Cтолешница из эпоксидной смолы своими руками: техноология изготовления
Главная » Мебель » Столешница из эпоксидной смолы — делаем оригинальный стол
Некоторые строительные материалы находят применение в других областях. Так обычная штукатурка превратилась в художественную или декоративную. Из нее даже панно теперь делают. Другой такой пример — эпоксидная смола. Из нее делают очень красивую и нестандартную мебель. В частности, столы, барные стойки, стулья. Вот только ценник совсем негуманный, но очень красиво. Как выяснилось, технология не так сложна, хоть есть много тонкостей. Но сделать стол из эпоксидной смолы и дерева своими руками вполне реально.
Подготовка древесины
Содержание статьи
Выбор древесины для столешницы из эпоксидной смолы — целое дело. Чем ярче проявляется древесный рисунок, тем интереснее будет результат. Но древесина должна быть выдержанной, сухой. И спилы нужны немалой толщины, с интересными краями. По сути, это необрезная доска, но дорогих пород древесины. Чтобы не путать со строительным материалом называют такие спилы — слэб и должны они быть камерной сушки.

Можно даже камень использовать как основу
Получив древесину, надо придумать как ее разложить. Столешница может быть собрана из нескольких досок «с рекой» из эпоксидки между ними. Края при этом могут быть из смолы или из древесины. Массив может располагаться с одной стороны, вторая будет прозрачной. Можно использовать круглые плашки, которые получаются при распиливании толстых и не очень деревьев. Если нет древесины с красивым краем (или она слишком дорога), рельеф можно сделать вручную — фрезером. Если доски узкие, их склеиваем, сажая на шканты. В общем, возможностей масса.

Такой вот стол из эпоксидной смолы сделан из двух досок карагача (вяза)
После того как придумали, как все будет выглядеть, начинаем обработку древесины. Надо снять кору, удалить дефекты. Дефекты — сухие и раскрошенные сучки, дырочки, которые прогрызли насекомые, сколы, трещины. Если где есть гниль или «синева», убираем фрезером до чистого дерева. В общем, все очищаем, шлифуем, сохраняя природную форму или добавляя рельефа в меру фантазии и способностей. Плоскость доски тоже шлифуем, обнажая древесный рисунок, при желании подчеркивая его. Использовать можно любые средства. Ту же морилку, масло для древесины, можно обжечь лампой, после отшлифовать, используя проволочную щетку и т.д.

Грунтовка древесины нужна, если не хотите видеть пузырьки в смоле
Перед основной заливкой надо древесину «прогрунтовать» той эпоксидной смолой, которую будете использовать в работе. Заливаем сначала все небольшие каверны, отверстия, которые обнаружили при зачистке. Залили и на протяжении двух-трех часов периодически прогреваем залитые участки. Из каверн, пор древесины выходит воздух. Если смолу не греть, останутся пузыри в толще смолы. Если вы хотите добиться прозрачности, пузыри надо удалять. Вот их и греем. После высыхания залитые участки шлифуем, выравнивая в плоскость с доской. Затем тонким слоем смолы покрываем доску полностью — стабилизируем ее, попутно выгоняя воздух из пор.
Создание формы для заливки
После того как древесину подготовили, залили ее тонким слоем состава, пока она сохнет, приступаем к созданию формы. В ней надо будет разместить деревянную заготовку. По размерам форма может быть как впритык по длине с доской, так и больше. Во втором варианте по краям будут полоски эпоксидки.
Для создания формы подойдет любой листовой материал с гладкой поверхностью. Чем более гладкой будет форма, тем меньше усилий потребует шлифовка. Форму собирают с бортиками, которые на несколько сантиметров выше планируемой толщины столешницы. После сборки стыки герметизируют герметиком, который нужно тщательно выровнять. Оборачиваем палец пищевой пленкой, смачиваем в воде и заглаживаем до идеального состояния. Но делать это надо быстро. Герметизация должна быть тщательной, иначе смола потечет из формы. А она далеко не дешевая, да и следы убирать непросто.

Если есть струбцины, можно плашки зафиксировать с их помощью, а не использовать груз
Можно сделать форму из ламинированного ДСП, а можно из фанеры, но ее надо будет обязательно чем-то покрыть. Например, воском, специальным разделительным составом. Самый простой и дешевый вариант — обтянуть пленкой, но она должна лечь гладко, без каких-либо волн и неровностей. Можно заклеить скотчем в два слоя. Клеить стык в стык, без захлестов. Второй ряд клеим сдвинув так, чтобы швы нижнего ряда были перекрыты лентами примерно на середине длины. Скотч тоже должен ложиться гладко. Его можно заменить виниловой пленкой, но надо будет подогревать в углах, чтобы легла ровно.
Можно сделать форму из стекла, посадив бортики на герметик. Для более легкого отделения стекло смазать слоем жира. Не пренебрегайте смазкой — будет намного меньше проблем. В общем и целом, делая стол из эпоксидной смолы даже на подготовительных процессах можно включать фантазию. Технология очень гибкая, вариантов множество.
Какую эпоксидную смолу использовать для изготовления столешниц
Эпоксидных смол очень много и разброс по ценам солидный. Сразу скажем, что для нормального результата дешевая не подойдет. Нужна прозрачная, которая со временем не мутнеет, не меняет цвет, а это дорогие составы, например, 3D MG-EPOX-STRONG. Часто они выделены в отдельную категорию: эпоксидные смолы для столешниц. При выборе надо обратить внимание на такие параметры:
- Минимальный слой.
- Максимальный слой.
- Время до заливки второго слоя.
- Время до окончательного высыхания.

Для этого стола из древесины и эпоксидной смолы была использована Crystal 76. Ушло 10 литров (на речку и залитую щель у стены)
Дело в том, что есть смолы, которые за один раз заливать можно только небольшим слоем. Скажем, максимальный слой 10 мм. И следующий слой можно заливать через 24 часа. Если надо сделать столешницу толщиной 6-7 мм (4 см древесина, плюс по 1-1,5 мм снизу и сверху), понадобится целая неделя. И это только, чтобы залить послойно. Есть эпоксидные смолы, которые можно заливать слоем до 6 см и более.
Если делать стол из эпоксидной смолы собираетесь впервые и с этим материалом дел ранее не имели, лучше выберите те, которые наливаются тонким слоем. С ними проще добиться отсутствия пузырьков. Хотя, возможно, вам нравится эффект «застывшей газировки». Если желаете смолу подкрасить, надо покупать специальные красители. При послойной заливке краситель разводят в одном из компонентов до добавления отвердителя. Так цвет получится однородным.
Сколько нужно смолы
Сколько нужно эпоксидной смолы для стола? Ответить непросто. Столешница может быть разного размера, может быть малой или большой толщины. Может будет только небольшая «река», а возможно большая часть будет именно из эпоксидки. В принципе, можно примерно посчитать объем столешницы, который вы планируете сделать. Прикинуть, сколько в процентном соотношении будет занимать древесина, остальное — эпоксидная смола. Так что сколько нужно эпоксидной смолы для стола считаем для своего случая сами. У одних, которые делают только «реку» пойдет 4-6 литров, у других может требоваться 20-30 литров или больше.

На изготовление этого журнального столика из эпоксидной смолы и дерева ушло 12 литров эпоксидки
Давайте рассмотрим пример. Будем делать прямоугольную столешницу размером 100*60 см, толщина — 7 см. Большую часть займет древесина — примерно на 2/3. Переводим величины в метры и перемножаем: 1,0 х 0,6 х 0,07 = 0,042 м³. Чтобы перевести в литры эту цифру умножаем на 1000. Получаем 42 литра. Вот так немало. Но это если делать столешницу полностью из эпоксидной смолы. Примерно 2/3 объема будут заняты древесиной. На долю эпоксидки придется всего 1/3. То есть, полученную цифру делим на 3 и получаем 14 литров. То есть, для изготовления столика 100*60 см потребуется порядка 14-15 литров эпоксидной смолы.
Технология заливки эпоксидной смолы на столешницу
В подготовленную форму выложили деревянную основу стола. Поставили на него груз, чтобы древесина плотно прижалась к основанию. Чем меньше ее затечет между деревяшкой и основанием, тем меньше будет расход.
Эпоксидная смола — двухкомпонентный состав. Состоит из смолы и отвердителя. Если хотите сделать эпоксидку цветной, добавляем несколько капель красителя в смолу и перемешиваем до однородного цвета. Переливаем в другую тару и повторяем перемешивание. Если этого не сделать, по краям, на дне останутся непрокрашенные полосы, которые будут видны. Закончив перемешивание, отливаем нужное количество затонированной смолы в отдельную емкость, добавляем отвердитель, перемешиваем в течение нескольких минут. Выливаем в форму.

На такой стол надо много смолы
Первый слой — базовый. Часть все равно затекает под древесину. Он не должен быть меньше минимально допустимого. Смола текучая и выравнивается сама, но не стоит лить ее в одном месте. Лучше более-менее равномерно распределить по всей поверхности. Выжидаем положенное время до нанесения следующего слоя и операцию повторяем. Так до тех пор, пока не получим нужную толщину.
Как залить без пузырьков
В принципе, есть эпоксидная смола, которая мало подвержена образованию пузырьков — из серии Арт-Массив. Но пузырьки появляются из древесины. Если вы ее предварительно не покрыли тонким слоем смолы, их будет больше. Если обработали — меньше. Но будьте готовы к тому, что они будут. Поэтому для первого раза и советуем использовать нанесение смолы тонкими слоями. Так проще добиться отсутствия пузырей.

Смола может быть непрозрачной
Вся хитрость в том, чтобы в течение двух-трех часов после заливки прогревать смолу. Так пузырьки будут выходить на поверхность. Можно использовать для этих целей строительный фен. Некоторые применяют газовые горелки, но открытый огонь и эпоксидная смола — опасное сочетание. Лучше, все-таки, фен. Итак, после заливки каждого слоя прогреваем его при помощи фена.
Полировка и доведение до глянцевого блеска
После окончательного твердения стол из эпоксидной смолы и дерева требует полировки. Смола не выглядит прозрачной — это нормально, не расстраивайтесь. Если вы заливали прозрачный компаунд, таким он и будет. Но нужна тщательная шлифовка. Для начала лучше использовать ленточную — она захватывает больше площади, для финиша больше подходит эксцентриковая. Но можно и болгаркой с регулировкой скорости и соответствующей насадкой справиться.
Зерно берем сначала крупное, затем все мельче и мельче. Если есть более-менее значительные перепады, начинаем с 80 или 100, затем шаг за шагом уменьшаем зерно. Финишное доведение — уже 1000, 1500 и 2000. Не все смолы одинаково хорошо полируются. Если даже после использования 2000 шкурки блеска недостаточно, пробуйте полироли для автомобилей, фар. Можно сделать самодельную полировочную пасту: паста гои + солидол. И растирать сначала ветошью, а заполировать мягкой насадкой для полировки.

Можно не выравнивать рельеф, а только покрыть слоем эпоксидной смолы
Добиться блеска можно не только полировкой. Это не значит, что шлифовать не надо. Надо. Но если блеска недостаточно, а поверхность уже гладкая, можно столешницу покрыть глянцевым лаком и лучше на водной основе. И еще лучше — яхтный. Тогда поверхность не будет бояться влаги и горячего. Покрывать лаком как обычно — в несколько слоев. Промежуточная шлифовка вряд ли нужна, разве что сделали лужи или мусор попал. Шлифовать уже последний слой до нужной степени глянца.
Варианты другого заполнения
Стол из эпоксидной смолы и дерева не обязательно делать только из дорогого слэба. Отлично можно приспособить радиальные спилы деревьев. И радиус тут далеко не главное. Можно из древесины сделать раму, которую установить на столешницу — на фанеру 10 мм или около того. В эту раму выложить спилы — по рисунку или хаотично. В таком случае столешницу не надо будет снимать с основы — это самый простой вариант. Для самостоятельного изготовления в первый раз — самое простое решение.

Сделать стол из спилов дерева и эпоксидной смолы можно в разных видах
Обратите внимание, что древесину лучше выбирать с изъянами. В данном случае это не дефекты, а изюминка. Трухлявые так вообще выглядят экзотично. Особенно если подчеркнуть разницу цветов и фактур используя глубокий цвет.

Авторская мебель из дерева и эпоксидной смолы. Второй такой же точно нет
Очень интересный эффект при использовании не только тонировки, но и разных добавок. Например, блесток, порошка, который дает эффект металлика, даже битое цветное стекло или зеркальные осколки дают очень интересную картинку.

Использование жемчужного порошка с затонированной древесиной
Вместо древесины использовать можно камень. Вес такого стола будет солидным, но и прочность тоже ого-го. Отлично смотрятся слоистые породы. Желательно иметь навыки работы с камнем. Это посложнее, чем шлифовка древесины. При подготовке, надо хорошо заливать пустоты, чтобы вышел весь воздух.

Стол из эпоксидной смолы и камня
Используют гальку, натуральный или покрашенный гравий. Эти камни можно выкладывать довольно толстым слоем — смола все равно затечет в промежутки. Часто встречается в комбинации с древесиной. Кстати, если вы «промахнулись» с количеством эпоксидной смолы, можно в залитую смолу добавить камушки. Так можно добрать нужный уровень.

Галька, гравий тоже идут в ход
Фантазия человека безгранична. Делают мебель из эпоксидки, заливая разные железки. Детали автомобилей, гаечные ключи, велосипедные или мопедные цепи и т.д.

Металл тоже идет в ход
По тому же принципу можно сделать и стулья или табуретки. Можно отлить в том же стиле ножки-тумбы. Стали уже даже светодиодные гирлянды заливать в эпоксидку. Чем не ночная лампа или ножка с мягкой подсветкой. Есть, кстати, светящиеся в темноте добавки в эпоксидную смолу.

Можно и как стулья использовать, и как опору для столешницы
Столы и столешницы из эпоксидной смолы. Советы по изготовлению.
Столы и столешницы из эпоксидной смолы. Советы по изготовлению.Стол-река, стол из спилов и просто столешницы из эпоксидной смолы с декоративным наполнением.
Вот такие разные, но очень популярные в последнее время виды столешниц.
Многие готовы попробовать создать такой шедевр самостоятельно.
А мы готовы вам помочь в этом вопросе.
И так, с чего начать?
Какую выбрать эпоксидку?
Если вы уже определились с типом, видом, дизайном будущей столешницы, теперь важно определиться с выбором эпоксидной смолы.
Эпоксидная смола для заливки столешницы должна быть прозрачная и иметь продолжительное время жизни, в противном случае вы рискуете воочию увидеть «кипение смолы» или потратить в разы больше времени на послойную заливку. Смолы конструкционные, базовые (такие как ЭД-20) здесь не уместны, т.к. они более густые, что не позволит выйти всем пузырькам воздуха, более хрупкие, не всегда бесцветные (1 сорт), а отвердители, которые используют с такими смолами (пэпа. тэта и т.п) дадут вам смесь с недостаточным временем жизни, что опять же может грозить как деформацией изделия при быстром отверждении, так и закипанием смеси.
Из представленных в нашем магазине смол, вам подойдет состав ЭпоксиМастер 2.0, позволяющий заливать слои до 5 см одним слоем.
Состав обладает низкой вязкостью, обеспечивает хорошую текучесть и заполнение труднодоступных участков, а умеренная реакционная способность позволяет работать с объектами большого размера. К тому же у состава ЭпоксиМастер прекрасное самовыравнивание, стойкость к отслаиванию и образованию трещин, хорошая наполняемость и отсутствует эффект «выбеливания» покрытия.
Благодаря прозрачности состава вы сможете добиться практически любого визуального эффекта: залить различные наполнители (ракушки, сухие листья, камни, картинки и прочее), сможете организовать подсветку как в толще столешницы, так и под ней, можно реализовать творческую задумку с люминофором или заколеровать смолу, сохранив при этом общую прозрачность слоя.
Подготовка к работе
Помещение должно быть хорошо проветриваемым, либо иметь принудительную вентиляцию. В помещении температура воздуха не должна быть ниже 22 °С. Испортить работу может высокая влажность и пыль!!!
Необходимо подготовить материалы для изготовления опалубки. Опалубку или форму можно собрать из фанеры, оргстекла (без царапин и сколов) или полированных алюминиевых листов. Так же вам понадобятся разделительные составы, например воск или полупостоянные разделители. Для «домашнего» применения лучше воск. А если вы планируете серию столешниц, тогда лучше полупостоянные разделители, они позволяют совершать более 20 съемов без восстановления разделительного слоя.
Некоторые домашние умельцы, в качестве разделителя используют обычный косметический вазелин. Его легко приобрести, но, сложно идеально выровнять на форме/опалубке и он даст помутнение в местах соприкосновения со смолой. Этот слой потом нужно будет вышкурить.
Соответственно нужно подготовить инструменты для шлифования, ну или хотя бы набор абразивной бумаги разной зернистости для ручной шлифовки.
Не забудьте подготовить средства индивидуальной защиты для себя любимого) Это перчатки, респиратор, защитные очки. Не станет лишним одноразовый малярный комбинезон и шапочка, т.к в жидком состоянии смола словно притягивает к себе любую пылинку, ворсинку, волосинку…)
Накройте полиэтиленом пол и другие горизонтальные поверхности в зоне «поражения» смолой, что бы сохранить их чистыми.
Еще вам понадобятся емкости для измерения и смешивания компонентов. Весы, с точностью до 1 гр. Либо мерные стаканы, т.к. некоторые смолы смешиваются по объему, а некоторые только по весу, как ЭпоксиМастер.
Как подсчитать необходимое кол-во эпоксидной смолы
В инструкции к эпоксидной композиции может быть указан примерный расход смолы. Чем хороша эпоксидная смола, так это тем, что она не дает усадки, т.е. сохраняет свой первоначальный объем.
ЭпоксиМастер расчитывается исходя из данных, что на 1м.кв. при толщне 1 мм расходуется около 1.1 кг смеси.
Соответственно на столик размером 1 м.кв толщиной 5мм вам понадобится 4 набора ЭпоксиМастер по 1.35 кг.
Заливаем нашу столешницу. Инструкция
Внимательно ознакомьтесь с инструкцией к набору смолы!!! Ознакомление с этим документом убережет вас от возможных сюрпризов в процессе.
Подготавливаем форму или собираем опалубку. Обязательно убедитесь в герметичности формы/каркаса. Сквозь малюсенькую трещинку может вытечь буквально весь ваш будущий стол. Щели можно заклеить герметиком, пластилином, термо-клеем или парафином.
Обработайте форму или каркас разделительным составом. Выровняйте по уровню!
Деревянные части будущей столешницы должны быть сухими! НО, даже сухое дерево в процессе заливки может выделять воздух.
Что делать в этой ситуации?
Перед заливкой деревянные детали в местах соприкосновения со смолой желательно прогрунтовать. Для этих целей можно использовать собственно саму смолу (готовую смесь) либо лак для мебели (полиуретановый к примеру).
Это не только спасет от выделения воздуха из дерева, но и не позволит мигрировать красителям по волокнам древесины, в случае заливки окрашенной смолой.
И так, форма/каркас готовы к работе. Деревянные детали прогрунтованы и высушены. Приступаем к подготовке смеси. Мы будем говорить о наборе для заливки ЭпоксиМастер 2.0
Если необходимо смолу заколеровать, то мы добавляем краситель только в компонент А (смола), до введения в него компонента Б (отвердитель). Добавлять следует совсем маленькими порциями, буквально на кончике зубочистки, до тех пор, пока не получите цвет желаемой интенсивности.
Тщательно размешиваем, до однородности. Что бы лучше и быстрее разошелся пигмент, компонент А можно подогреть до 30-40 градусов (поставить возле радиатора или на водяной бане)
Далее, смешиваем наши компоненты 100:35, как указано в инструкции.
Т.к. у нас состав с временем жизни более 7 часов, то больше подогревать наши компоненты смысла нет, воздушные пузырьки все успеют выйти наружу и без этих манипуляций. Смесь тщательно перемешиваем, не забываем промешивать в середине и по краям стенок. Неоднородность смеси погубит все ваше изделие! Где то смола застынет, где то останется липкий слой, а где то все останется жидким. Такое «изделие» уже не спасти(
Теперь наливаем тонкий слой смолы на дно формы, выкладываем наши элементы декора (Внимание! Деревянные элементы, листья, картинки, могут всплывать!!! Тогда их можно оставить в тонком слое смолы, почти до полного отверждения слоя, так сказать приклеить на нужной вам глубине.) Выливаем приготовленный состав в форму, если толщина заливки не превышает 5 см, то заливаем одним разом.
ВНИМАНИЕ! Лить смолу нужно тонкой струйкой в одну точку, можно наливать по наклонной палочке, опущенной в форму. Чтобы в углах не образовалось внутренних пустот, перед заливкой смочите их готовым заливочным составом.
Если же требуется отлить изделие толщиной 6 и более см, заливаем в два этапа, двумя слоями. Между слоями должно пройти от 1 до 2 суток.
Если вам кажется, что пузырьки выходят плохо (возможно в помещении прохладно) можно подогреть поверхность смолы строительным феном или просто вспрыснуть из пульверизатора ацетоном, это снизит поверхностное натяжение и позволит воздушным пузырькам выходить быстрее.
И так, с заливкой мы закончили.
Изделие оставляем отверждаться, желательно оградить нашу форму от оседания пыли на поверхности.
Отверждение займет не менее 2 суток! Ускорить процесс можно повышением температуры, но очень аккуратно, т.к. слой достаточно большой, объем смолы тоже. Избегайте перегрева смеси иначе это приведет к обильному образованию воздушных пузырьков или деформации изделия, растрескиванию, появлению кратеров.
Полировка/шлифовка готового изделия
Готовым изделие считается после завершения постотверждения, подробнее об этом вы можете прочитать в инструкции к вашей смоле. Постотверждение позволяет вашему изделию достичь своих максимальных свойств. Если нет возможности произвести постотверждение или по инструкции оно не требуется (не обязательно), дайте вашему изделию набрать прочность. При температуре 22 -25°С на это уходит 5-7 суток.
Ну а теперь можно приступать к шлифовально-полировальным работам.
Внимание! Смачивайте поверхность водой, что бы избежать перегрева вашего изделия, иначе смола начнет плавиться и забивать абразивную бумагу. Ну или выбирайте режим оборотов не приводящий к перегреву.
Последний штрих — покрытие изделия полиуретановым лаком, устойчивым к УФ, в несколько слоев, с промежуточным шлифованием. Это спасет ваш шедевр от желтения под воздействием солнечных лучей и придаст гораздо более яркий блеск изделию, чем полировка.
Особенности ухода за столешницей из эпоксидной смолы
Категорически нельзя ставить только что снятые с плиты кастрюли, чайники и сковородки!!! Оплавится столешница.
Не рекомендуется использовать агрессивные и абразивные чистящие средства. Поверхность может помутнеть, потерять блеск.
Желаем творческих успехов и вдохновения=)
У вас Все получится!
Дерево и эпоксидная смола: как залить
На чтение 6 мин. Опубликовано
Эпоксидная смола – популярный инструмент для современных дизайнеров. На ее основе домашние мастера изготавливают оригинальные и эксклюзивные изделия. Очень красиво и необычно смотрится дерево и эпоксидная смола – смолистая субстанция отлично сочетается с опилами, древесиной различных пород, отдельными веточками.
Преимущества и недостатки эпоксидки при работе с деревом
Работа с деревом и эпоксидной смолой – увлекательное занятие. Зная, как правильно работать с эпоксидкой, можно создать удивительные по красоте вещи. Если раньше такой материал использовали при заливке различных поверхностей, то сейчас ее активно применяют в своей работе и дизайнеры. Популярность смолистая субстанция получила благодаря своим многочисленным достоинствам:
- низкому уровню истираемости;
- высокой прочности изделий и их долговечности;
- универсальность – эпоксидке можно придать любую форму;
- после полимеризации готовое изделие легко подвергается любой дополнительной обработке;
- возможность применения различных красителей.

Но эпоксидная смола для дерева обладает и некоторыми недостатками. Например, эпоксидка начинает проявлять свои заявленные качества только после соединения ее со специальным отвердителем. Смолистое вещество становится полностью безопасным только после отвердевания. В процессе работы необходимо использовать личные средства защиты и постоянно проветривать рабочее помещение.
Для дизайнерских работ лучше использовать ювелирную эпоксидку, она намного качественнее, но и обладает более высокой стоимостью.
Технологические особенности
Разбирая вопрос, как залить дерево эпоксидной смолой, нужно учитывать некоторые особенности такого материала. Структура дерева неоднородная, и внутри нее могут скапливаться воздушные пузырьки. А при смене температурного режима древесина начинает изменяться (расширяться либо сжиматься). Скопившийся воздух начинает выходить на поверхность, портя готовую работу.
Чтобы этого не допустить, при заливке смолой дерева, необходимо учитывать температуру рабочего помещения: а именно спустя 2–3 часа после окончания работ обеспечить температурный режим в +20–25⁰С. Если запланировано заливать толстый эпоксидный слой, то весь процесс нужно сделать в два этапа – так минимизируется риск появления и выхода воздуха.
Как правильно пропитывать древесину
Прежде чем использовать эпоксидные смолы для заливки древесины, рабочий материал (дерево) необходимо нагреть. Такой процесс приводит к расширению древесных пор, и более качественному проникновению смолы. После отвердевания поверхности заливку подвергают необходимой финишной обработке.
Качество итоговых работ непосредственно зависит и от правильного соотношения пропорций смолы и отвердителя. В классическом варианте на 10 частей эпоксидки добавляют 1 часть катализатора.
Как устранить появление воздушных пузырьков
Если все меры были предприняты, но на поверхности смолистой субстанции возникли пузырьки воздуха, их можно удалить. Подогревать поверхность не стоит – это приведет к появлению новых воздушных карманов. Стоит использовать один из следующих вариантов:
- С помощью тонкой иглы аккуратно проткнуть пузырь.
- Обрызгать поверхность спиртовым раствором, используя пульверизатор.
- Слишком крупные воздушные карманы просверливают. Образовавшиеся полости вычищают, поверхность обезжиривают и наносят второй слой заливки.

Варианты использования эпоксидки в дизайне
Для дизайнерской работы с деревом лучше использовать прозрачные эпоксидные смолы. Такой состав выделяет все элементы и подчеркивает красоту дерева. Очень оригинально смотрятся изделия, где использовалась заливка смолы с добавлением к ней пигмента.
Совет. При работе с красками лучше выбирать колеровочные составы той же марки, что и используемая эпоксидка.
Существует множество различных дизайнерских приемов для работы с деревом и смолой. Например, добавление к составу опилок, блесток, сухоцвета. А при использовании люминесцентных красок изделие станет просто фантастическим (светящиеся в темноте ступени не дадут оступиться, а различные подсвеченные украшения подчеркнут любой образ). Для получения эффекта нежно-молочных разводов к смоле при заливке добавляют водяные капельки. Что можно сделать?
- Оригинальная мебель. Необычными становятся мебельные элементы с заливкой из эпоксидки. Столы, стулья, даже двери можно выделить и сделать эксклюзивными. При работе можно использовать любые творческие задумки.
- Необычные полки. Также можно создать оригинальные и необычные полочки. Сделать их можно и самостоятельно, опираясь на заданные размеры и подчеркивая общий стиль комнаты.
- Барные стойки или столешницы. Такие модели не просто подчеркивают стиль помещений, но и могут создавать отдельные «островки» со своим эксклюзивным дизайном, становясь центральной точкой интерьера.
- Лампы. Из эпоксидки и дерева можно творить настоящие шедевры, даже различные модели настольных/напольных ламп, светильников и ночников.
Эпоксидку используют не только для создания необычных и неповторимых деталей интерьера. Этот материал добавляет прочности обрабатываемому изделию, значительно продлевая срок его службы. Например, лестница из эпоксидки, даже, несмотря на высокую стоимость рабочего материала, в конечном итоге обойдется значительно дешевле работ по классической схеме установки лестничных пролетов.
Для получения безукоризненного итогового результата работы с эпоксидной смолой следует грамотно подходить к выбору этого материала.

Как выбрать подходящую эпоксидку для дерева
Все эпоксидные смолы, используемые для работ, подразделяются на две крупные группы. Это:
- Конструкционные материалы. Их применяют в различных сферах промышленности. А также для ремонта, тюнинга, судостроения и т. п. Для такой группы эпоксидок от субстанции требуются повышенные показатели ударопрочности и твердости.
- Декоративные (или ювелирные). Эти материалы больше всего подходят для дизайнерских задумок. Они прозрачные и позволяют увидеть всю структуру дерева. Также их активно используют для создания картин, бижутерии, скульптур и разных сувениров.
Для дизайнерских работ используются ювелирные эпоксидные смолы. Их важным качеством является устойчивость к воздействию ультрафиолета (в процессе длительного времени покрытия не желтеют). К достоинствам относится и повышенная текучесть. Но декоративные эпоксидки обладают более высокой ценой.
Современный рынок отделочных материалов предлагает довольно обширную линейку эпоксидных смол. Чтобы не растеряться при выборе, учитывайте следующие рекомендации:
- Для заливки больших поверхностей, например, столешниц или барных стоек требуется толстый слой эпоксидки. Причем масса не должна перегреваться и желтеть. Для выполнения такой задачи лучшим выбором станет смола марки Epoxy River.
- Для работ более мелких лучше подходит универсальная эпоксидка. Она достаточно быстро отвердевает и может заливаться как тонким покрытием, так и толстым слоем. Для таких целей выбор остановите на фирме Aquaglass Citrus.
- А для создания уникальных украшений и бижутерии важным требованием к смоле становится отсутствие токсичности, стойкость к деформациям и пожелтению и экономичность при использовании. Учитывая, что подобные работы проводятся в домашних условиях, наиболее безопасной является смола от компании Diamant.
Выводы
Такой материал, как эпоксидная смола, смело можно отнести к уникальным. Смолистая субстанция становится прекрасным помощником современных дизайнеров. А сочетания эпоксидки с деревом позволяют создавать неповторимые по красоте различные изделия.
Столешница из эпоксидной смолы – как самостоятельно создать шедевр
Делаем самостоятельно столешницу
Поскольку столешницу из эпоксидки можно сделать с основой или без нее, то рассмотрим оба варианта – каждый имеет свои особенности.
Столешница, выполненная только из эпоксидной смолы без основы, смотрится очень эффектно благодаря своей прозрачности и вкраплениям декоративных элементов. При определенных навыках такую столешницу можно сделать с самыми замысловатыми очертаниями и оригинальным 3D рисунком в массиве застывшей смолы.
Делают прозрачную столешницу, используя в качестве формы стекло:
- нужных размеров и формы стекло тщательно очищают, высушивают и обезжиривают ацетоном;
- перед заливкой поверхность стекла натирают восковой мастикой, которую после застывания полируют сухой ветошью;
- в качестве бортиков для формы используют полированные алюминиевые уголки, внутреннюю поверхность которых обрабатывают парафиново-скипидарной смесью — это позволит без проблем вынуть застывшую столешницу из формы;
- уголки крепятся к нижней поверхности стекла с помощью оконной замазки.
Возможен и другой вариант, когда полностью изготовленная из эпоксидной смолы столешница вставляется затем в рамку из подходящего по стилю изделия материала.
Для того, чтобы заливка застыла должным образом, должно пройти 2-3 дня. До этого снимать столешницу с формы нельзя.
Совет
Чтобы не пришлось сверлить отверстия в застывшей смоле для крепления ножек, предусмотрите это заранее, наметив места будущих креплений и укрепив в форме небольшие отрезки трубы необходимого диаметра. После застывания отрезки вынимаются, а на их место вкручиваются крепления для ножек.
Столешницу на деревянной основе сделать проще, поскольку смола для столешниц заливается на уже подготовленную поверхность. При этом, как и в случае со стеклянной формой, по краям столешницы делаются бортики – они могут быть впоследствии сняты. А можно применить вариант, когда деревянные бортики являются частью столешницы, а образовавшаяся «ванна» заливается смолой.
Очень красиво смотрятся столешницы, где деревянные части чередуются с прозрачными вставками. Для этого также можно воспользоваться стеклом в качестве основы, на котором выкладываются деревянные фрагменты, а расстояния между ними заливаются эпоксидной заливкой.
Если планируется использовать в качестве основы старую доску, то работу нужно провести в два этапа: сначала в доске немного углубляются уже имеющиеся каверны и трещинки, которые затем заливаются подкрашенной жидкой эпоксидной смолой. После застывания первого слоя заливается уже вся столешница, при этом залитые ранее углубления красиво выделяются на прозрачной поверхности.
После того, как работа по заливке окончена, необходимо защитить поверхность на время застывания от попадания влаги, пыли и насекомых – они могут существенно испортить всю работу. Для этого над столешницей следует натянуть полиэтилен, укрепленный на заранее подготовленном каркасе.
После полной кристаллизации материала поверхность полируется и покрывается защитным лаком.
Мастер-класс смотреть онлайн: Заливка украшений из эпоксидной смолы и дерева
Сейчас очень популярными становятся украшения из эпоксидной смолы и дерева. Загадочные и эффектные, они привлекают внимание к своей хозяйке и дают огромнейший простор фантазии для применения их в абсолютно различных стилях — от романтики до бохо.
Популярность этому направлению придали украшения Бритты Бекман. В 2013 году немецкий дизайнер Бритта Бекман (Britta Boeckmann) переехала из Германии в Австралию и начала заниматься изготовлением украшений ручной работы. На данный момент талантливая девушка уже успела обзавестись собственной ювелирной студией и продает свои изделия под брендом «BoldB».
Работа Бритты Бекман:
Мы сделаем украшения на эту же тему, однако, немного усовершенствуем их — они будут светиться в темноте загадочным нежным светом благодаря специальным пигментам.
Для данного урока применялись:
1. Эпоксидная прозрачная смола.
2. Кусочки акрила (можно картона, полиэтилена). Стекло использовать нельзя (смола имеет высокую адгезию к стеклу).
3. Светящиеся пигменты для смолы (люминофор), флуоресцентные пигменты для придания желаемого оттенка.
Необязательный этап, но в данном случае показано украшение, светящееся в темноте загадочным светом.
4. Срезы дерева по вашему вкусу.
5. Инструменты: шлифмашина, ручная фрезерная машина Дремель.
6. Шлифовальные пасты (можно использовать автопасты для шлифовки пластиков).
7. Если в инструкции к смоле сказано, что смола смешивается по весу, используйте электронные весы. Если сказано, что по объему, используйте шприцы.
8. Пистолет с термоклеем (для герметизации нашей опалубки). Вместо него также можно использовать восковой или скульптурный пластилин. Наша задача — плотно заделать швы между деталями опалубки, чтобы смола не протекла.
Мы не будем останавливаться очень подробно на способах заливки смолы, обработки дерева и тонкостях применения люминофорных пигментов, это можно прочитать в специализированных наших статьях. Здесь будет показан именно способ изготовления подобных произвольных форм.
Итак, приступаем
Делаем опалубку
Для начала, включаем фантазию и представляем, какого вида украшение мы хотим, где должна быть смола, где дерево, какие должны быть цвета и переходы. Изобразим приблизительный эскиз.
Склеиваем кусочки акрила пистолетом с термоклеем (вы также можете использовать толстый картон, полиэтилен), кладем на дно срезы дерева по задумке нашей композиции, приклеиваем их термоклеем ко дну опалубки, чтобы они не всплывали в смоле.
Акрил используется потому, что смола к нему не прилипает, как, скажем, к стеклу, и затем вы легко сможете снять его.
Вкратце остановимся на основных особенностях люминофоров.
Если добавить просто люминофорные пигменты, на свету смола будет молочно-сероватой, без голубого оттенка. Оттенок можно придать использованием флуоресцентных (ярких) пигментов.
Суть люминофорного пигмента в том, что он «заряжается» на ярком свету и затем, в темноте, светится и отдает свой заряд (полученную энергию). Чем сильнее «зарядить» его на ярком свету, тем дольше он будет светиться в темноте.
Люминофоры бывают с разным размером частиц (зерна). Для смолы чаще используются люминофоры с мелким зерном (5-15 мкм), чтобы более мелкий пигмент красиво распределился в смоле в виде взвеси, а не осел на дно, как более тяжелые крупные частицы.
Смешивание смолы.
Отмеряем смолу по весу на электронных весах (основа, затем отвердитель). Если смола смешивается по объему, работаем со шприцами. В нашем случае, смола смешивается 100 г основы (компонент А) на 50 г отвердителя (компонент В) 2 к 1.
Добавляем люминофорные и флуоресцентные пигменты (зеленый, голубой). Также, бывают сразу дуопигменты, сочетающие оба этих свойства.
Перед заливкой, можно поставить смолу в другую емкость с горячей водой (не более 50-60 град.). Смола разжижится и пузырьки из нее выйдут легче, так как они у вас неизбежно появятся при смешивании смолы и пигментов.
Смешивайте смолу аккуратно, медленными движениями по кругу, уделяя особенное внимание стенкам посуды, плоской деревянной палочкой, не менее 2 минут.
Свечение заливки в темноте. Очень эффектно, не правда ли?:)
Обратите внимание, пигмент придает смоле мутноватость, и она не будет абсолютно прозрачной.
Время застывания смолы зависит от вида смолы и объема ее заливки, правильности смешивания с отвердителем, температуры в помещении. Прохладное помещение может значительно увеличить время полимеризации.
Желательно накрыть отливку куполом, чтобы уберечь от попадания пылинок, летающих мелких шерстинок и прочих радостей, которые могут испортить внешний вид отливки.
Через 24 часа пробуем смолу и, если она застыла, разбираем опалубку. Смола дает усадку (фото), если вы хотите этого избежать, долейте смолы через 6-8 часов.
Время начать делать из нашего красивого брусочка украшения той формы, что задумано.
Работайте в средствах индивидуальной защиты дыхания, в перчатках, в хорошо проветриваемом помещении.
Шлифуем шлифмашиной всю поверхность брусочка, чтобы полностью выровнять поверхность.
Вырезаем формы по своему желанию, ориентируясь на предварительные эскизы.
Не обходится и без расстройств (отпал кусочек смолы с одного края).
Используя Дремель (это торговая марка инструмента, вы, конечно, можете использовать другие подобные машинки), обрабатываем края заготовок.
И вот они — заготовки, ожидающие финишной полировки.
Сверлим дырочки в нашей будущей заготовке и шлифуем ее (наилучший результат дадут применение шлифмашины и профессиональных шлифпаст. По опыту — обычная паста ГОИ и неподходящие пасты не дадут настолько красивого результата, как профессиональные шлифовальные пасты для смолы).
Также при желании вы можете покрыть заготовку специальным лаком.
Часто мастера дополнительно обрабатывают дерево маслами (например, льняным) и восками для защиты и улучшения внешнего вида.
Тут показано только общее направление изготовления мастерами подобных изделий, способов существует несколько.
Удачного творчества!
Эпоксидная смола для заливки столешницы: какую выбрать? — Эпоксидка
Эпоксидная смола уникальный и простой в использовании материал для творчества. Смолу применяют не только в качестве клеевого состава. На ее основе создается мебель, украшения, предметы интерьера и дизайна. Но не все так просто. Чтобы создать, что-то уникальное необходимо не только знать все тонкости работы с эпоксидной смолой, но и правильно выбирать материал для творчества.
Преимущества и недостатки эпоксидной смолы

Любой строительный материал имеет, как свои плюсы, так и минусы. Зная положительные и отрицательные стороны материала намного легче работать с ним. Так же эти знания помогают определиться с конструктивными особенностями будущей модели. При создании столешницы из эпоксидной смолы нужно учитывать вес готовой столешницы и какая на нее будет воздействовать нагрузка.
Преимущества эпоксидной смолы для создания столешницы:
- Залитая в форму смола не подвергается усадке. Не усаживается материал, потому что в процессе его застывания не происходит испарения части состава.
- Жидкая по консистенции смола после заливки образует совершенно ровную поверхность. Обладает способностью проникать в любые щели и полностью покрывать неровную поверхность.
- Столешница из эпоксидной смолы очень прочная. Ее тяжело поцарапать или сломать.
- Эпоксидная смола не пропускает влагу и не накапливает ее. Также на ее поверхности не образуется плесень и грибок.
- Затвердевшая смола не меняет цвет как из-за воздействия ультрафиолета, так и по прошествии долгого времени.
- Материал сравнительно не дорогой.
Недостатки эпоксидных смол:
- Перед работой необходимо в точности соблюсти пропорции отвердителя и смолы.
- Работа со смолой требует внимательности к температуре и помещению. Помещение должно проветриваться и быть достаточно теплым. Не нужно забывать, что жидкая смола токсична и может нанести вред здоровью.
- Неправильное охлаждение в процессе застывания приводит к образованию мутных взвесей или к микротрещинам. Состав необходимо заливать разогретым и не охлаждать принудительно.
Эпоксидная смола капризный материал для новичков, но если соблюдать пропорции при смешивании, правила безопасности и температурный режим в помещении можно быстро научится применять смолу в творчестве.
Марки эпоксидных смол
Эпоксидные смолы в основном различаются по густоте состава при стандартной консистенции смешиваемых составных веществ. Если раньше смолы выпускались только для промышленного использования и были очень токсичными по составу, то сегодня некоторые компании выпускают экологически чистые смолы для домашнего использования.
QTP-1130

Низковязкая смола не содержащая растворитель. Хорошо подходит для новичков создающих небольшие конструкции. Обладает высокой прозрачностью. Часто используется при заливке столешниц из слэба, камня или различного декора. Не желтеет. Ровно заполняет форму для заливки и не усаживается.
Характеристики:
- Прочность сжатия – 83 МПа;
- Прочность разрыва – 50 МПа;
- Прочность на изгиб – 79МРа;
- Термостойкость: + 50 градусов при постоянном воздействии, +80 при воздействии до 7 дней, +100 градусов при воздействии до 12 часов.
Смола QTP-1130 не токсична после высыхания. Не имеет неприятного химического запаха в жидком виде. Рекомендуется к использованию при температуре до + 40 градусов.
Арт-Эко

Двухкомпонентная, низковязкая смола. Для уменьшения вязкости, комплектуется растворителем. Максимальная толщина для заливки 7 мм. Хорошо подходит для смешивания с колером. Одним из недостатков является необходимость строгого соблюдения пропорций, смешиваемых элементов. Подходит для заливки монолитных конструкций и покрытий, для изготовления столешниц и бижутерии.
- Прочность сжатия – 80;
- Прочность разрыва – 40;
- Прочность изгиба – 70.
Арт-эко устойчива к воздействию света, тепла до +70 градусов и к механическим повреждениям. Очень прозрачна, но со временем желтеет. Использование с применением колера обязательно. Смола не имеет резких химических запахов, как в жидком, так и в твердом виде.
ЭД-20

Смола для универсального применения. Изготовляется по ГОСТу, поэтому во многом не подпадает под современные характеристики. Является высоковязкой, что во многом усложняет работу с ней. Часто возникают воздушные пузырьки. Новичкам крайне сложно работать с этой смолой. Со временем немного желтеет, использование колера обязательно. Главным достоинством состава является высокая прочность, стойкость к механическим воздействиям.
- Прочность сжатия – 85;
- Прочность разрыва – 90;
- Прочность на изгиб – 140.
У данной эпоксидной смолы много поклонников и противников. Главным образом негативные отзывы возникают по причине неопытности при работе с ЭД-20.
CHS Epoxy 520

Эпоксидная смола от Чешских производителей. Является самой прозрачной по консистенции из всех марок, представленных на рынке. Лучший выбор при создании изделий с большим количеством сложного декора. При декорировании возможно использование сухих и свежих цветков и листьев, металл, дерево, камни. При смешивании с отвердителем марки 921 ОП становится высоко пластичным. Пластичность готовой столешницы очень важна, так как нагрузка может быть неравномерной. CHS Epoxy 520 является аналогом отечественных смол марок ЭД20 и ЭД 22. Но отличается простотой применения. После нанесения не возникает пузырьков воздуха и со временем состав не желтеет.
- Прочность сжатия — 80;
- Прочность разрыва – 75;
- Прочность изгиба – 92.
Эта марка смолы подойдет, как новичкам, так и профессионалам. Очень хорошо подходит для создания больших по объему столешниц. Глубина заливки 1.5 – 2 сантиметра для первого слоя.
Crystal Glass

Смола от отечественного производителя. Подходит для заливки мелких конструкций и бижутерии, а также столешниц большого объема. Работать с этой маркой очень легко, так как ее текучесть зависит от количества отвердителя. Особенностью CrystalGlass является необходимость настаивания перед заливкой. Во время настаивания состав густеет, что позволяет найти необходимый уровень загустения. Смола очень хорошо растекается и заполняет весь рельеф заготовки и элементов декора. Не образует пузырей и мутных хлопьев. Затвердевшая столешница обладает прочностью, антикоррозийной устойчивостью и не желтеет со временем. В состав CrystalGlass можно добавлять колер.
- Прочность сжатия – 75;
- Прочность разрыва – 70;
- Прочность на изгиб до 85.
CrystalGlass одна из марок эпоксидных смол, подходящих для начинающих изготовителей столешниц. При работе с ней нужно только подобрать правильную консистенцию тягучести состава.
ПЭО-610КЭ

Еще одна марка смолы изготовленная согласно ГОСТу. Буква «Э» указывает на высокую степень эластичности затвердевшего состава. Это позволяет изготавливать крупные столешницы, с большим запасом прочности. Глубина заливки одного слоя составляет 0.7см. при этом состав полностью затвердевает через 54 часа. Компаунд ПЭО-610КЭ позволяет заливать сложные декоративные элементы без возникновения неровностей, пузырьков и пустот. Готовая столешница обладает запасом прочности на разрыв до 75МРа и на изгиб до 90 МПа. Не желтеет, не имеет неприятного химического запаха. Обладает высокой влагоотталкивающей способностью. В комплекте с основным компонентом отвердителя нет. Его нужно приобретать отдельно. Смола проста в применении и позволяет с легкостью работать даже новичкам.
EpoxAcast 690

Также отечественная эпоксидная смола. Обладает высокой прозрачностью и жесткостью в твердом состоянии. Не пластична. При работе с ней можно заливать до 5 см первого слоя. Подвержена усадке по мере застывания. Больше подходит для изготовления бижутерии. При создании монолитных конструкций больших объемов требуется определенный опыт. Прочность на изгиб до 140 МПа, прочность разрыва 120МРа. При своей повышенной тягучести и низкой эластичности EpoxAcast 690 можно заливать средние по сложности элементы декора. Материал не желтеет, но можно добавлять в состав колер. Не имеет неприятного запаха.
MG EPOX STRONG

Сверх прозрачная смола из Германии. Самый популярный заливочный состав у профессионалов. Обладает высокой прозрачностью, не желтеет и не усаживается. Позволяет работать со сложно декорируемыми конструкциями больших объемов. Не пропитывает слои песка и не отделяет песчинки. Отлично подходит для заливки фотографий, цветов и листьев сохраняя яркие цвета. Застывает в течение 3 суток. За это время приобретает прочность до 90 МПа и эластичность на изгиб до 85МРа. Многие мастера рекомендуют изготавливать столешницы и конструкции с повышенными требованиями прочности именно этой маркой смолы.
Epoxy CR 100

Самая безвредная по химическому составу смола. Рекомендуется, как универсальная смола для работы, как с мелкими моделями и бижутерией, так и для изготовления столешниц. Подходит для заливки слэба, сложных декоративных элементов и фотографий. Обладает высокой прочностью в твердом состоянии и большом коэффициентом прозрачности. Не желтеет и позволяет добавлять в состав колер. Застывает в течение 50 часов. Не подвержена коррозии, ультрафиолетовому излучению и влагонакоплению. Подходит для работы новичка, из-за простоты использования и жидкой консистенции без появления микротрещин и пузырьков.
При выборе эпоксидной смолы важно знать все нюансы ее состояния в жидком и твердом состоянии. Перед началом основной работы требуется попрактиковаться в смешивании и достижении правильной консистенции.
Важно очень внимательно ознакомиться с сопроводительной инструкцией.
Эпоксидная смола для заливки слэбов и столешниц
Для заливки пустот и полостей в древесине, а также выравнивания поверхностей у слэбов и столешниц мы рекомендуем приобрести эпоксидную смолу. Этот двухкомпонентный материал после отверждения образует прочную, идеально ровную и прозрачную поверхность. Подобные материалы, позволяющие создавать монолитную форму, заполняя пустоты и трещины, иногда называют компаундом. В компаунд можно добавлять красители и различные наполнители для создания дополнительных эффектов.Основными сферами применения эпоксидной смолы являются прозрачная заливка слэбов, предназначенных для изготовления столешниц, заливка трещин и выпавших сучков в древесине, изготовления рекламной и сувенирной продукции.
Предлагаем воспользоваться некоторыми рекомендациями при работе с заливочной эпоксидной смолой.
Основными требованиями являются:
— температура при работе — от +20°С (мин. +18°С),
— умеренная влажность в помещении (обычная комнатная),
— оптимальная толщина заливки — 20 мм на любой площади,
— стандартное соотношение смолы и отвердителя: 100 : 45 (по весу)
— допускается толстослойная заливка при условии уменьшения количества отвердителя до 30%.
Как правильно смешивать компоненты:
Обязательным правилом является двойное перемешивание, т.е. сначала в одной емкости размешиваем 3-5 минут, затем переливаем в другую чистую емкость и перемешиваем повторно 2-3 минуты. Визуально материал должен стать однородным, без разводов.
Заливка изделий:
После заливки, не требуется удаление воздушных пузырей из массы и с поверхности, благодаря специальным добавкам воздух выходит самостоятельно. В определенных случаях, воздух с поверхности необходимо удалить спустя некоторое время, если у изделия есть углубления.
Эффективно помогает газовая портативная горелка — достаточно на пол секунды поднести к отливке на место образования пузырей.
Удаление пузырей можно выполнить механическим способом, для этого подойдёт иголка, просто прокалываем их, либо выгоняем за пределы отливки.
Также подойдет строительный или бытовой фен, при разогреве поверхности пузыри лопаются.
Работа с эпоксидной смолой и деревом:
Места контакта древесины со смолой перед заливкой рекомендуется загрунтовать. В качестве грунтовочного состава мы предлагаем использовать эпоксидную композицию, состоящую из грунта и отвердителя (имеется в продаже). При заливке эпоксидной смолой после грунтования воздух выходит самостоятельно, без грунтовки пузыри могут скапливаться на краях дерева.
Правила смешивания:
-
количество компонентов подбирается по весу, а не по объему,
-
перемешивание может производиться как в ручную, так и с помощью миксера.
Техническое описание.
Соотношение компонентов ( А+В ) |
100:45, допустимы отклонения |
Время жизни после смешивания (100 гр) |
не менее 360 минут |
Отверждение |
48-72 часа ( зависит от температуры и толщины слоя ) |
Сухой остаток |
97,3 % |
Транспортировка при отрицательной t |
допускается |
Хранение |
+5 °С — +25 °С (избегать прямых солнечных лучей) |
Срок годности |
12 месяцев |
Расход на м2 при толщине 1 мм |
1,1 кг |
Средства защиты органов дыхания |
Рекомендуются |
Минимальная температура применения |
+18 °С |
* Для определенных задач, необходимы тестовые испытания.
Мебель из древесно-полимерного композита с низкой воспламеняемостью — ScienceDaily
Дерево — популярный материал в дизайне интерьеров, но его водопоглощение ограничивает его использование в ванных комнатах, где натуральное дерево легко обесцвечивается или покрывается плесенью. Ученые и партнеры Fraunhofer разработали древесно-полимерный композиционный материал для мебели, устойчивый к влажности и обладающий низкой горючестью.
Ресурсосберегающие древесно-полимерные композиты (ДПК) — это последняя тенденция в материалах для садовой мебели и других наружных применений, особенно для террасных покрытий, а также для обшивки и ограждений.В рамках спонсируемого ЕС проекта LIMOWOOD исследователи из Института исследования древесины им. Фраунгофера, Wilhelm-Klauditz-Institut WKI в Брауншвейге теперь сотрудничают с промышленными партнерами в Бельгии, Испании, Франции и Германии в разработке материалов, подходящих для прессования в влагостойкие плиты WPC для изготовления внутренней мебели.
Эти плиты состоят примерно на 60 процентов из древесных частиц и на 40 процентов из термопластического материала, обычно полипропилена или полиэтилена.Как деревянные, так и пластмассовые компоненты могут быть получены из вторичного сырья. Древесный компонент в плитах WPC может быть заменен другими продуктами из лигноцеллюлозы, полученными из волокнистой части растений, таких как конопля или хлопок, или шелухой рисовых зерен и семян подсолнечника. Все эти материалы полностью пригодны для вторичной переработки. Более того, прессованные плиты WPC, произведенные исследователями WKI, не содержат формальдегид. «Спорный вопрос о выбросах формальдегида из-за связующего, используемого в обычных прессованных деревянных изделиях, в данном случае не является проблемой», — говорит исследователь WKI д-р.Арне Ширп.
Испытания демонстрируют низкую горючесть плит из ДПК
Выбрав соответствующие добавки, исследователи смогли улучшить огнезащитные свойства своих плит из ДПК. Первоначально они разработали свою формулу в лабораторных масштабах, используя коммерчески доступные антипирены, не содержащие галогенов, которые добавляли в смесь древесины и полимера во время фазы плавления. Первый шаг заключался в определении предельного кислородного индекса испытуемого объекта: этот параметр определяет поведение пластмасс или древесно-наполненных пластиковых компаундов при воздействии огня.Он представляет собой минимальную концентрацию кислорода, при которой материал будет продолжать гореть после возгорания. Чем выше это значение, тем ниже воспламеняемость материала. Ширп и его коллеги получили наилучшие результаты с комбинацией антипиренов, таких как красный фосфор и расширенный графит. Предельный кислородный индекс плит WPC, обработанных таким образом, увеличивается до 38 процентов при условии, что содержащиеся в них древесные частицы также являются огнестойкими. Для сравнения, предельный кислородный индекс стандартной древесно-стружечной плиты составляет 27 процентов, а необработанной плиты ДПК — 19 процентов.Даже в испытании с одним источником пламени, в котором горелка Бунзена прижимается к испытательному образцу, обработанные плиты WPC продемонстрировали высокую огнестойкость. Даже после 300-секундной выдержки доски не загорелись. Напротив, контрольные образцы — стандартной древесно-стружечной плиты и необработанной плиты ДПК — загорелись и продолжали гореть.
Другой особенностью нового материала WPC является то, что он очень мало впитывает воду и поэтому хорошо подходит для использования в ванных комнатах и кухнях.Даже после погружения в кипящую воду на пять часов материал остается неповрежденным, тогда как обычная древесно-стружечная плита в этом испытании была полностью разрушена. Единственным ограничивающим фактором при применении WPC является его неспособность выдерживать высокие статические нагрузки. Но даже здесь оказалось возможным повысить ее прочность на изгиб до уровня, намного превышающего аналогичный показатель у обычных древесностружечных плит, за счет разумного сочетания компонентов материалов.
Древесно-полимерные композиты можно производить разными способами.Наиболее часто используемые процессы — это литье под давлением и экструзия, в которых различные компоненты — древесные волокна, термопластические материалы и добавки — плавятся под высоким давлением при высокой температуре и формуются в непрерывной форме. Команда Арне Ширпа сосредоточила свое внимание на технологии прессования, потому что это лучший способ производить плиты для использования в мебельном строительстве. «Полученные плиты имеют такой же внешний вид, как и цельнодеревянные изделия, и их можно склеивать или скреплять шурупами для создания красивой мебели.Они подходят для всех декоративных, ненесущих элементов ». Но есть много других применений древесно-полимерных композитов, включая наружную облицовку зданий, строительство выставочных стендов и внутреннюю отделку домов и кораблей. В ходе разработки партнеры по проекту LIMOWOOD стремятся заполнить пробел между высокими и низкими сегментами мебельного рынка, который колеблется между дорогими и необязательно экологически безопасными материалами и дешевыми продуктами из ДСП или древесноволокнистых плит, которые в настоящее время в основном производится с использованием связующих на основе формальдегида.Исследователи WKI представят прототипы своих огнеупорных плит WPC на выставке Interzum в Кельне с 5 по 8 мая.
История Источник:
Материалы предоставлены Fraunhofer-Gesellschaft . Примечание. Содержимое можно редактировать по стилю и длине.
,Мебель древесно-полимерный композит пониженной горючести
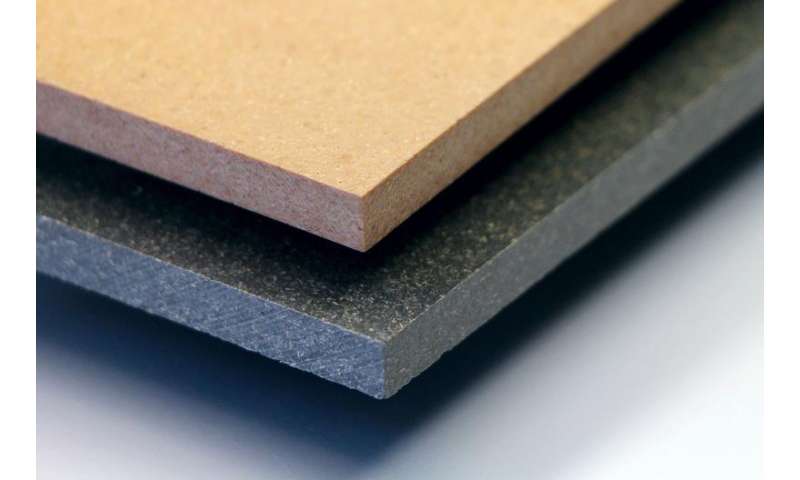
Дерево — популярный материал в дизайне интерьеров, но его водопоглощение ограничивает его использование в ванных комнатах, где натуральное дерево легко обесцвечивается или покрывается плесенью. Ученые и партнеры Fraunhofer разработали древесно-полимерный композиционный материал для мебели, устойчивый к влажности и обладающий низкой горючестью.
Ресурсосберегающие древесно-полимерные композиты (ДПК) — это последняя тенденция в материалах для садовой мебели и других наружных применений, особенно для настилов террас, а также для обшивки и ограждений. В рамках спонсируемого ЕС проекта LIMOWOOD исследователи из Института исследования древесины им. Фраунгофера, Wilhelm-Klauditz-Institut WKI в Брауншвейге теперь сотрудничают с промышленными партнерами в Бельгии, Испании, Франции и Германии в разработке материалов, подходящих для прессования в влагостойкие плиты WPC для изготовления внутренней мебели.
Эти плиты состоят примерно на 60 процентов из древесных частиц и на 40 процентов из термопластического материала, как правило, полипропилена или полиэтилена. Как деревянные, так и пластмассовые компоненты могут быть получены из вторичного сырья. Древесный компонент в плитах WPC может быть заменен другими продуктами из лигноцеллюлозы, полученными из волокнистой части растений, таких как конопля или хлопок, или шелухой рисовых зерен и семян подсолнечника. Все эти материалы полностью пригодны для вторичной переработки. Более того, прессованные плиты WPC, произведенные исследователями WKI, не содержат формальдегид.«Спорный вопрос о выбросах формальдегида из-за связующего, используемого в обычных изделиях из прессованной древесины, в данном случае не является проблемой», — говорит ученый-исследователь WKI д-р Арне Ширп.
Испытания подтверждают низкую горючесть плит ДПК
Выбрав соответствующие добавки, исследователи смогли улучшить огнезащитные свойства своих плит из ДПК. Первоначально они разработали свою формулу в лабораторных масштабах, используя коммерчески доступные антипирены, не содержащие галогенов, которые добавляли в смесь древесины и полимера во время фазы плавления.Первый шаг заключался в определении предельного кислородного индекса испытуемого объекта: этот параметр определяет поведение пластмасс или древесно-наполненных пластиковых компаундов при воздействии огня. Он представляет собой минимальную концентрацию кислорода, при которой материал будет продолжать гореть после возгорания. Чем выше это значение, тем ниже воспламеняемость материала. Ширп и его коллеги получили наилучшие результаты с комбинацией антипиренов, таких как красный фосфор и расширенный графит.Предельный кислородный индекс плит WPC, обработанных таким образом, увеличивается до 38 процентов при условии, что содержащиеся в них древесные частицы также являются огнестойкими. Для сравнения, предельный кислородный индекс стандартной древесно-стружечной плиты составляет 27 процентов, а необработанной плиты ДПК — 19 процентов. Даже в испытании с одним источником пламени, в котором горелка Бунзена прижимается к испытательному образцу, обработанные плиты WPC продемонстрировали высокую огнестойкость. Даже после 300-секундной выдержки доски не загорелись.Напротив, контрольные образцы — стандартной древесно-стружечной плиты и необработанной плиты ДПК — загорелись и продолжали гореть.
Еще одной особенностью нового материала WPC является то, что он очень мало впитывает воду и поэтому хорошо подходит для использования в ванных комнатах и кухнях. Даже после погружения в кипящую воду на пять часов материал остается неповрежденным, тогда как обычная древесно-стружечная плита в этом испытании была полностью разрушена.Единственным ограничивающим фактором при применении WPC является его неспособность выдерживать высокие статические нагрузки. Но даже здесь оказалось возможным повысить ее прочность на изгиб до уровня, намного превышающего аналогичный показатель у обычных древесностружечных плит, за счет разумного сочетания компонентов материалов.
Древесно-полимерные композиты можно производить разными способами. Наиболее часто используемые процессы — это литье под давлением и экструзия, в которых различные компоненты — древесные волокна, термопластические материалы и добавки — плавятся под высоким давлением при высокой температуре и формуются в непрерывной форме.Команда Арне Ширпа сосредоточила свое внимание на технологии прессования, потому что это лучший способ производить плиты для использования в мебельном строительстве. «Получаемые в результате плиты имеют такой же внешний вид, как и цельнодеревянные изделия, и их можно склеивать или скреплять между собой для получения красивой мебели. Они подходят для всех декоративных элементов, не несущих нагрузки». Но есть много других применений древесно-полимерных композитов, включая наружную облицовку зданий, строительство выставочных стендов и внутреннюю отделку домов и судов.Своими разработками партнеры по проекту LIMOWOOD стремятся заполнить пробел между высокими и низкими ценами на рынке мебели, который колеблется между дорогими и необязательно экологически безопасными материалами и дешевыми изделиями из древесно-стружечных или древесноволокнистых плит, которые в настоящее время в основном производятся с использованием связующих на основе формальдегида. Исследователи WKI представят прототипы своих огнестойких панелей WPC на выставке Interzum в Кельне с 5 по 8 мая (Boulevard, B077).
Пеноматериалы на основе древесины
Предоставлено Fraunhofer-Gesellschaft
Цитата : Мебель из древесно-полимерного композита пониженной горючести (4 мая 2015 г.) получено 13 августа 2020 с https: // физ.орг / Новости / 2015-05-древесно-полимерный композит-мебель-flammability.html
Этот документ защищен авторским правом. За исключением честных сделок с целью частного изучения или исследования, никакие часть может быть воспроизведена без письменного разрешения. Контент предоставляется только в информационных целях.
,