для стяжки на 1 кв.м
Возьмем для примера пескобетон русеан и керамзит расход на 1 м2. Если знать пропорции стройматериала на 1 кв.м произвести, расчет на конкретные размеры помещения будет не сложно. Расчеты объемов нужных материалов производят следующим образом:
- возьмем слой стяжки равный одному сантиметру, пескобетона на 1м2 потребуется 18 кг. Если объем пола равен 100 м2, а слой стяжки 5 см высотой, то расчет происходит так: 18 кг х 100 м2 х 5.
- керамзит рассчитывается таким же образом. Для комнаты 12 м2 и толщине слоя керамзита в 10 см понадобится 1,2 м3 стройматериала – 16 м2 х 0,1 м.
Как правильно выполнить стяжку пола с керамзитом
По составу раствор будет иметь класс легкого бетона, а именно керамзитобетона. Пескобетон М 300 и керамзит будут иметь такие пропорции при приготовлении 1 м3:
- 20-25 мешков керамзита различной фракции. Объем составит 0.7 м3;
- 12-14 мешков пескобетона по 50 кг, марки М 300.
Сколько пескобетона потребуется на керамзит. Больше цемента в составе добавит прочностных качеств конструкции и увеличивает теплопроводность. Для того чтобы увеличить теплоизоляционные качества рекомендуется использовать меньшее количество цемента. Частные строители советуют применять оптимальное соотношение – это 2 мешка керамзитовых гранул на мешок 50 кг пескобетона.
Широкое распространение в строительстве получили легкие бетонные смеси. Керамзитобетон — одна из наиболее популярных разновидностей. Он существенно упрощает проведение строительных работ без потери прочности возводимых конструкций. Отличается высокой долговечностью, подходит для жилых зданий и промышленных сооружений. Для обеспечения наилучших эксплуатационных характеристик можно подобрать оптимальный состав и пропорции керамзитобетона.
Описание материала
Керамзитобетон представляет собой прочный монолитный строительный материал, отличающийся от классического бетона введением в состав смеси керамзита. В традиционном бетоне роль наполнителя играет щебень. Основное назначение керамзита, которым в керамзитобетоне заменен щебень, состоит в снижении массы готовой смеси.
Сырьем для производства керамзита служит глина или глинистый сланец. Исходный материал подвергается обжигу. Различные технологические режимы позволяют получать конечный продукт с заданной плотностью, которая варьируется от 150 до 800 килограммов на кубический метр. Относительная простота технологии производства позволяет поддерживать привлекательный для потребителей уровень цен. Материал отличается хорошими теплоизолирующими свойствами, долговечен, морозоустойчив. Отдельно стоит отметить натуральность и экологичность.
Обычно в состав керамзитобетона входят следующие компоненты:
- одна часть цемента;
- две части песка;
- три части керамзита.
Пропорции могут варьироваться в зависимости от назначения смеси и требуемых параметров прочности.
Иногда керамзитобетон ошибочно называют керамобетоном. Это грубейшая ошибка, поскольку керамобетон готовится не на цементной основе. Этот материал разработан в качестве эффективного огнеупора. Такие свойства обусловлены использованием высококонцентрированных керамических вяжущих суспензий и кремнеземного заполнителя. Вяжущим компонентом классического бетона и керамзитобетона является цемент.
Преимущества и недостатки
Для определения достоинств и недостатков следует обратить внимание на основные характеристики керамзитобетона. Именно от них зависит выбор материала для решения конкретных строительных задач.
Среди основных преимуществ нужно выделить следующие:
- Небольшая масса готовых изделий. Благодаря пористой структуре керамзита материал имеет малую плотность. Для зданий из керамзитобетонных блоков нет необходимости сооружать громоздкий фундамент, рассчитанный на высокие нагрузки. Самостоятельный монтаж блоков небольшой массы существенно снижает общие трудозатраты и сокращает сроки строительства.
- Приемлемая прочность. Керамзитобетон можно использовать для сооружения несущих стен и перекрытий, поскольку его прочность незначительно уступает классическому бетону.
- Хорошие теплоизолирующие свойства. Керамзитобетонные стены и пол обеспечивают сохранение тепла в помещении гораздо лучше, чем выполненные из классического бетона.
- Прекрасная звукоизоляция. Эта характеристика особенно важна при использовании материала для возведения жилого дома. Помещения будут хорошо защищены от проникновения уличного шума.
- Экологичность. Это преимущество обусловлено применением в качестве наполнителя керамзита, получаемого из глины. Все компоненты состава не выделяют в атмосферу вредных веществ.
- Долговечность. Керамзитобетон довольно давно используется в строительстве. За все время применения он зарекомендовал себя как надежный материал, способный прослужить много десятилетий.
- Низкая стоимость. Благодаря небольшой стоимости керамзита материал можно считать одним из самых дешевых вариантов изготовления бетонной смеси.
- Простота изготовления и распространенность. Несложная технология производства блоков привела к широкому распространению мелких производств. В связи с этим материал можно приобрести даже в небольших населенных пунктах, что обеспечит дополнительную экономию.
- Легкое проведение отделочных работ. Поверхность керамзитобетона характеризуется высокой адгезией. На ней прекрасно держатся штукатурные смеси любого состава.
Некоторые особенности керамзитобетона создают определенные ограничения в применении. Основным недостатком материала считается высокая влагопроницаемость и повышенное впитывание воды. Влага активно поглощается пористой структурой керамзита. Особенно опасно это свойство при отрицательных температурах, когда накопившаяся жидкость начинает кристаллизоваться и может привести к образованию трещин. По этой причине использовать такой стройматериал можно только в изолированных от погодных воздействий конструкциях. В случае применения материала для возведения наружных стен необходима тщательная гидроизоляция.
К незначительным минусам можно отнести и необходимость в дополнительной теплоизоляции. Несмотря на хорошие теплоизолирующие свойства материала, здания из керамзитобетона требуют утепления наружных стен.
Варианты применения
Керамзитобетон получил широкое распространение в строительстве.
Наиболее популярны два способа его применения:
- Для изготовления кирпичных блоков.
- Для создания наливного пола, то есть сооружения стяжки.
Не должно смущать то, что блоки именуются кирпичными. Кирпичами называются строительные элементы заданной формы, из которых сооружается кладка. Материал изготовления не играет роли. Таким образом, любые строительные блоки можно называть кирпичами.
Изредка керамзитобетон применяют и для возведения монолитных стен. Это может потребоваться в зданиях с деревянными перекрытиями, поскольку снижение массы стен является приоритетной задачей.
Изготовление блоков
Чтобы сэкономить на покупке готовых блоков, можно сделать керамзитобетон своими руками. Пропорции компонентов могут незначительно отличаться, однако наиболее популярен следующий рецепт: одна часть цемента; две-три части песка; одна часть воды; три-пять частей керамзита.
Для изготовления раствора рекомендуется использовать бетономешалку, она существенно упростит перемешивание. Большое значение имеет последовательность смешивания компонентов:
- Первым в бетономешалку или бункер для перемешивания загружается цемент. К нему добавляется песок. Эти сыпучие составляющие необходимо тщательно перемешать.
- К полученной смеси постепенно добавляется вода, состав перемешивается до получения однородной консистенции.
- На заключительном этапе в цементный раствор вводится керамзит. Смесь размешивается до равномерного распределения наполнителя.
Керамзит чрезвычайно гигроскопичен. Он настолько активно впитывает влагу, что иногда смесь может стать практически сухой. Применять ее в таком состоянии не представляется возможным, поэтому требуется добавить небольшое количество воды. Следует добиваться лишь полного покрытия поверхности керамзита цементным раствором. Доводить смесь до жидкой консистенции нельзя, иначе формирование будущего блока будет нарушено, он может рассыпаться при извлечении из формы или будет иметь серьезные дефекты.
Полученный раствор помещают в заранее приготовленные формы. Необходимо проследить за полным заполнением форм, чтобы исключить образование пустот в готовом изделии.
Для упрощения изготовления смеси не обязательно приобретать цемент и песок отдельно. В продаже имеется готовая сухая смесь, называемая пескобетоном. Рекомендуется применять марку М-300 и выше, это обеспечит достаточную прочность готовым блокам.
Выполнение стяжки
Устройство наливного пола предполагает использование жидкой смеси.
Для ее приготовления смешивают:
- одну часть цемента;
- три части песка;
- одну-две части воды;
- две части керамзита.
Указанное количество воды можно считать базовым. В процессе перемешивания керамзит будет активно впитывать жидкость. Воду можно добавлять до получения консистенции жидкой сметаны. Раствор составляется и перемешивается в той же последовательности, какая рекомендована для изготовления блоков.
Есть дополнительные условия, которые необходимо соблюдать перед нанесением раствора. Бетонная плита перекрытия не должна контактировать с влагой. Нельзя допускать, чтобы сухой бетон или другой материал основания впитывал воду. Для этого требуется обязательная гидроизоляция. Лучше всего для этих целей использовать специальные готовые составы, имеющиеся в продаже. Обычно они выпускаются в виде мастик или эмульсий. Заблаговременно нанесенное на основание гидроизолирующее средство обеспечит правильное затвердевание смеси с образованием монолитной структуры.
Через пару дней раствор достаточно затвердеет. После этого можно приступать к нанесению финишного слоя. Верхний слой формируют из цементно-песчаной смеси. Для удобства можно использовать готовый пескобетон. Консистенция раствора должна напоминать слегка размягченное сливочное масло. Следует избегать излишка жидкости. Рекомендуемое количество воды обычно указано в инструкции по применению.
Монолитность стяжки достигается по прошествии нескольких дней. Для увеличения прочности рекомендуется поддержание влажного состояния в течение месяца. Для этого пол можно слегка обрызгивать водой или просто накрыть полиэтиленовой пленкой.
Стены и перекрытия
Для возведения стен и перекрытий из керамзитобетона используются свои пропорции приготовления раствора.
Обычно смесь для стен имеет следующий состав:
- одна часть цемента;
- полторы части песка;
- одна часть керамзита;
- полторы части воды.
Заливку проще всего производить в съемную опалубку из досок или фанеры. Чтобы опалубка не впитывала влагу из раствора, рекомендуется покрыть деревянные элементы полиэтиленовой пленкой.
Поскольку керамзитобетон не защищен от впитывания влаги, использовать для армирования металлические элементы не рекомендуется, так как возрастает риск их поражения коррозией. В качестве армирующего материала лучше применять стеклопластиковую арматуру и сетку из того же материала.
Наружные стены из керамзитобетона обязательно должны быть защищены с двух сторон гидроизоляционным материалом. Допускается использовать для этих целей толстый слой штукатурки. В продаже можно найти специальные влагостойкие штукатурные смеси, в том числе предназначенные для наружных работ.
Раствор для сооружения перекрытий можно приготовить со следующими пропорциями:
- три части песка;
- одна часть цемента;
- четыре части керамзита;
- полторы части воды.
Для сооружения опалубки потребуются профилированные металлические листы, несущие двутавровые балки, фанера, армирующая сетка. Примерный порядок работы выглядит следующим образом:
В качестве основания будущего перекрытия укладываются несущие балки.
- Поверх балок расстилаются профилированные листы, которые станут дном опалубки.
- Из фанеры изготавливаются боковые стенки опалубки.
- Внутрь опалубки укладывается армирующая стеклопластиковая сетка.
- Приготовленный раствор заливается в опалубку.
Не следует полагаться на визуальное затвердевание материала. Важно помнить, что расчетную прочность бетонные смеси с любыми наполнителями приобретают по прошествии месяца с момента заливки.
Керамзитобетон завоевал большую популярность в строительстве. Основным его преимуществом является малая плотность, позволяющая упростить возведение зданий и уменьшить затраты на изготовление фундамента. Материал довольно универсален, подходит для изготовления блоков и создания монолитных конструкций. Для каждой строительной задачи существуют свои пропорции составления бетонной смеси, которые обеспечивают наилучшие эксплуатационные характеристики. Простота приготовления раствора способствовала широкому распространению самостоятельного изготовления керамзитобетонных блоков.
Сделать полы прочными, ровными и теплыми поможет керамзитобетонная стяжка. В ее основе находится керамзит, который является экологически чистым материалом и представляет собой гранулы, полученные вследствие вспенивания и обжига глины. Керамзит обладает отличными техническими характеристиками, в частности, надежной тепло- и звукоизоляцией. Стяжку пола из керамзитобетона можно сделать без особого труда своими руками, изучив предварительно технологический процесс и подготовив необходимый инвентарь с материалами.
Марка и состав
Стяжка из керамзитобетона сохраняет все плюсы, которыми обладает обычная бетонная, но при этом уменьшает ее недостатки. Керамзитобетон (КБ) получают посредством смешивания воды, цемента, песка и керамзита. Благодаря специальной технологии производства, строительный материал для стяжки пола получается легким, пористым и высококачественным. Он не поддается гниению, коррозии и поэтому его часто выбирают для обустройства стягивания по грунту. В зависимости от состава керамзитоцементных блоков и фракции используемых ингредиентов, различают следующие марки стройматериала, каждая из которых имеет свое назначение:
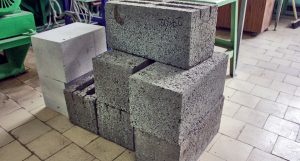
- М300 — применяется в производстве покрытий путей сообщения для передвижения людей и транспортных средств;
- М150 — выпускается для литья блоков;
- М100 — используется для заливки основы под напольное покрытие, которая обеспечивает жесткость и ровность поверхности;
- М50 — применяется для установки внутренних перегородок в жилых домах.
Сильные и слабые стороны
Марка керамзитобетона, подходящая для стяжки пола, обладает множеством плюсов, которые позволяют создать крепкое основание под самый разный тип напольного покрытия.
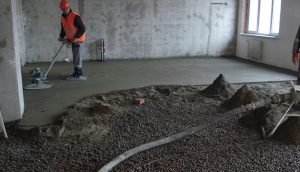
Опытные строители выделяют следующие сильные стороны этого рабочего материала:
- влагостойкость;
- надежность, прочность и долговечность;
- высокий уровень звуко- и теплоизоляции;
- возможность противостоять пламени огня;
- легкий вес;
- способность сопротивляться воздействию отрицательных факторов извне;
- готовый пол после заливки стяжки значительно увеличивается в толщине;
- шероховатая поверхность, которая требует дополнительных операций, а точнее, применения шлифовальных машин.
К тому же, состав керамзитобетона включает только натуральные компоненты, что делает стройматериал экологически чистым и безопасным для человеческого здоровья. Многие застройщики выбирают керамзитобетон и по причине того, что он является идеальной основой для совершенно любого вида напольного покрытия. Но, несмотря на немалое множество преимуществ, имеются у КБ и недостатки.
Подручный инвентарь и материалы
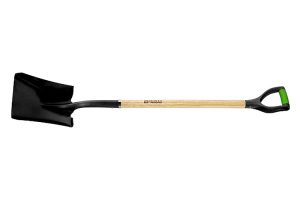
Перед тем, как начать заливать пол керамзитобетоном, строителю нужно подготовить следующее:
- шпахтель;
- перфоратор с насадкой;
- малярный валик;
- кельма;
- линейка строительная;
- емкости пустые;
- перчатки;
- кисточки;
- защитные очки;
- молоток;
- марлевая повязка;
- лопата;
- ватерпас.
Раствор продается готовый в строительном магазине, но также без труда можно изготовить его собственноручно в домашних условиях. Важно только соблюдать пропорции и взять первосортные компоненты. Ведь от качества готовой керамзитобетонной смеси зависит прочность стяжки пола и дальнейшего покрытия.
Пропорции и приготовление
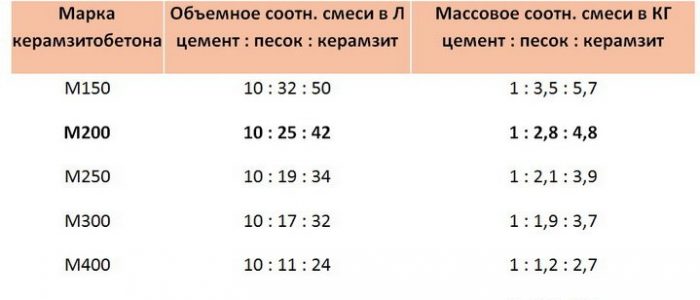
В зависимости от предназначения стяжки, определяется пропорция керамзитобетонного раствора. Так, если нужно обустроить пол в общественных местах, то потребуется отмерить 50 кг керамзита, 45 кг песка и смешать их с бетоном (15 кг). Если толщина керамзитобетонной стяжки в среднем 5 см, то рабочей смеси хватит примерно на 2 м2. Для жилых сооружений рабочую массу готовят из 4 частей гранул обожженной глины, 3 ч. песка и 1 ч. битого камня. Последовательность приготовления раствора следующая:
- В большую емкость высыпать керамзит и залить его необходимым количеством воды.
- Размешать ингредиенты и оставить на время, чтобы гранулы хорошо впитали влагу.
- Слить оставшуюся воду и выгрузить КБ в бетоносмеситель.
- Добавить остальные сухие компоненты.
- Еще раз разбавить водой и тщательно размешать.
Как заливать: способы
Правильность укладки мокрой прослойки
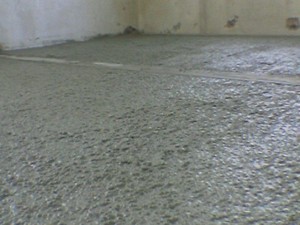
Проводить напольную стяжку можно различными вариантами, и если не важна теплоизоляция, то можно прибегнуть к мокрому способу. Потребуется замесить раствор в соответствующих пропорциях, вылить его на подготовленную поверхность с установленными маяками и очищенную от мусора и старого покрытия, и разровнять правилом. Такая стяжка не утеплит пол, но существенно сэкономит физическую силу и время на строительные работы.
Осуществлять мокрую стяжку из керамзитобетона нужно сразу на всю площадь, избегая длительных перерывов, поэтому весь объем раствора должен быть подготовлен заранее.
Полусухой метод
Если нужно приподнять уровень пола, сделать теплее или повысить его теплоизоляционные свойства, то, как нельзя, кстати, окажется стяжка основания из КБ и пескоцемента, которая осуществляется в 2 этапа. Изначально пол засыпают сухим керамзитовым гравием ниже уровня чернового пола на 20 мм, после чего проливают его цементным молоком, которое надежно скрепит гранулы между собой. Спустя 24 часа первый ряд заливают бетонным раствором, разравнивают, оставляют сохнуть и набираться прочности. Чтобы не допустить растрескивания бетона, в процессе высыхания уложенный пол нужно регулярно поливать водой. К тому же, опытные застройщики советуют накрывать его пленкой для лучшего сохранения влаги.
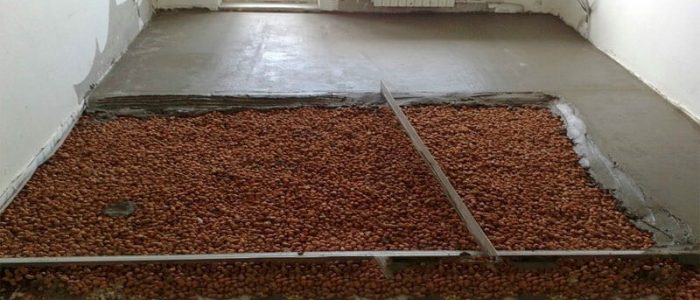
Простой вариант — сухой
На подготовленную напольную поверхность высыпают керамзитовый гравий и накрывают сверху гипоскартоном либо фанерой. Чтобы хорошенько закрыть швы, настил лучше делать в 2 слоя. Такой способ довольно простой и начинающие строители с легкостью справятся с ним. Сухая стяжка не предполагает использование цемента, что существенно экономит бюджет и время на строительные работы.
Завод по производству ГРП песка / керамзита
Керамический песок — это разновидность керамической частицы, которая имеет высокую интенсивность разрушения, в основном используется для нефтяных месторождений в качестве скважинного проппанта. Используется для увеличения выхода нефти и газа. Поэтому керамический песок является разновидностью экологически чистых и экологически чистых продуктов. Керамический песок, изготовленный из высококачественного боксита и других добавок, гранулирует и кальцинирует для повышения прочности и плотности. Он заменяет природный кварцевый песок, стеклянный песок, металлический песок и другие проппанты низкой интенсивности. Керамический песок — лучший проппант для увеличения добычи нефти и природного газа.Вкратце, процесс изготовления керамического песка представляет собой дробление → дозирование → измельчение → гранулирование → прокаливание охлаждение → грохочение упаковки
Ниже приводится описание процесса керамического песка:
1 . Дробление Размер бокситов из шахты составляет около 300 ~ 500 мм, низкая влажность. После двухэтапного дробления, которое состоит из щековой дробилки и молотковой дробилки, размер боксита будет около 25 мм.
2.Дозирование боксита, порошка марганца и другого дополнительного материала будет передано на ленточный конвейер через ленточный весовой дозатор , чтобы убедиться, что подходящая пропорция. Если влажность боксита или другого материала составляет более 6%, необходимо сначала высушить.
3. Измельчение В процессе измельчения основным оборудованием является шаровая мельница и сепаратор для изготовления системы измельчения с замкнутым контуром . Для гранулятора требуется, чтобы размер материала был меньше 300 мес.
4.Гранулятор Порошок сырья после измельчения хранится в бункерах. Обычно имеется 2-3 бункера, его можно выгружать отдельно, а также можно разгрузить вместе с несколькими бункерами. Порошок сырья будет перенесен в небольшой бункер, в бункере есть шнековое дозирующее устройство или ленточный весовой дозатор. Материал будет транспортироваться в гранулятор , а вода будет распыляться в гранулятор с помощью трубопровода. Когда гранулятор вращается, сырье может быть превращено в частицы различного размера. Сырой керамический песок будет транспортироваться во вращающийся сит с помощью ленточного конвейера, квалифицированный песок будет прокаливаться во вращающейся печи, а избыточный размер возвращается в процесс измельчения сырья.Система гранулятора полностью автоматическая, непрерывно, в сочетании с пылесборником мешочного типа, может очищать отработанный воздух. . песок будет прокален в керамический песок с высокой интенсивностью во вращающейся печи .
6.Подготовка пылевидного угля Для приготовления пылевидного угля используют шаровую мельницу или вертикальную мельницу , которая может сушить уголь горячим ветром из колпака печи. Использование сепаратора позволяет регулировать тонкость измельченного угля по желанию; это обеспечивает достаточные условия для полного сжигания пылевидного угля.
7. Охлаждение мелкозернистого продукта Для охлаждения керамического песка обычно используется роторный охладитель , он прост и надежен при работе, вторичный воздух охладителя абсолютно поступает в печь, многоканальная горелка, может сэкономить много энергии.Температура керамического песка после охладителя очень низкая, можно дотронуться рукой.
8. Экран Песок Ceramin, после того как охладитель можно напрямую транспортировать на многоступенчатый вибрационный грохот, можно разделить на множество частиц в соответствии с требованиями.
Керамический песок Спецификация
Модель 1: 0,45-0,9 мм (20 меш — 40 меш), высокая интенсивность и средняя плотность
Модель 2: 0.9-1,25 мм (16 меш — 20 меш) высокой интенсивности и средней плотности
Модель 3: 1,0-1,70 мм (12 меш — 18 меш) высокой интенсивности и средней плотности
Модель 4: 0,224-0,65 мм (40 меш — 60 меш) высокой интенсивность и средняя плотность
9. Упаковка Керамический песок после сортировки будет транспортироваться в разные бункеры, бункеры, связанные с упаковочной машиной, готовая продукция будет отправляться на склад для подготовки к отправке. Все точки пыли в процессе должны совпадать с пылесборником для очистки отработанного воздуха.
Термообработанные низкокачественные каолиновые глины в настоящее время считаются подходящим пуццолановым материалом для метакаолинов. Однако их пригодность в качестве хорошего пуццоланового материала зависит от геохимии и структуры глины, на которую обычно влияет географическая среда. В этом исследовании изучалась низкосортная каолиновая глина из Ньямебекере в регионе Ашанти, Гана. Было проанализировано влияние прокаленного материала на раннее и позднее развитие прочности портландцемента.Ранняя 3- и 7-дневная прочность, а также поздняя 28-дневная прочность портландцемента, замененного на 20% по массе прокаленного материала, дали оптимальные значения прочности. Дальнейший анализ с использованием твердотельного магнитно-углового спин-ядерного магнитного резонанса (Ss MAS ЯМР) зондируют в среду алюминия (Al) для обнаружения присутствия и природы гидратов алюминия с использованием оптимальной пропорции смеси. Результаты ЯМР Ss MAS показали, что повышение прочности оптимальной смеси было обусловлено ростом стабильных моносульфатных соединений в октаэдрической среде в результате метастабильных алюминатных фаз в тетраэдрической среде.Для большей надежности показателей прочности бетона в исследовании рекомендуется использовать 20% кальцинированной глины из глины Ньямебекере в качестве замены портландцемента.
1. Введение
Портландцемент является важным строительным материалом, который поддерживает бетонную промышленность для развития инфраструктуры и жилых районов. Бетон является вторым наиболее широко потребляемым материалом после воды. Исследования показали, что не только портландцемент используется для приготовления прочного бетона, но также возможна смесь между портландцементом и дополнительными цементными материалами (SCM).SCM, которые использовались в бетоне, включают пуццолановые материалы, такие как летучая зола, шлак, кремнезем и метакаолин [1–3]. Обычно СКМ используются для замены от 20% до 40% портландцемента по весу. Известно, что использование SCM в качестве частичной замены цемента повышает прочность бетонов, а также повышает долговечность бетона при минимизации стоимости цемента.
Метакаолины — это СКМ, получаемые при прокаливании высококачественных каолиновых глин [4, 5]. Высококачественные каолиновые глины имеют ограниченное количество на земной коре.Это делает метакаолин дорогим строительным материалом. Однако земная кора содержит огромное количество каолиновых глин среднего и низкого качества. Высококачественные каолиновые глины — это глины с содержанием каолинита более 65%, в то время как у среднего и низкого сортов содержание каолинита составляет от 40% до 65% и ниже 40% соответственно [6, 7]. Доступность низкосортных каолиновых глин по сравнению с высокосортными глинами привлекла внимание исследователей к разработке пуццоланов из глин такой природы.Авторы, в том числе Фернандес и соавт. [8], He et al. [9] и Maia et al. [4] показали, что кальцинированные низколегированные каолиновые глины улучшают прочность и долговечность бетонов лучше, чем бетоны из портландцемента. Однако реакционная способность этих прокаленных глин зависит от географического положения, что также влияет на их структуру и химический состав. Различия в структуре и химическом составе глины из определенного местоположения обеспечивают необходимость исследований региональных или местных глинистых материалов в качестве подходящего СКМ.
Глины очень распространены в Гане; однако их обработка и использование в качестве пуццолана остаются проблемой [10]. Уже есть некоторые существующие работы в Гане от Atiemo [11] и Bediako и Atiemo [12], которые использовали глину Mankranso, Hwereso и Mfensi для производства пуццолана. Все эти упомянутые области в Гане имеют огромные запасы глины. Получение пуццолана из глины осуществляется путем прокаливания глины при температуре от 600 до 900 ° C [13]. Эта работа направлена на получение глиняного пуццолана из глины, полученной из Ньямебекере в регионе Ашанти, Гана.Этот район, Ньямебекере, представляет собой небольшое фермерское сообщество в Гане с изобилием глины, которое еще предстоит определить количественно. Основной целью исследования является изучение влияния обожженной глины Нямебекьере на ранние и прочностные свойства портландцементных растворов. Анализ прочности на сжатие был по
.Линия по производству легкого керамзитобетонного оборудования
Керамический песок — это разновидность керамической частицы, которая имеет высокую интенсивность разрушения, в основном используется для нефтяных месторождений в качестве скважинного расклинивающего наполнителя. Используется для увеличения выхода нефти и газа. , Поэтому керамический песок является разновидностью экологически чистых и экологически чистых продуктов. Керамический песок, изготовленный из высококачественного боксита и других добавок, гранулирует и кальцинирует для повышения прочности и плотности.Он заменяет природный кварцевый песок, стеклянный песок, металлический песок и другие проппанты низкой интенсивности. Керамический песок — лучший проппант для увеличения добычи нефти и природного газа. Вкратце, процесс изготовления керамического песка представляет собой дробление → дозирование → измельчение → гранулирование → прокаливание, охлаждение → просеивание упаковки.
Ниже приводится описание процесса керамического песка:
1. дробление Размер бокситов из шахты составляет около 300 ~ 500 мм, низкая влажность. После двухэтапного дробления, которое состоит из щековой дробилки и молотковой дробилки, размер боксита будет около 25 мм.
2. Дозирование Боксита, порошка марганца и другого дополнительного материала будет передано на ленточный конвейер через ленточный весовой дозатор, чтобы убедиться, что соответствующая пропорция. Если влажность боксита или другого материала составляет более 6%, необходимо высушить при первый .
3. Измельчение В процессе измельчения основным оборудованием является шаровая мельница и сепаратор для создания системы измельчения с замкнутым контуром. Для гранулятора требуемый размер материала будет меньше, чем 300 меш.
4. Гранулятор Порошок сырья после измельчения хранится в бункерах. Обычно имеется 2-3 бункера, он может быть выгружен отдельно, а также может быть выгружен вместе со многими бункерами. Порошок сырья будет перенесен в небольшой бункер, в бункере есть шнековое дозирующее устройство или ленточный весовой дозатор. Материал будет подаваться в гранулятор, а вода будет распыляться в гранулятор с помощью трубопровода. Когда гранулятор вращается, сырье может быть превращено в частицы различного размера. Сырой керамический песок будет транспортироваться во вращающийся сит с помощью ленточного конвейера, квалифицированный песок будет прокаливаться во вращающейся печи, а избыточный размер возвращается в процесс измельчения сырья.Система гранулятора полностью автоматическая, непрерывно, в сочетании с пылесборником мешочного типа, может очищать отработанный воздух. . песок будет прокален в керамический песок с высокой интенсивностью во вращающейся печи.
6.Подготовка пылевидного угля Для приготовления пылевидного угля используют шаровую мельницу или вертикальную мельницу, которая может сушить уголь горячим ветром из колпака печи. Использование сепаратора позволяет регулировать тонкость измельченного угля по желанию; это обеспечивает достаточные условия для полного сжигания пылевидного угля.
7. Охлаждение мелкозернистого продукта Для охлаждения керамического песка обычно используют роторный охладитель, он прост и надежен при работе, вторичный воздух охладителя абсолютно попадает в печь, многоканальная горелка, может сэкономить много энергии.Температура керамического песка после охладителя очень низкая, можно дотронуться рукой.
8. Экран Ceramin sand после того, как охладитель может быть непосредственно транспортирован на многоступенчатый вибрационный грохот, его можно разделить на множество частиц в соответствии с требованиями.
Керамический песок Спецификация
Модель 1: 0,45-0,9 мм (20 меш — 40 меш) высокой интенсивности и средней плотности
Модель 2: 0,9-1,25 мм (16 меш — 20 меш) высокой интенсивности и средней плотности
Модель 3: 1,0 -1.Высокая интенсивность 70 мм (12 меш-18 меш) и средней плотности
Модель 4: Высокая интенсивность 70 мм (40 меш-60 меш) и средняя плотность
9. Упаковка Керамический песок после просеивания будет транспортироваться в разные бункеры, силосы, связанные с упаковкой Машина, готовая продукция будет передана на склад для подготовки к доставке. Все точки пыли в процессе должны совпадать с пылесборником для очистки отработанного воздуха.
Мы можем предоставить комплексные технологические решения и комплектное производственное оборудование для завода по производству керамического песка мощностью 10000-30000 тонн в год.Наш профессиональный инженер может сделать проект в соответствии с ситуацией проекта, чтобы сэкономить энергопотребление на 35%.
ООО «Горное машиностроение Хэнань Чжэнчжоу» расположено в промышленном парке Улун города Чжэнчжоу Синъян, который является столицей провинции Хэнань. Он находится на пересечении улиц 310 State
Road и Xingmi Road, недалеко от шоссе, железнодорожного вокзала, West Zhongyuan Road, центральной части города Чжэнчжоу и международного аэропорта Чжэнчжоу. Условия перевозки
очень удобно.Основная продукция компании: шаровая мельница, вращающаяся печь, вертикальный подогреватель, охладитель, дробилка, металлургическая коксовая печь, магнитный сепаратор, флотационная машина, классификатор, питатель
, ковшовый элеватор, подогреватель, пылесборник, элеватор, сушилка и др. оборудование относится к области металлургии, цемент, известь, переработке полезных ископаемых, огнеупорной, химической промышленности.
Продукция Henan Zhengzhou Mining Machinery Co., Ltd была продана в каждую провинцию Китая и экспортирована в Россию, Корею, Вьетнам, Малайзию, Непал, Бангладеш, Мексику,
, Армению, Африку, Южную Америку и другие страны, а также регионы.
Для того, чтобы дать вам ответственное предложение, вы можете сообщить нам следующую информацию:
1. С каким материалом вы будете иметь дело?
2. Какова зернистость материала?
3. Какую гранулярность конечных продуктов вы собираетесь достичь?
4. Каких производственных мощностей вы собираетесь достичь?
Свяжитесь с нами
Henan Zhengzhou Mining Machinery Co.,
Адрес
Промышленная зона Цяолу-Цайчжоу, город Синъян, провинция Хэнань, Китай (материк)
Наши инженеры предложат вам наиболее подходящий по вашей информации.
,
Линия по производству легкого керамзитового заполнителя
Керамический песок — это разновидность керамических частиц, которая имеет высокую интенсивность разрушения, в основном используется для нефтяных месторождений в качестве скважинного расклинивающего наполнителя. Используется для увеличения выхода нефти и газа. Поэтому керамический песок является разновидностью экологически чистых и экологически чистых продуктов. Керамический песок, изготовленный из высококачественного боксита и других добавок, гранулирует и кальцинирует для повышения прочности и плотности.Он заменяет природный кварцевый песок, стеклянный песок, металлический песок и другие проппанты низкой интенсивности. Керамический песок — лучший проппант для увеличения добычи нефти и природного газа. Вкратце, процесс изготовления керамического песка представляет собой дробление → дозирование → измельчение → гранулирование → прокаливание, охлаждение → просеивание упаковки.
Ниже приводится описание процесса керамического песка:
1. дробление Размер бокситов из шахты составляет около 300 ~ 500 мм, низкая влажность. После двухэтапного дробления, которое состоит из щековой дробилки и молотковой дробилки, размер боксита будет около 25 мм.
2. Дозирование Боксита, порошка марганца и другого дополнительного материала будет передано на ленточный конвейер через ленточный весовой дозатор, чтобы убедиться, что соответствующая пропорция. Если влажность боксита или другого материала составляет более 6%, необходимо высушить при первый .
3. Измельчение В процессе измельчения основным оборудованием является шаровая мельница и сепаратор для создания системы измельчения с замкнутым контуром. Для гранулятора требуемый размер материала будет меньше, чем 300 меш.
4. Гранулятор Порошок сырья после измельчения хранится в бункерах. Обычно имеется 2-3 бункера, он может быть выгружен отдельно, а также может быть выгружен вместе со многими бункерами. Порошок сырья будет перенесен в небольшой бункер, в бункере есть шнековое дозирующее устройство или ленточный весовой дозатор. Материал будет подаваться в гранулятор, а вода будет распыляться в гранулятор с помощью трубопровода. Когда гранулятор вращается, сырье может быть превращено в частицы различного размера. Сырой керамический песок будет транспортироваться во вращающийся сит с помощью ленточного конвейера, квалифицированный песок будет прокаливаться во вращающейся печи, а избыточный размер возвращается в процесс измельчения сырья.Система гранулятора полностью автоматическая, непрерывно, в сочетании с пылесборником мешочного типа, может очищать отработанный воздух. . песок будет прокален в керамический песок с высокой интенсивностью во вращающейся печи.
6.Подготовка пылевидного угля Для приготовления пылевидного угля используют шаровую мельницу или вертикальную мельницу, которая может сушить уголь горячим ветром из колпака печи. Использование сепаратора позволяет регулировать тонкость измельченного угля по желанию; это обеспечивает достаточные условия для полного сжигания пылевидного угля.
7. Охлаждение мелкозернистого продукта Для охлаждения керамического песка обычно используют роторный охладитель, он прост и надежен при работе, вторичный воздух охладителя абсолютно попадает в печь, многоканальная горелка, может сэкономить много энергии.Температура керамического песка после охладителя очень низкая, можно дотронуться рукой.
8. Экран Ceramin sand после того, как охладитель может быть непосредственно транспортирован на многоступенчатый вибрационный грохот, его можно разделить на множество частиц в соответствии с требованиями.
Керамический песок Спецификация
Модель 1: 0,45-0,9 мм (20 меш — 40 меш) высокой интенсивности и средней плотности
Модель 2: 0,9-1,25 мм (16 меш — 20 меш) высокой интенсивности и средней плотности
Модель 3: 1,0 -1.Высокая интенсивность 70 мм (12 меш-18 меш) и средней плотности
Модель 4: Высокая интенсивность 70 мм (40 меш-60 меш) и средняя плотность
9. Упаковка Керамический песок после просеивания будет транспортироваться в разные бункеры, силосы, связанные с упаковкой Машина, готовая продукция будет передана на склад для подготовки к доставке. Все точки пыли в процессе должны совпадать с пылесборником для очистки отработанного воздуха.
Мы можем предоставить комплексные технологические решения и комплектное производственное оборудование для завода по производству керамического песка мощностью 10000-30000 тонн в год.Наш профессиональный инженер может сделать проект в соответствии с ситуацией проекта, чтобы сэкономить энергопотребление на 35%.
ООО «Горное машиностроение Хэнань Чжэнчжоу» расположено в промышленном парке Улун города Чжэнчжоу Синъян, который является столицей провинции Хэнань. Он находится на пересечении улиц 310 State
Road и Xingmi Road, недалеко от шоссе, железнодорожного вокзала, West Zhongyuan Road, центральной части города Чжэнчжоу и международного аэропорта Чжэнчжоу. Условия перевозки
очень удобно.Основная продукция компании: шаровая мельница, вращающаяся печь, вертикальный подогреватель, охладитель, дробилка, металлургическая коксовая печь, магнитный сепаратор, флотационная машина, классификатор, питатель
, ковшовый элеватор, подогреватель, пылесборник, элеватор, сушилка и др. оборудование относится к области металлургии, цемент, известь, переработке полезных ископаемых, огнеупорной, химической промышленности.
Продукция Henan Zhengzhou Mining Machinery Co., Ltd была продана в каждую провинцию Китая и экспортирована в Россию, Корею, Вьетнам, Малайзию, Непал, Бангладеш, Мексику,
, Армению, Африку, Южную Америку и другие страны, а также регионы.
Для того, чтобы дать вам ответственное предложение, вы можете сообщить нам следующую информацию:
1. С каким материалом вы будете иметь дело?
2. Какова зернистость материала?
3. Какую гранулярность конечных продуктов вы собираетесь достичь?
4. Каких производственных мощностей вы собираетесь достичь?
Свяжитесь с нами
Henan Zhengzhou Mining Machinery Co.,
Адрес
Промышленная зона Цяолу-Цайчжоу, город Синъян, провинция Хэнань, Китай (материк)
Наши инженеры предложат вам наиболее подходящий по вашей информации.
,